How to Implement a Combustible Dust Safety Program: Using the Combustible Dust Safety Cycle
by Chris Giusto on Mar 13, 2025 10:20:00 AM
Protecting your facility against the hazards of combustible dust is an important endeavor. But how do you know if you are taking the right steps in the right order to efficiently maximize your efforts? To help guide owners and operators through this process, I like to use a tool I developed called the Combustible Dust Safety Cycle.
The way I’ve conceptualized this, the cycle has 3 stages that revolve around a central stage that is connected to the outer three. The cycle starts with a Dust Hazard Analysis (DHA), that leads to Mitigation, and then Management of Change will bring us back to the DHA where we started. As you can see in the image above, this cycle revolves around Housekeeping, which is linked to every stage of the cycle.
With this general concept in mind, let’s look at each of these stages in greater detail.
Dust Hazard Analysis (DHA):
If you are not familiar with what a Dust Hazard Analysis is, you may want to read What Is a Dust Hazard Analysis (DHA)? to get some background before proceeding.
The DHA is where the whole cycle begins. It is where existing hazards and mitigation methods are identified and where additional mitigation methods are recommended. The first time this is completed for a facility is the most important and usually the most involved. Once a DHA is complete, an owner/operator should have a good understanding of the combustible dust hazards that are present in their facility.
If you would like to download a sample DHA Report, or view a free webinar that reviews a sample report, just click the links in this text.
Mitigation:
With combustible dust hazards, we look to eliminate the hazards when possible and reduce the severity when we cannot. The DHA report will typically recommend additional mitigation measures. These can take many forms, including but not limited to:
- Explosion protection devices
- Equipment upgrades
- New procedures
- Training
A good report will provide guidance on which mitigation options should be considered and provide pros and cons if multiple options might work to address the same hazard. The facility can then implement the recommendations. Sometimes solutions are relatively straightforward and can be executed by working with a knowledgeable explosion protection equipment supplier. Other times, solutions may be more complicated, and it is helpful to work with an Engineer that has experience with combustible dust hazard mitigation.
Management of Change (MOC):
Management of Change is the process that ensures mitigation strategies remain effective over time. Changes to processes, materials, personnel, etc. can make existing mitigation methods less effective and can also introduce new hazards that require mitigation.
The DHA report serves as the baseline for MOC. Many larger, more mature companies have formal MOC procedures that plant personnel must follow when making improvements or other changes to their facility. If your company has an existing program, be sure to include a review of combustible dust hazards as part of the process. If your company does not have a formal process, then it is important that your EH&S Manager, Project Engineers, Plant Manager, or someone in a position of responsibility is familiar with the DHA report and ensures that it is reviewed prior to implementing planned changes.
As you go through this process, you need to ask yourself questions like:
- What happens when something changes?
- Will any existing hazards be eliminated or reduced?
- Will any new hazards be created or introduced?
- Will the changes make existing mitigation measures ineffective?
These are just examples of the considerations that need to be evaluated to ensure that your Combustible Dust Safety strategies remain effective. The MOC procedure should refer to the original DHA, which you will remember is where our cycle started.
We’ve now completed our trip around the outside of the cycle and talked about the first three strategies. Let’s now look at how this all revolves around the fourth stage, housekeeping, and why housekeeping is central to the whole cycle.
Housekeeping:
Housekeeping is of critical importance to reduce the risk of a combustible dust event. While dust laying on the floor or accumulating on less visible elevated surfaces may seem innocuous, it can easily be disturbed and generate a combustible atmosphere. Fugitive dust accumulations have been responsible for some of the most devastating combustible dust incidents recorded. Often a relatively small explosion creates a pressure wave which disturbs layers of dust throughout a facility providing more fuel and creating a chain reaction of explosions and/or flash fires.
It is always better to CONTAIN, CONTROL, and ELIMINATE dust at the source before it requires clean-up. Housekeeping should be considered a secondary line of defense, but that does not mean it is any less important.
