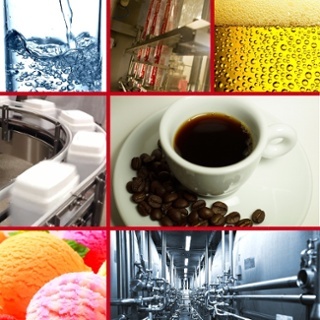
Overall Equipment Effectiveness System
System implementation for this project required installing standardized software modules to Allen-Bradley ControlLogix PLC and Panelview HMI code to generate performance data and integrate with GE Proficy Plant Applications system and documenting how these changes would impact SOPs.
Challenge
The food and beverage industry relies on innovation and efficiencies. A major Hallam-ICS client in the beverage industry had revolutionized the delivery of their product to consumers. The overwhelming success of their product and the growth of their key brands created a situation where they had to rapidly increase capacity of both their processing and packaging lines. They built new facilities and added new lines to existing facilities, all the while improving and changing production methodologies. After the installation of these systems, the production team stressed the importance of improving throughput and reducing waste by looking at the Overall Equipment Effectiveness (OEE) of their systems.
Looking for an experienced and trusted partner, they called on Hallam-ICS. The client team brought in all stakeholders; engineering, marketing & sales, production, safety and identified what was important to each of them. These requirements were shared with Hallam-ICS and these became our focus.
Solution
The engineering team and operations staff was looking for reports, key performance indicators (KPIs) and dashboards that would assist them in their efforts to reduce machine downtime. The engineering team was also looking for a standardized and well documented solution that could be rolled out across multiple sites in a timely manner. Finally, they were all looking for a system that was flexible and scalable to meet future enhancements, including connecting to SAP as part of an MES solution.
Hallam-ICS selected a team that included Senior Control System Engineers and a Business System Intelligence Developer to work with closely with the client. Regular interaction with production, engineering and business interests allowed the team to ask detailed questions before trying to define a solution. Once the existing system and future vision were fully understood, the Hallam-ICS team assisted the client with design, development and deployment of the proposed system.
A key enhancement was the ability to select manual downtime reasons as well as capturing automatic alarms. Once installed and collecting data, reports were generated using SQL Server Reporting Services. The report application was developed to be flexible, allowing the user to define the specific attributes and KPIs that they were interested in. The resulting system met all that was important to our client; it was flexible, scalable and provided the information they needed to optimize production.
Results
Our team accomplished the following:
- Enhanced Production Efficiency and Insight: Designed and deployed a flexible system that provided detailed KPIs and dashboards, enabling the client to effectively monitor and reduce machine downtime. The system also incorporated manual downtime selection and automatic alarm capture for comprehensive data analysis.
- Scalable and Standardized Solution: Delivered a well-documented and standardized solution that can be seamlessly implemented across multiple facilities. The scalable design ensures adaptability to future enhancements, including integration with SAP as part of a broader MES framework.
- Collaborative and Tailored System Development: Partnered closely with engineering, production, and business stakeholders to design a solution aligned with their unique requirements. The resulting system, leveraging SQL Server Reporting Services, empowered users to define custom attributes and KPIs, optimizing throughput and minimizing waste.