NFPA 652 on a Budget-5 Ways to Minimize the Cost of Compliance
by Chris Giusto on Nov 16, 2021 9:42:02 AM
Most existing facilities will incur costs to become compliant with NFPA 652 (and the relevant referenced standards). Spending money that does not offer a timely and calculable return on investment (ROI) is not something most facilities take lightly.
Blogs posts within this series:
- Combustible Dust Fundamentals and NFPA 652
- What is a Dust Hazard Analysis (DHA)?
- A Practical Guide to 5 Important Properties of Combustible Dust
- 7 Steps to Complete a Dust Hazard Analysis
- I've Completed My DHA, Now What?
Owners and operators must maintain budgets and control expenses to ensure their facility remains profitable and continues to employ their workers.
Safety related projects often do not have the same ROI requirements as typical capital projects, especially when there is some legal or insurance-related requirement for its implementation. However, many facilities attempt to minimize these costs as much as possible because they do not believe they have a direct impact on the bottom line. (I argue that this thinking is incorrect and will discuss this in a future blog.)
The approach of attempting compliance while spending as little as possible often results in sub-standard implementation that will eventually cost more to correct than it would have to do it properly the first time. That said, there are some ways to maximize the value for dollars spent on combustible dust safety and NFPA compliance.
Start by Completing a Dust Hazard Analysis (DHA)
A proper DHA can pay for itself many times over in several different ways. The first and most obvious is avoiding fines for noncompliance. NFPA 652 (and indirectly OSHA) requires owners/operators of facilities handling combustible dusts to complete a DHA. We recently saw news that OSHA fined a facility specifically for not completing a DHA. Remember, the deadline for existing facilities and processes is September 7, 2020, but any new process or facility built after 2015 was required to have a DHA as part of the project.
Legal requirements and fines aside, the real benefit of a DHA comes from identifying the hazards in the facility and prioritizing plans for mitigation. You cannot efficiently (i.e., at a lower cost) make a facility safer and compliant without knowing all the hazards that need to be addressed and having a well-thought-out plan to do so. Even with the best of intentions, a facility jumping into mitigation efforts without completing a DHA could encounter unnecessary expenses and misdirected efforts on lower risk hazards. Worst of all, hazards may be overlooked that would have been identified during the DHA. Remember, the whole point of a DHA is to identify hazards, especially those you did not know existed.
Complete Your DHA in Phases
You must complete a DHA for your entire facility by next year, but you don’t have to do it all at once. There is now a limited amount of time left to take advantage of this strategy, but it could help some facilities to spread costs across this year and next. Start with DHAs for the highest risk systems first, then work toward completing the rest of the facility. Examples of high-risk systems include dust collection systems (dust collectors specifically), hammermilling or other size reduction equipment that generates dust and possibly sparks, and processing involving heat (e.g., drying, roasting). If it is not clear where to start, think about any near-misses with fires, flash fires, or even small-scale explosions in the facility in the past, or contact a consultant for additional assistance.
Think about Combustible Dust Safety During the Design Phase
Completing a project correctly the first time is always cheaper than going back and retrofitting after the project is finished. This only applies to new processes or facilities, but it is worth emphasizing here due to the number of facilities and projects that are not completed properly. Performing a DHA during the design phase of a project ensures compliant safety measures are included before construction begins. Existing facilities face many limitations that often result in increased costs when retrofitting systems for NFPA compliance. Do not put yourself in their position when you have the opportunity to incorporate protection into the design in the most cost-effective manner possible.
Work with an Experienced Firm for Implementation
Modifying existing systems to incorporate combustible dust safety measures is often not a simple task and requires design assistance from an engineering firm. To help ensure this happens for your project, look for a firm with the following experience:
- Combustible Dust Safety Implementation
- Retrofitting Existing Systems
- Knowledge of DHAs and NFPA Standards
- Designing New Systems and Facilities
Experience designing new systems and facilities is particularly important because it is critical to work with someone who understands the implications of modifying your systems and how to accommodate the changes without sacrificing performance. Mistakes made during implementation can negatively impact production, which directly results in lost revenue. Improper installations may be ineffective during an explosion and can provide a false sense of security when a hazard has not really been mitigated, leading to an unexpected and expensive accident.
Procurement & Construction Recommendations
Opportunities to maximize the value of safety dollars do not end with design. Assuming a contractor will be installing the upgrades, I encourage you to directly purchase the major components and supply them to the contractor for installation. This provides value in two ways. First, it eliminates the mark-up on materials (usually about 10%) that the contractor charges, which can be significant on devices that can cost tens of thousands of dollars. Second, this gives the engineer a chance to confirm the design is correct for the specific manufacturer and model purchased. For example, isolation valves have limitations on location relative to the vessel they are protecting that vary by size and manufacturer. If the contractor wants to buy a valve made by a different manufacturer than was used for the basis of design, it may not work properly if the design is not modified to compensate for the difference in requirements.
