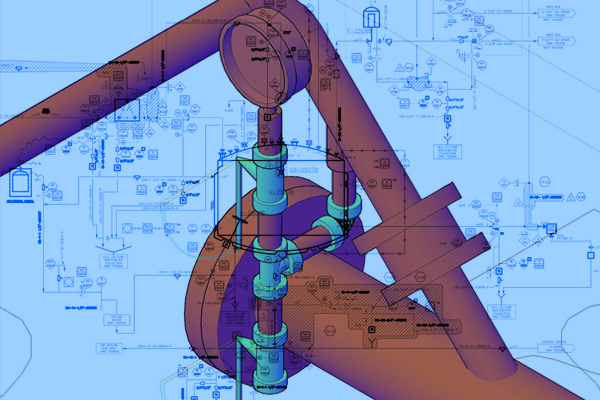
Control System, Instrumentation and Installation Turnkey Solution
The foundation of Hallam-ICS’s project approach is to work cooperatively with Client's User Group and Projects Engineering Group to fully satisfy the project intent.
Challenge
Sanofi (formerly Genzyme) undertook a Cell Culture Expansion Project on their campus in Framingham, MA. This cGMP facility produces Fabrazyme, the only treatment option approved in the U.S. for patients suffering from Fabry Disease.
Hallam-ICS was contracted to provide a turnkey, PLC based control system for the High BOD process waste treatment plant associated with the facility. Hallam-ICS provided software development, panel build to UL508 standards, FAT/SAT and instrument procurement, installation and wiring services.
Solution
Our work also included instrumentation and installation services to support the expansion project. We’ve assembled an in-house team of experienced instrumentation professionals for the bench testing of approximately 1,150 devices for the process control and utility systems. The team was responsible for receipt verification, bench test and installation of instruments supporting Media Prep, Buffer, Media Harvest, Seed Reactors, Chromatography, Micro Filtration, along with various Utility functions including CIP, WFI, Clean Steam, Chilled Water, RO Water, specialty and house gases.
In addition, Hallam-ICS was responsible for the electrical installation of the Process Automation System (PAS). This installation included mounting and wiring more than 30 control panels, network wiring including Foundation fieldbus, Asi bus, Profi bus and traditional 4-20 mA signal wires to the process instruments. More than 2500 control panels terminations and interface functionality with the skid systems and plant process instrumentation were loop checked through the site Delta V control system.
Results
Our team accomplished the following:
- Comprehensive Instrumentation Support: Conducted bench testing, installation, and wiring for approximately 1,150 process control and utility system devices, ensuring seamless integration into critical facility functions such as Media Prep, Seed Reactors, and CIP systems.
- Extensive Electrical Installation: Mounted and wired over 30 control panels, implemented various network wiring protocols, and executed over 2,500 control panel terminations interfacing with the Delta V control system.
- Turnkey Control System Delivery: Delivered a fully compliant PLC-based control system, including software development, UL508 panel fabrication, FAT/SAT execution, and robust instrument procurement and wiring services.