Ensure Data Integrity in cGMP: The Crucial Role of Validation Processes
by Jon Edgar on Aug 1, 2024 10:30:00 AM
In the pharmaceutical manufacturing industry, ensuring data integrity is a fundamental requirement. Within the framework of current good manufacturing practices (cGMP), maintaining accurate, reliable, and consistent data is pivotal for product quality and patient safety. The role of validation processes in upholding data integrity cannot be overstated. Here’s why.
Data Integrity in cGMP
Data integrity involves maintaining data that is complete, consistent, and accurate throughout the lifecycle of the product that the data supports and for the retention period after that. In the context of cGMP, this encompasses all data from the manufacturing process and from research and development through distribution. The data may include everything from laboratory records, equipment calibration, equipment maintenance logs, quality control, batch records, and more.
Regarding integrity, the acronym 'ALCOA' is often used as a mnemonic to remember what individual items lend to data integrity. The individual letters stand for Attributable, Legible, Contemporaneous, Original, and Accurate. In addition, 'ALCOA+' guidance recommends that data is also Complete, Consistent, Enduring, and Available.
Attributable means that the data must be, without question, the product of the person signing the work. Entries may be associated by date/time.
Legible is self-explanatory. All data recorded must be free of ink blots, smears, scribbles, and other errant marks. Data printed on thermal printer paper should be photocopied and attached to the retained documentation.
Contemporaneous means that the document is completed as close as practicable to the time of execution. Actions should not be documented after prolonged periods which could allow the operator’s memory of the event to fade and lose accuracy. Modifications to the original data must be dated, and timed and an explanation of the modification must be provided.
Original means that the original manufacturing data must be included as an attachment to the master record. If original data is recorded on scrap paper for example, the data can be transcribed into the master record, but the original scrap paper must also be attached and properly labeled with the master document number, date and time, initials of the person making the attachment and the page/step number where the data applies.
Data must be accurate as represented in the process step. Inaccurate data results in a lack of confidence in the master record and may lead to product recall and other corrective actions being taken.
The Importance of Validation in Data Integrity
One of the key outcomes of validation is to ensure that systems, processes, and methodologies generate reliable and accurate data compliant with current good manufacturing practices (cGMP) demonstrating that the system is suitable for the intended purpose, installed and operating according to user requirements. Through the validation process, potential issues that could compromise data quality can be identified and addressed.
Challenges in Data Validation
One challenge to maintaining data integrity is found in the rapid technological advancements. As systems become more complex, ensuring the validation of these systems becomes increasingly intricate. The data may be collected at the local skid level, transferred to a supervisory control and data acquisition (SCADA), stored in a database, and then recalled for display to a monitor or paper-generated reports. The integration of various software and hardware components adds layers of complexity. Each component of this interaction must be verified to maintain data accurately.
Another component of the challenge of maintaining data integrity is the potential of data being intentionally or unintentionally altered. Great effort must be made to secure data using controls that prevent unauthorized. Preventive measures should minimally include physical system access, control of users through issuance and maintenance of user credentials, user training, prevention of data access and alteration, and demonstrated evidence of changes to configured system settings which include initial setting, final setting, user who made the change and time/date of the change.
Cybersecurity must also be a consideration. Ensuring data security internally is of primary concern as disgruntled users must be prevented from adversely affecting data. Validation efforts should demonstrate robust security measures to protect sensitive information.
Best Practices in Data Integrity Assurance
Implementing best practices is crucial for maintaining data integrity. These should include:
- A risk-based approach should be taken to prioritize validation efforts. Risk assessments should be used to focus on critical areas to ensure comprehensive data validation.
- Conduct routine audits and reviews of systems, processes, policies, and procedures to identify and rectify deficiencies or non-compliance.
- Regular training for personnel on data integrity, and cGMP practices and thorough documentation of validation processes are essential.
Regulatory Compliance
Regulatory bodies, such as the FDA (Food and Drug Administration), provide and enforce guidelines to ensure data integrity in cGMP. Compliance with these regulations is mandatory and requires industry manufacturers to adhere to the regulatory guidelines.
Conclusion
Data integrity within cGMP regulated industry is not just a goal but a necessity for the efficacy and safety of the products provided to consumers. Validation processes serve as a safeguard, ensuring that data remains accurate, reliable, and consistent. By implementing best practices, and adhering to regulatory guidelines, manufacturers can uphold the integrity of their data, thereby ensuring the quality and safety of their products.
In conclusion, the critical role of validation processes in maintaining data integrity within cGMP regulated industry cannot be underestimated. It is the foundation on which trust in pharmaceutical products and manufacturing processes is based.
About the Author
Jon Edgar is the Commissioning and Qualification Team Lead for the Apex, NC office. He provides qualification and compliance consulting services to the Life Science Industry. Jon currently guides customers through the process of qualifying facilities and equipment used in pharmaceutical manufacturing.
Read My Hallam Story
About Hallam-ICS
Hallam-ICS is an engineering and automation company that designs MEP systems for facilities and plants, engineers control and automation solutions, and ensures safety and regulatory compliance through arc flash studies, commissioning, and validation. Our offices are located in Massachusetts, Connecticut, New York, Vermont and North Carolina Texas, Florida and our projects take us world-wide.
You May Also Like
These Related Stories
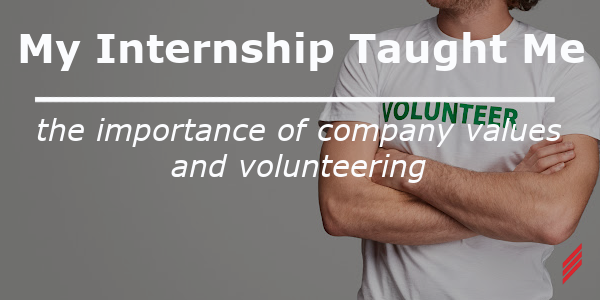
My Internship Taught Me the Importance of Company Values and Volunteering
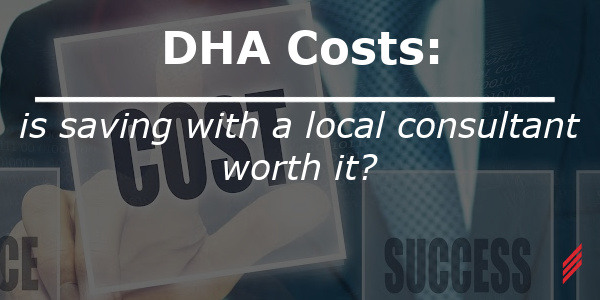
DHA Costs: Is Saving with a Local Consultant Worth It?
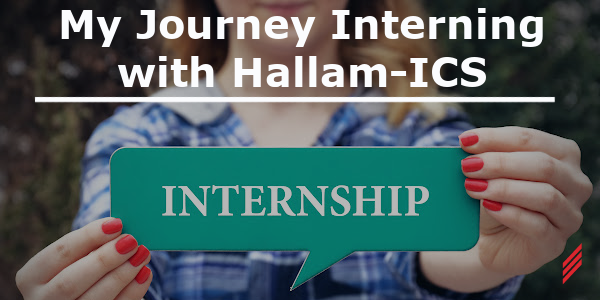
No Comments Yet
Let us know what you think