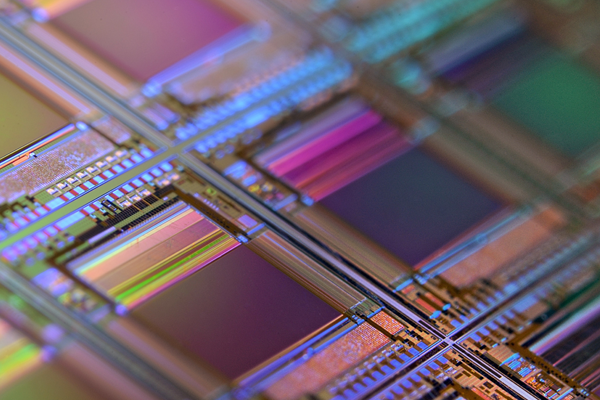
Fabrication Facility
Implementing a secure, uniform site-wide system for enhanced safety and emergency response.
Challenge
Upgrading cleanroom and infrastructure systems in an operational fabrication facility required careful phasing to minimize disruptions to production. The project scope included testing, characterization, and phased upgrades to production areas, as well as designing new cleanroom spaces, utility systems, and waste management solutions. Integrating advanced tools, such as a generator/UPS and pure water system upgrades, presented further complexity while maintaining continuous operations.
Solution
Hallam-ICS developed a phased construction plan to minimize production downtime, collaborating with a construction manager and specialized engineers for constructability reviews and pricing. Key solutions included:
- EBL tool installation: We hired an architect and a structural engineering firm to supplement our process, electrical, and HVAC team to remove an existing cleanroom, demolish utility systems, and prepare the space for new equipment. Work included installing ductwork overhead to facilitate a future phases work. The new cleanroom is an ISO 5 space, with a dedicated gowning area. Hallam-ICS’s construction group executed this project.
- Generator/UPS: We designed a containerized, outdoor lithium-ion uninterruptable power supply and standby power generator for the new tools in the current and future phases. Work included procurement of the UPS, switchgear, and generator. We hired a civil engineer and underground locating firm to establish the existing buried utilities and for the future layout.
- Metals Module: In this scope of the work, our design includes new cleanroom spaces to house new owner-procured tools for wet chemistry and etch processes. Part of this work includes a new pure water system upgrade including a temporary outdoor, containerized pure water plant to allow us time and space to renovate the existing pure water room. The new system will increase their capacity from 100 gal/min of pure water to 200 gal/min. This phase also includes a replacement of their corrosive waste system (we are retaining one of the existing in-ground tanks while replacing the other components one-at-a-time), and a new arsenic waste treatment system.
- Solvent study and design: We evaluated the existing solvent collection piping and pumping systems, in terms of future increased wafer starts. We designed replacement solvent collection piping, a new pumping station, changes to an existing station, and a new outdoor tank.
- Corrosive waste system improvement: We identified capacity and control issues with the existing corrosive waste (acid waste) system. We provided a design for increased pump capacity, added controls, and replaced piping.
Results
Our team accomplished the following:
- Delivered phased construction and cleanroom upgrades with minimal production impact, including new ISO 5 cleanrooms.
- Designed advanced utility and waste systems, doubling pure water capacity and improving waste handling efficiency.
- Successfully integrated future-ready systems, ensuring scalability and operational continuity.