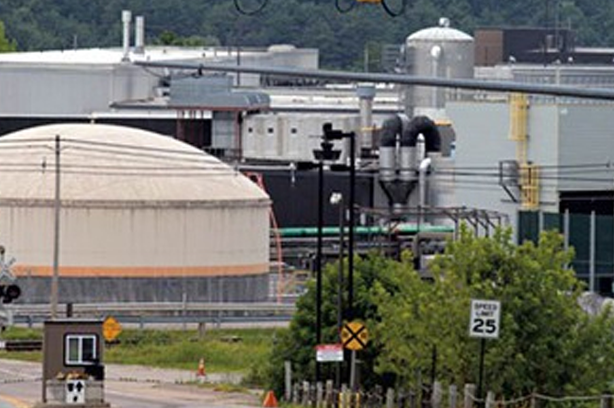
CUP Control System Upgrade
IBM (now GlobalFoundries) needed a partner who could lead the process of converting the existing control system hardware and software to the new site standards without impacting ongoing operations on the site.
Challenge
GLOBALFOUNDRIES (GF), a leading semiconductor manufacturing foundry, acquired IBM’s Microelectronics Business, including the manufacturing facility in Essex Junction, VT in 2015. This facility had operated since 1957 and had produced world-class chips for IBM, and most recently for a range of gaming and cell phone manufacturers in their 200 mm fab.
In 2012, IBM needed to upgrade the aging control system in their Central Utility Plant (CUP). The CUP is critical to the manufacturing process and provides utilities such as UPW (Ultra-Pure Deionized Water), HTHW (High Temperature Hot Water), CHW (Chilled Water) and GCHW (Glycol Chilled Water) to the rest of the site.
IBM needed a partner who could lead the process of converting the existing control system hardware and software to the new site standards without impacting ongoing operations on the site. As a long and trusted partner, Hallam-ICS was chosen for this program.
Solution
The CUP systems were controlled by a Moore hardware product line that had been phased out since being purchased by Siemens in 2000. The hardware is now discontinued. Hallam-ICS was hired to upgrade the entire control system while keeping the CUP running. During the 4-year program, the systems have been upgraded without a single interruption to services provided to the manufacturing floor.
The existing Moore control system hardware has been replaced with Schneider M340 PLC hardware with the network replaced with Modbus TCP Ethernet. The SCADA system was upgraded from Moore APS to GE Fanuc iFix. The iFix system uses an OPC server to access data from the Moore system. As the control hardware was upgraded, the SCADA tags were con- verted to an Ethernet driver so the operators have uninterrupted monitoring and control of the system.
In order to accomplish the hardware upgrade, the control system was segmented into small sections and upgraded one section at a time. In some cases these sections involved central, critical points that affect the entire utility. To upgrade the control system for these central points, temporary mechanical systems were implemented in order to seamlessly install the new control system.
Several different upgrade philosophies were applied depending on the requirements of each specific control system section. In some areas complete new control panels were installed. In some areas existing panels were retrofitted in place with new hardware. In some places hot-standby PLC architecture was implemented so the new system would have zero downtime. Upgrade strategies were evaluated and implemented in order to reduce cost and provide an incredibly reliable end result.
Results
Our team accomplished the following:
- Seamless Control System Upgrade: Successfully upgraded the aging Moore control system hardware to Schneider M340 PLC hardware with Modbus TCP Ethernet and transitioned the SCADA system to GE Fanuc iFix, all without interrupting essential utility services to the manufacturing floor.
- Customized and Reliable Solutions: Employed tailored upgrade strategies, including retrofitting existing panels, installing new control panels, and implementing hot-standby PLC architectures, ensuring zero downtime during critical system transitions.
- Enhanced Operational Efficiency and Longevity: Delivered a robust and modernized control system, incorporating temporary mechanical systems for central utility upgrades and providing a reliable, cost-effective solution aligned with the site’s long-term operational needs.