Another chance to reduce costs, and something I encourage all my clients to do for any project, is to have a constructability review meeting with the engineer and contractor. This is a great opportunity to review the design, walk the site, ask questions, discuss options, and make sure everyone is on the same page. Contractors usually have hands-on experience and look at installation differently than engineers. Their insights can be valuable and help to save time and money, IF they do not negatively impact the design. The installation requirements of explosion protection devices are not widely known and understood, so the opportunity to review and discuss proposed changes to the design is especially important for combustible dust safety related projects.
Finally, be sure to include adequate construction administration time in the engineer’s scope. Once the design is complete, it is tempting to avoid spending more money on engineering. However, it costs far less to have the engineer ensure field issues are resolved while still maintaining the design intent and satisfying NFPA requirements than ending up with a non-compliant or unsafe installation.
Summary
The common thread that unites everything above is making sure things are done correctly the first time. Begin with a solid plan to address all hazards in a prioritized order. Break work into phases as much as possible to spread out costs. Think about combustible dust safety early in the project and design accordingly. Seek guidance from professionals who have the right kind of experience. And work with your engineer and contractor as a team to achieve an efficient, and compliant, installation. Correcting improper installations after completing construction is usually very expensive and can often be avoided by following these suggestions. It may cost a little more money early in the project to ensure things are done correctly, but that cost is insignificant compared to an improper installation that fails to protect your personnel from a combustible dust event.
If you have questions or would like more information about NFPA 652 and Combustible Dust Safety, you can contact Chris directly via email at cgiusto@Hallam-ICS.com.
About the Author
Chris Giusto is Regional Manager for the South Atlantic and Director of Combustible Dust Safety at Hallam-ICS. He works with clients to improve processes & safety, reduce waste & energy consumption, increase flexibility & capacity, and build new facilities. He has over 20 years of engineering experience and leads Hallam’s Combustible Dust Safety Service offerings. He’s spent nearly his entire career working with combustible dust hazards and designing NFPA-compliant equipment and systems. With additional expertise in material handling and dust collection system design, he and his team bring a comprehensive approach to practical solutions for improving safety and meeting NFPA requirements.
Read My Hallam Story
About Hallam-ICS
Hallam-ICS is an engineering and automation company that designs MEP systems for facilities and plants, engineers control and automation solutions, and ensures safety and regulatory compliance through arc flash studies, commissioning, and validation. Our offices are located in Massachusetts, Connecticut, New York, Vermont and North Carolina and our projects take us world-wide.
You May Also Like
These Related Stories
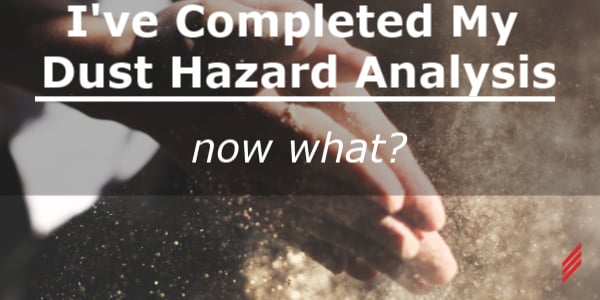
I’ve Completed My DHA–Now What?
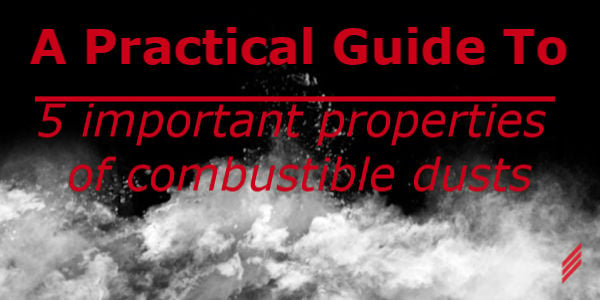
A Practical Guide to 5 Important Properties of Combustible Dusts
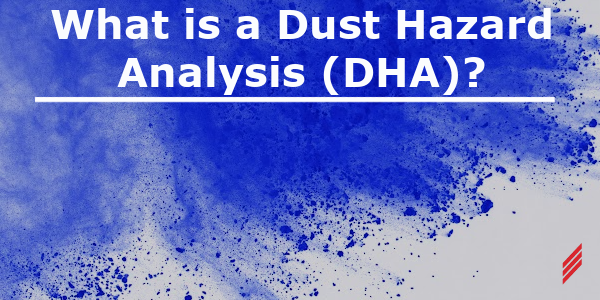
No Comments Yet
Let us know what you think