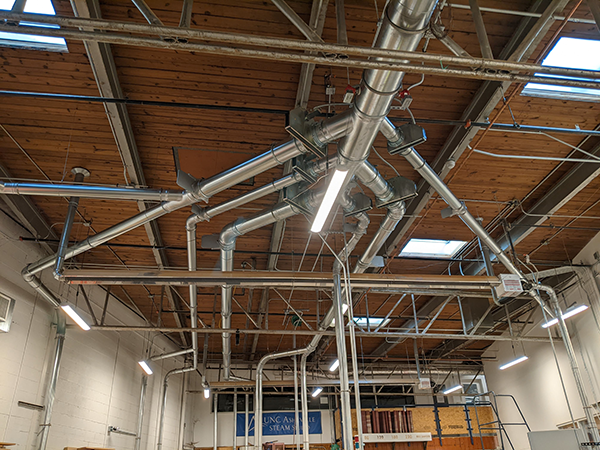
Woodshop Dust Hazard Analysis, Mitigation Design, and Dust Collection Remediation
We approach our work from a Whole Facility Design Perspective, resulting in elegant, efficient engineering solutions that are practical and reliable, maximizing your long term benefit from your facility.
Challenge
Hallam-ICS was contracted to conduct a Dust Hazard Analysis (DHA) for the ~50,000 sqft UNCA Steam Studio woodshop which included a dust collection system serving 15 pieces of equipment.
Hallam-ICS identified several hazards that required additional mitigation to achieve compliance with NFPA standards. One of the more significant issues was that the dust collector with a capacity of 3,500 cfm was not capable of serving all 15 pieces of equipment at the same time. Blast gates were installed to close off branches that were not in use, but the duct system was not designed to ensure adequate conveying velocities and resulted in dust accumulation inside the ducts.
Solution
Hallam-ICS was then contracted to engineer the necessary upgrades. Installing a larger dust collector, or a second dust collector, to achieve the needed capacity was not feasible for financial and logistical reasons.
Working closely with woodshop staff to understand the frequency of use of each piece of equipment, Hallam-ICS developed a solution for the undersized dust collection system. Equipment was grouped into six zones, any three of which could be operated simultaneously. This required a complete redesign of the ductwork system per ACGIH guidelines and specifying an automation system to maintain minimum transport velocities per NFPA requirements. Hallam-ICS also designed, programmed, built, and commissioned the control system. Other mitigation designs included proper explosion venting, spark detection and suppression, and duct isolation for clean air returned to facility.
Results
Our team accomplished the following:
- Designed an innovative ductwork system and control automation to overcome capacity limitations, enabling safe and effective dust collection across six operational zones.
- Implemented critical safety measures, including explosion venting, spark detection, suppression systems, and duct isolation, ensuring compliance with NFPA standards.
- Delivered a cost-effective solution by redesigning the system to work within existing limitations, avoiding expensive upgrades while meeting safety and performance requirements.