Design Considerations for a Helium Recovery Plant
by Ash Kreider on Feb 29, 2024 10:30:00 AM
Hallam-ICS has provided design services for several helium liquefaction plants. This blog provides details from an example project at the Massachusetts Institute of Technology (MIT). Hallam-ICS’s scope included process, HVAC, compressed air, process cooling water, electrical, fire alarm, and gas monitoring design. We worked directly for the architect on this project, LAB / Life. Science. Architecture, Inc..
You might be asking yourself what a helium liquefaction plant is, or why we need them. A liquefaction plant recovers waste gaseous helium, purifies it and reliquefies it for re-use.
What is Helium Used For?
Under atmospheric conditions helium boils at 4.2 Kelvin (-452.1 Fahrenheit). This low boiling point makes helium an excellent fluid to cool equipment and experiments that require very low temperatures. MIT uses helium for research purposes, but it is also used elsewhere to cool MRI machines in hospitals, as an inert gas for welding, and many other applications.
Typically research equipment flows liquid helium across the part of the equipment that requires cooling. The helium boils and the equipment releases the gaseous helium.
Why Recover Helium?
Helium is found in natural gas deposits. It exists in finite amounts, and once released to the atmosphere, it eventually escapes to space. There is currently a global helium shortage. If we keep releasing it to the atmosphere, we will eventually run out.
If you don’t care about depleting one of the earth’s precious resources (you should care), liquid helium is expensive, and the costs will likely continue to rise as we deplete the existing reserves.
Facilities that use liquid helium have two choices about what to do with their helium gas “waste”.
Release the helium gas into the atmosphere
- This is the easiest solution. Regulatory codes do not consider helium to be hazardous, so it can be vented directly to the atmosphere. It does pose an asphyxiation risk if it replaces air in the breathing space, so engineers have to think about where this is released.
- This solution has low upfront cost, but requires buying new liquid helium.
- This solution contributes to the global helium shortage.
Recover the helium gas, reliquefy it, and reuse it
- This solution requires a collection piping system and a helium recovery plant. These can be expensive and take time to build. They also require staff to operate the system.
- For facilities with a lot of liquid helium usage, this is often the cheapest long term solution.
- This solution minimizes the effect on the global helium shortage.
Process Equipment and Scope
For most helium recovery plants, an equipment vendor provides the equipment to a building owner, and the building owner works with an engineering firm to provide a design for the process piping. That was true with this project. Linde-Kryotechnik provided the helium recovery equipment, LAB / Life. Science. Architecture, Inc. provided architectural design and Hallam-ICS provided the process piping design. A local contractor installed the equipment, piping, and appurtenances.
Major parts of the project’s process scope and equipment included:
Equipment layout
- The project’s architect worked with MIT, Hallam-ICS, and Linde to provide a layout that functioned for the equipment and MIT’s operation team. The equipment was placed in an existing building so the architect had to work around the conditions of the existing building.
Atmospheric helium bag
- This is a large bag used to contain used gaseous helium at atmospheric pressure. For this project the bag was approximately 18’x5’x10’ with a total volume of 1,000 cubic feet.
- These bags need to be large because helium expands 745 times when it boils and warms to ambient temperatures. The 1,000 cubic foot bag for this project contains enough gas for about 5 liters (1.34 gallons) of liquid helium.
- These bags are often difficult to locate due to their size. This was no exception. In this case, the architect provided a space above an existing stairwell and Linde provided a custom bag to match that space’s dimensions.
High pressure pure gaseous helium storage tanks
- This project included 6 exterior storage tanks that were each approximately 100 cubic feet in volume. These will store helium at pressures up to 2,000 psig.
- Hallam-ICS’s design configured these tanks so that they could be used for pure or impure gaseous helium.
- This project also included using an existing exterior tank to store helium at pressures up to 150 psig. This is useful for this site because one large user discharges pressurized gaseous helium to this tank.
Helium compressors
- One Bauer 70B helium recovery compressor provided by Linde compresses the impure helium from atmospheric helium bag for use in the helium purifiers.
- Two Linde RS compressors work with the helium liquefier as part of the liquefication process.
Helium purifiers
- This project included two Linde 500A helium purifiers based on the flow rate requirement for the system.
- The helium returned from users often contains impurities, usually nitrogen, oxygen and moisture from the air. These purifiers take high pressure gaseous impure helium and provide purified helium.
Helium liquefier
- The Linde L1610 helium liquefier takes purified gaseous helium and outputs liquid helium. This liquefier is capable of producing up to 70 liters per hour of liquid helium.
Liquid helium dewar
- This project included a Cryofab CMSH-3000 liquid helium dewar. This 3,000 L container stored liquified helium for future distribution to smaller dewars.
- MIT’s team can fill smaller dewars from this tank for transport back to the equipment that needs the liquid helium for cooling.
Liquid nitrogen equipment
- The helium purifiers and liquefier require liquid nitrogen for their operation.
- MIT has an existing 1,000 gallon liquid helium tank. This project added new liquid nitrogen piping and equipment to supply the purifiers and liquefier with liquid nitrogen. This included vacuum jacketed piping, a phase separator, vacuum pump, and vent heaters.
Process piping, valves and other appurtenances
- This project had hundreds of feet of helium piping, dozens of valves, and several other appurtenances in addition to the equipment listed above.