Housekeeping is integral to all aspects of Combustible Dust Safety, and the effectiveness and procedures must be reviewed and considered at every stage of the cycle:
Dust Hazard Analysis:
- Looks at existing housekeeping procedures and effectiveness
- Makes recommendations for improvements or additions
Mitigation:
- Housekeeping is a key element in any mitigation strategy
- Good housekeeping reduces the risk of secondary deflagrations
Management of Change:
- MOC should include a review of housekeeping implications
- Housekeeping should be documented, noting accumulation levels, especially in areas that are not cleaned frequently (e.g., elevated surfaces) Changes in accumulation levels are an indication that something else has changed and should probably be investigated.
Summary:
Combustible Dust Safety, done correctly, is an ongoing process. Conceptualizing the process as a cycle is helpful to determine where you are today, and where you need to go next. Management of Change must include a review of the DHA, revisions/updates should be made to the report, and mitigation strategies updated as necessary. And remember, NFPA 660 7.1.4 requires DHAs to be reviewed and updated at least every 5 years. If all else fails, this 5-year review requirement should restart the cycle.
About the Author
Chris Giusto is Regional Manager for the South Atlantic and Director of Combustible Dust Safety at Hallam-ICS. He works with clients to improve processes & safety, reduce waste & energy consumption, increase flexibility & capacity, and build new facilities. He has over 20 years of engineering experience and leads Hallam’s Combustible Dust Safety Service offerings. He’s spent nearly his entire career working with combustible dust hazards and designing NFPA-compliant equipment and systems. With additional expertise in material handling and dust collection system design, he and his team bring a comprehensive approach to practical solutions for improving safety and meeting NFPA requirements.
Read My Hallam Story
About Hallam-ICS
Hallam-ICS is an engineering and automation company that designs MEP systems for facilities and plants, engineers control and automation solutions, and ensures safety and regulatory compliance through arc flash studies, commissioning, and validation. Our offices are located in Massachusetts, Connecticut, New York, Vermont and North Carolina, Texas and Florida and our projects take us world-wide.
You May Also Like
These Related Stories
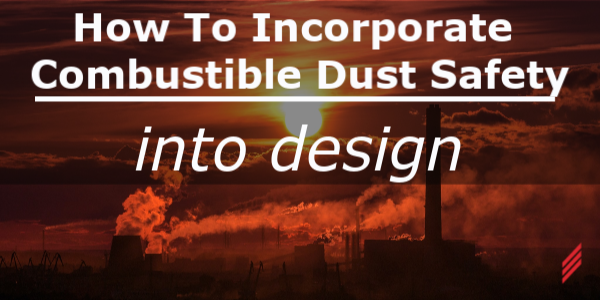
How to Incorporate a Combustible Dust Safety into Design
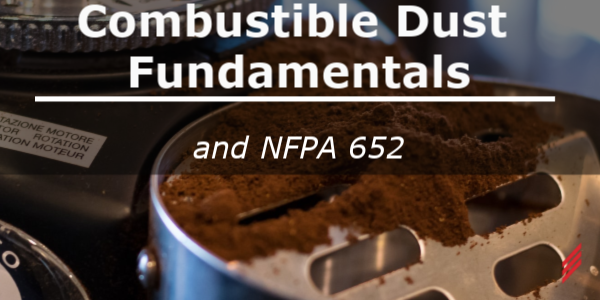
Combustible Dust Fundamentals & NFPA 652
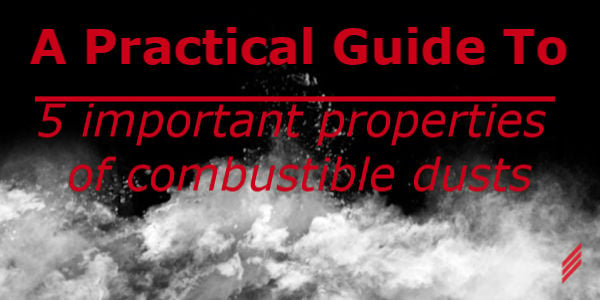
No Comments Yet
Let us know what you think