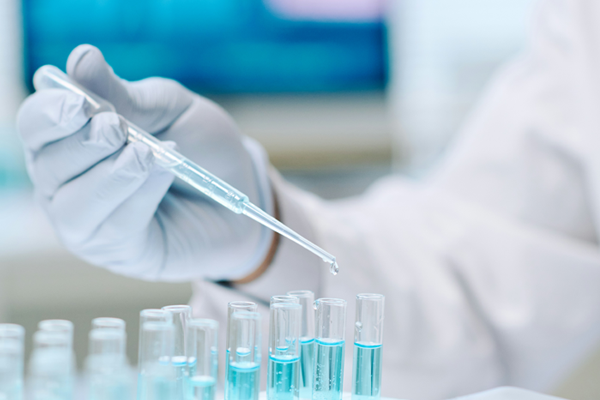
EMS Monitoring for Pharmaceutical manufacturing facility - Confidential Client
Enhanced reliability, optimized efficiency, and seamless integration for improved system performance.
Challenge
The client, a pharmaceutical manufacturer with a focus on biological products, sought to integrate a robust environmental monitoring system into their facility. The client required full redundancy, seamless data acquisition, and validation to meet regulatory compliance for their critical environments, including clean rooms and laboratory suites.
Project Challenges
- Complex Software Integration – The client had acquired a broad suite of Rockwell software and needed a structured implementation strategy to maximize efficiency.
- Validation and Compliance – The pharmaceutical manufacturing process required extensive validation of process variables, necessitating a methodical approach to verifying all data points.
- Project Schedule – To meet project deadlines, a modular and dynamic validation strategy was required, ensuring efficiency in deployment and compliance.
System Overview
- Particle Measuring Systems: The system required twenty (20) sets of Particle Measuring Systems, ISO-ProE, and MiniCapt samplers. Some required independent 24 VDC power, while others required POE ++, a high-wattage Power Over Ethernet rating.
- Each of the units used Modbus TCP/IP protocol to exchange data for status and processing parameters.
- The Process Automation Controller (PAC) was a Rockwell Automation-based system configured for redundancy with a redundant Input/Output (IO) network.
- The Human Machine Interface (HMI) was a redundant FactoryTalk View SE system, serving as the primary interface for user interaction.
- Virtualized Environment: All software was installed with a customer-provided Virtual Infrastructure environment that hosted all application servers.
- Network Architecture - The system utilized Parallel Redundancy Protocol (PRP) to ensure seamless communication and eliminate single points of failure. PRP allows redundant networks to operate simultaneously, providing continuous data availability and improving overall system reliability.
- Objective: The goal of this project was to create site hardware, software, and programming standards that allowed for rapid and dynamic deployment to aid in the validation process.
Equipment Overview
- Particle Measuring Systems:
- ISO-ProE Sampler: Compact, VHP-resistant, remote particle counter.
- MiniCapt Sampler: VHP-resistant, Annex 1 compliant, self-contained, remote microbial air sampler.
- Rockwell Automation: FTView SE, Network Distributed (PlantPAx 5.0), FT Historian, FT Asset Centre, PAC EP Processors for multiple areas, Flex5000 IO Systems, and Stratix Network switches.
- Real Time Automation: Model 460ETCMC Modbus TCP/IP Protocol Converter including 2 isolated network ports.
- SmartSights: Win911 alarm notification software used to alert operation staff of out-of-tolerance conditions via text and email notifications.
Solution
System Integration and Configuration
Our team was brought in to fully configure and commission the new Rockwell-based environmental monitoring system, which included:
- Implementing FactoryTalk View SE with primary and secondary backup servers.
- Deploying a fault-tolerant FactoryTalk Historian to log critical environmental and process data.
- Setting up redundant PLCs to ensure system reliability across multiple process areas.
- Establishing seamless integration with the Building Automation System (BAS)
- Interfacing Particle Measuring Systems and MiniCapt samplers with the Rockwell PACs for total non-viable particle count monitoring and viable microbial air sampling.
- Setting up automated alarming and notifications
System Functionality
The system was designed to ensure accurate data collection and traceability for pharmaceutical manufacturing. Key functionalities include:
- Real-Time Monitoring: Continuous environmental data collection from particle counters and microbial air samplers.
- Automated Alarming: Immediate alerts for out-of-specification conditions via Win911, enabling swift response.
- Batch Traceability: All system data as well as sample discs processed by the laboratory are associated with the batch record for end-to-end traceability.
- Data Integration: Seamless data logging into the historian for retrospective analysis and regulatory compliance.
Validation and Calibration
To accelerate the client’s production timeline, we pre-validated all I/O points prior to the installation of instrumentation. This involved:
- Conducting loop checks using calibrated meters to verify engineering units and scaling.
- Ensuring data integrity from field devices to HMI interfaces and historian logs, maintaining accuracy throughout the data chain.
- Assisting in executing validation documents using KNEAT, the client's electronic validation system.
- Documenting traceable, repeatable processes to align with GMP and FDA compliance requirements.
Outcome and Client Benefits
- Regulatory Compliance – The facility achieved traceable, validated calibration processes, ensuring adherence to stringent pharmaceutical guidelines.
- The federal regulations that are applicable are 21 CFR 210, 211, and part 11. Particle monitoring supports contamination control in aseptic environments.
- Automated data logging and audit trails ensure data integrity and traceability.
- Access controls and authority checks prevent unauthorized data modifications.
- Alerts and reports facilitate timely investigations into potential contamination events.
- Integration with electronic records and signatures supports compliance with Part 11.
- The federal regulations that are applicable are 21 CFR 210, 211, and part 11. Particle monitoring supports contamination control in aseptic environments.
- Accelerated Deployment – By pre-validating all I/O and system architecture, the client was able to expedite commissioning and reduce downtime.
- Seamless Integration – The Rockwell-based system effectively provided redundancy and a historian-driven data acquisition approach.
- Improved Process Monitoring – The particle counter and environmental monitoring system provided comprehensive visibility into manufacturing conditions.
- Long-Term Support – As a result of our involvement, the client retained us for ongoing system support and future expansion efforts.
Lessons Learned and Future Considerations
- Project Coordination is Key – Early integration of control system planning with procurement can prevent inefficiencies and unnecessary costs.
- Validation Should Be Built into the Execution Plan – Pre-validation strategies proved essential in accelerating commissioning timelines.
Results
Our team accomplished the following:
- Enhanced System Reliability – Successfully improved system performance, ensuring consistent and accurate functionality for critical operations.
- Optimized Process Efficiency – Streamlined system workflows, reducing operational bottlenecks and increasing overall productivity.
- Seamless Integration – Designed and implemented a solution that seamlessly integrated with existing infrastructure, minimizing downtime and disruption.