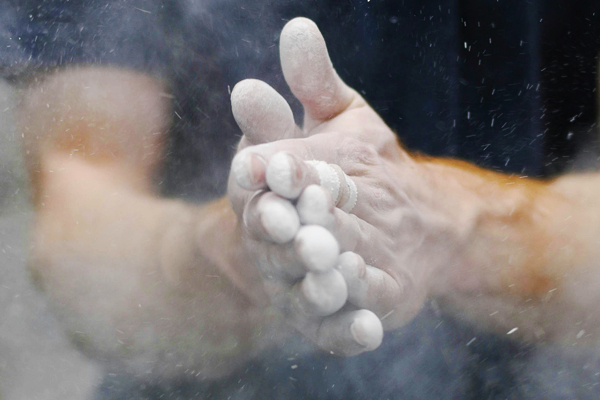
Talc Ore Processing
Implementing a secure, uniform site-wide system for enhanced safety and emergency response.
Challenge
The client required the design and construction of a new $20 million building to house a technologically advanced process for talc beneficiation, including integrating pneumatic conveyance systems, extensive electrical infrastructure, and specialized equipment. The project also involved connecting the new structure to the existing facilities and addressing complex permitting and code requirements, such as fire safety variances and utility upgrades.
Solution
Beginning with multiple collaboration meetings with client's process engineers, we went through electrical power, control system architecture, general arrangement, flow diagrams, materials and methods for pneumatic conveyance and process ductwork.
Along with the new building, our work included an elevated walkway to the existing mill building, new conveyances from existing roller mills and an addition to the existing shipping center for a bag and railcar loading system.
In addition to our team’s mechanical and electrical engineers, we hired a local civil engineer, a structural engineer and an architectural consultant to create the building’s structure and envelope.
Working from their process flow diagrams, we laid out pneumatic conveyance piping (4” through 8”), process ductwork (up to 40” diameter) and the owner-procured equipment.
We designed the balance of plant system schematics and layouts for process cooling, process water heating, compressed air, chemical distribution and injection and dust collection. During the project’s design, we were essentially an extension of the owner’s process and design engineers.
The plant’s significant electrical demand (5.0 MVA transformer nameplate) required a new electrical service from the local utility. We worked with the utility and a specialty consultant to show the overhead service from over a mile away. The electrical design influenced the layout to keep the large motors (900 HP) and heaters (300 kW) near the electrical room to save on cable costs. The electrical power distribution respected the owner’s safety requirements and practices.
Hallam-ICS was the main contact with the code officials during the design, to obtain a permit and negotiate for variances. In addition to appearing at public meetings, we met with the fire chief to review the plan for the fire pump and storage (we constructed the building foundation with a 45,000 gallon tank cast directly into the concrete) and resolve fire alarm deficiencies in the existing building.
We also negotiated for a variance to omit duct smoke detectors in certain air handlers, creating a technical basis which evaluated different technologies, the nature of the owner’s product dust and the relative risk to staff or visitors. Hallam-ICS designed and built the control panels for the project, combining our design standards with the owner’s preferences.
Results
Our team accomplished the following:
- Designed pneumatic conveyance and process ductwork systems to accommodate equipment with diameters ranging from 4" to 40".
- Secured variances for fire safety systems, such as omitting duct smoke detectors, with technical evaluations and public meetings.
- Oversaw the design of a new 5.0 MVA electrical service, optimizing equipment placement to minimize cable costs and maximize efficiency.