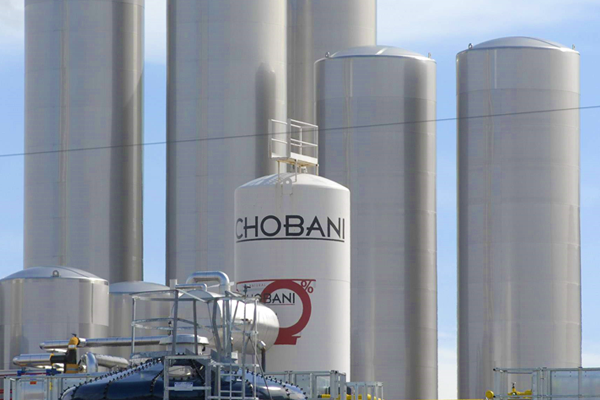
Automated Recipe Interface
Providing automation to improve quality and increased throughput.
Challenge
A rapid rise in popularity has required Chobani to aggressively grow and retool their manufacturing facility in upstate New York. Hallam-ICS has been involved with several automation projects aimed at improved quality and increased throughput.
Solution
Conveying System Upgrade: Chobani was installing a new conveying system as the first phase of an overall upgrade of their Chill Tunnel process. During this phase, the existing control system needed to be converted over to operate the new conveying system without impacting production. Managing this cut over required detailed planning, coordination with other trades and well tested PLC programs prior to conversions. The existing system consisted of (3) Allen-Bradley CompactLogix PLC’s and (8) PanelView Plus operator stations, along with numerous sensors and drives used to control the flow of product. Hallam-ICS worked closely with the electrical and mechanical subcontractors to have the new system ready and in place prior to converting to complete the upgrade successfully with no downtime.
Chill Tunnel Control System Upgrade: The next phase of the project was to upgrade the existing control system to a new ControlLogix PLC with (3) new PanelViews along with new VFD’s on Ethernet and new sensors distributed across (3) DeviceNet networks . The new control system would be programmed to provide improved utilization and flexibility of the conveying and cooling system. Algorithms were developed and new code was written for a “Traffic Cop” that would allow production to accommodate regular preventive maintenance or to continue to operate in the event of an equipment failure on one of the two conveying lines. The system also provided load balancing and uniform spacing between the pallets with an end result of more consistent cooling across the product and reducing overall energy usage.
Process & Filling Room HVAC Upgrade: The process and filling room required an HVAC system designed and programmed to maintain the required temperature and humidity conditions as well as creating positive pressure in the clean filling space to prevent potential contaminants from entering the space. Hallam-ICS installed a new Allen-Bradley ControlLogix PLC with remote I/O to operate the temperature and humidification controls of the air handling system as well as controlling pressure in the space by modulating the inlet, outlet and exhaust dampers. An emergency exhaust system was also provided in the event of any leaks in the ammonia system. The HVAC system was connected to the site Wonderware InTouch system, providing real-time monitoring and alarming as well as historical trending of key parameters.
Results
Our team accomplished the following:
- Seamless System Integration: Successfully upgraded the Chill Tunnel and conveying systems, transitioning to advanced ControlLogix PLCs and achieving improved utilization, flexibility, and energy efficiency without production downtime.
- Enhanced Cleanroom Controls: Designed and implemented a robust HVAC system for process and filling rooms, maintaining critical temperature, humidity, and pressure levels, while integrating real-time monitoring and emergency response capabilities.
- Energy Optimization and Reliability: Developed advanced control algorithms, including load balancing and fault tolerance, ensuring consistent product cooling, reduced energy usage, and improved operational efficiency.