- Hallam-ICS worked with Linde to understand the equipment and with MIT to understand how the operations team wanted to run the equipment. We provided a piping design to meet the requirements.
- The process piping for this project was complicated due to several factors.
-
- The equipment within the building had to work with tanks outside of the building. Some of these tanks were set up to switch between purified and impure helium gas.
- The interconnecting piping between the liquefaction plant equipment has specific requirements that we had to account for.
- The equipment had several cold gaseous and liquid nitrogen waste streams that we had to heat up and route to a safe location.
In addition to the process design, Hallam-ICS provided the following scope items.
HVAC
- The HVAC design included a new energy recovery unit, ductwork, new fan coil units, a new reheat coil, and controls for the system.
- The project also included a dedicated outdoor air duct and fan to cool the new Bauer 70B helium recovery compressor.
Compressed air
- This project provided new compressed air piping to the four pieces of helium recovery equipment that required compressed air.
Process cooling water
- This project included a new process cooling water loop to provide cooling water to the RS helium compressors.
- The loop included duplex pumps, an expansion tank, an air separator and other typical cooling water appurtenances.
- This new cooling water loop used one of MIT’s existing heat exchangers that was connected to the house chilled water supply.
Electrical
- Hallam-ICS provided the design for the electrical power distribution for new equipment associated with this project.
Fire alarm
- This project included design for the modifications to the fire alarm that the new building layout required.
Gas monitoring
- This project included design for an oxygen concentration monitoring system for the space. The Oxigraph model we selected pulls ambient air from four locations within the building and alarms if it detects a low oxygen concentration.
Unique Project Challenges
This project had a few unique challenges.
Helium compressor air cooling
- The Bauer 70B compressor is an air cooled unit. It is normally placed outside where it can pull air directly from the atmosphere. There was no space available outside to place this unit. Our HVAC design included additional ductwork and an exhaust fan to supply outside air to this compressor. The fan was controlled by the building management system. The building management system and the helium recovery system had to communicate to make this strategy work.
Liquid nitrogen discharge from helium purifiers
- The helium purifiers each discharge 70 liters of waste nitrogen during their regeneration cycle. To remove this nitrogen safely, the design included an electric nitrogen vaporizer to boil the nitrogen and heat it to room temperature before discharging from the building.
Heating cold nitrogen gas with vent heater
- Several pieces of equipment discharge cold gaseous nitrogen at temperatures slightly above nitrogen’s boiling point of 77.4 Kelvin (-320.4 Fahrenheit).
- This presents an asphyxiation risk. We coordinated a safe location away from people to vent this nitrogen to mitigate the asphyxiation risk.
- There is also a risk of ice forming on the end of the pipe which would cause upstream problems and in a worst case scenario, an explosion. The process design included a resistance electric heater and controls to warm the gas to room temperature prior to discharging.
About the Author
Ash Kreider is a Mechanical Engineer at Hallam-ICS. He has process engineering experience in multiple industries. He currently designs systems for a wide range of applications including gas distribution, cryogenic fluid recovery, process equipment hookup and HVAC.
Read My Hallam Story
About Hallam-ICS
Hallam-ICS is an engineering and automation company that designs MEP systems for facilities and plants, engineers control and automation solutions, and ensures safety and regulatory compliance through arc flash studies, commissioning, and validation. Our offices are located in Massachusetts, Connecticut, New York, Vermont and North Carolina Texas, Florida and our projects take us world-wide.
You May Also Like
These Related Stories
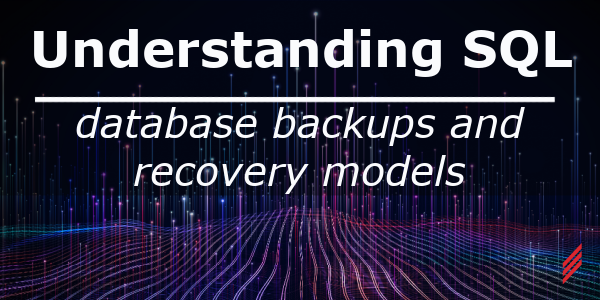
Understanding SQL Server Database Backups and Recovery Models
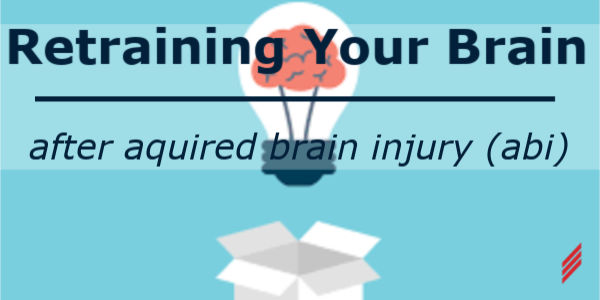
Retraining Your Brain After Acquired Brain Injury
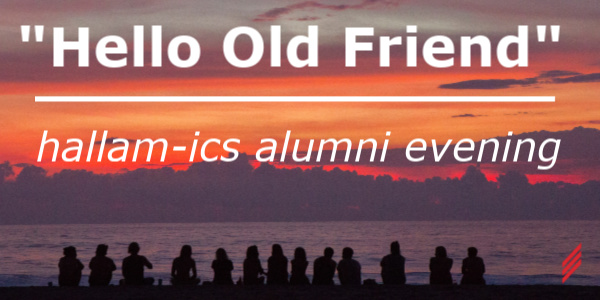
No Comments Yet
Let us know what you think