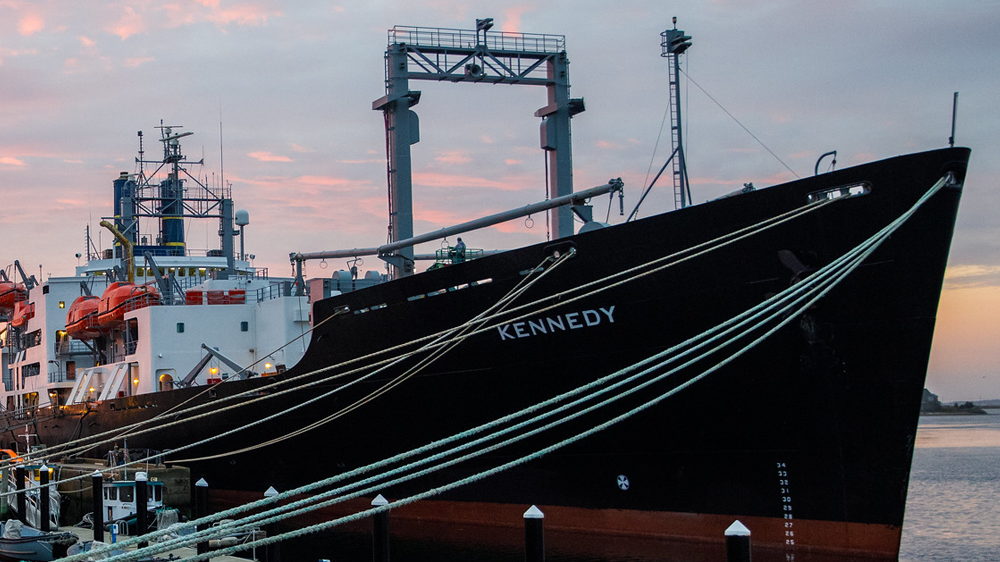
Infrared Thermography Inspection
The goal of the inspection was to record potential issues that may be present throughout the electrical system.
Challenge
Massachusetts Maritime Academy had asked Hallam-ICS to perform an electrical power system Arc Flash study, Qualified Electrical Safety Training on 10 sites as well as Infrared Thermography on two of those sites, namely Clean Harbors Athletic Center (74,000 sq. ft) and Harrington Hall (80,000 sq. ft).
MMA’s personnel safety was one of the top objectives for this inspection. The goal of the inspection was to record potential issues that may be present throughout the electrical system. Hallam-ICS Electrical Safety Team performed an infrared thermography inspection that included electrical equipment up to 4160 V such as switchgear, MCCs, panels, breakers, disconnect switches, control panels, and transformers.
Solution
Infrared (IR) thermography has been used extensively in the practice of electrical distribution systems as a key tool in preventive maintenance programs. When electrical components are nearing their failure point, they almost always produce excess heat energy. This heat energy is not visible to the naked eye, therefore using a thermal imaging camera to safely view these components and their connections is very useful in identifying problem areas before they fail completely.
Upon completing the inspection, we produced a report outlining the status of electrical systems, specifying any anomalies, or exceptions, that have been found during inspection or after analysis. Exceptions were evaluated and given a repair priority along with recommended course of action. The imaging and analysis process compared the apparent temperature differences of electrical components to similar components or ambient air. These temperature differences were used to identify problem areas, the potential cause of the problem, and rate the severity.
By combining both arc flash and the IR inspection we were able to perform work at lower cost to MMA, saving this client money on the project by removing the equipment covers once and getting their facility in compliance with OSHA and NFPA 70E/70B. The team of trained engineers who performed the inspection were based in one of our regional offices, local to the client’s site, reducing the travel costs as well.
Results
Our team accomplished the following:
- Enhanced Safety and Compliance: Completed Arc Flash study and infrared inspections to identify potential electrical system issues, ensuring compliance with OSHA and NFPA 70E/70B standards.
- Cost-Effective Preventive Maintenance: Combined arc flash and IR thermography inspections to detect equipment anomalies early, reducing repair costs and potential system failures.
- Comprehensive Reporting and Analysis: Provided a detailed report on electrical system conditions, prioritizing repair needs with actionable recommendations to improve reliability and operational safety.