How to Incorporate a Combustible Dust Safety into Design
by Ash Kreider on May 7, 2020 10:30:00 AM
Introduction
So, you’re starting to design a new facility or process. There are a lot of things to consider, not the least of which is combustible dust safety. You may be asking yourself when the best time is to start thinking about combustible dust safety.
The answer is not surprising: immediately and throughout the design process. The good news is that if you start early, you can minimize the additional effort and cost.
Treat Combustible Dust Safety Like any Other Design Success Criteria
In any new design there are numerous success criteria that the team should be thinking about. These can differ substantially based on the type of facility or process, but some common ones include:
- Construction schedule
- Throughput
- Product quality metrics
- Safety
- Operating costs
- Capital costs
A good design team will consider all the criteria above and many more as they go through the design process. The best way to handle dust safety is to treat it the same way as any of these other success criteria. The team needs to consider all success criteria to develop the best design. There are many project management and six sigma books that discuss how to do this effectively, so I won’t go into detail in this blog.
My point here is simple: Dust safety is an important success criterion. Treat it as you would any other important success criteria.
Can I Just Wait Until Everything Is Built to Think About Combustible Dust Safety?
You could ignore combustible dust risk in the short term, but this will likely cause you more pain in the end. In many cases a small design change, such as locating equipment near an exterior wall, can save you from major design changes later in the process when it is more expensive. This should not be a surprise to any design professional. As with any major success criteria, the earlier you can define what is needed and incorporate it into design, the better.
If you are fortunate enough to be working with a dust that is not combustible you will still need to document the dust properties for NFPA 652 compliance. This can be done at any point, but it is prudent to do this early in case the dust turns out to be combustible.
Items to Consider
1. Do You Have a Combustible Dust Expert?
You should ensure that you have someone on your team that is familiar with performing dust hazard analyses, and who understands the hazards associated with combustible dust. Depending on your process, you may want to have someone on your team that understands dust collection systems, deflagration venting or explosion prevention systems.
2. Is Your Dust Combustible?
Look through publicly available literature for your dust. If nothing exists, send out a sample for a “Go/No-Go” screening test. If you’re lucky enough to have a dust that is not combustible, your design will be much simpler. Be sure to maintain documentation of the results.
3. What are Your Dust’s Properties?
There are 5 important combustible dust properties to consider. My colleague Chris Giusto discussed these in a previous blog. You should determine which properties will be important to your design and test for them if publicly available data does not exist. Don’t forget to consider dust at any point in the process. Operations that change the makeup or particle size of the dust may have a large impact on dust properties.
4. Housekeeping
It seems strange to think about things like how to clean the rafters during the design phase of a project, but it can become important if dust is able to escape the process. Secondary explosions from accumulated dust are often worse that the initial explosion. If dust will be outside of your process, think about how it might be dispersed and how to clean it up.
5. HVAC Design
If a return air duct is located near a dust generation source, there is potential for dust accumulation within the ductwork. This is another potential source for a secondary or tertiary explosion.
6. Dust Collection
If you will be collecting dust from your process, be sure the dust collection system is designed for your dust. If your layout allows, placing this equipment outside the building is often a way to isolate this equipment from the rest of the plant.
Don’t forget that dust collection equipment, cyclones for example, can segregate your dust by particle size, which will change the dust’s properties.
7. Electrical Classification
If dust will be generated in combustible quantities one option is to electrically classify the space. While this adds cost, it can sometimes be the most effective way to mitigate a combustible dust risk.
8. Know the Relevant Codes and Standards
NFPA 652, the Standard on the Fundamentals of Combustible Dust is a great starting point for combustible dust safety, but you should also be familiar with NFPA 654, the Standard for the Prevention of Fire and Dust Explosions from the Manufacturing, Processing, and Handling of Combustible Particulate Solids. There are also several industry specific NFPA standards that might apply to your process, examples include coal (NFPA 120), combustible metals (NFPA 484), and wood processing (NFPA 664).
Should I Perform a Dust Hazard Analysis as Part of the Design Effort?
A dust hazard analysis is a great way to document the combustible dust risk for your process, you will need to perform one before startup, but it may be premature to perform a full DHA during the early design phases. It also may not be possible because many of the key players that will operate the process may not be available.
I suggest pre-populating your dust hazard analysis document as early as you can in the design process. Identify items that will be critical to design and focus on these. As the design solidifies, revisit and update the document. If you do this correctly, when the team performs the dust hazard analysis, it will go smoothly.
Summary
Combustible dust safety is an important success criterion for a new process and should be treated as such. Be sure your design team has the proper knowledge and experience relative to your process.
If you would like to learn more or want to discuss your process, you can contact Ash directly at akreider@Hallam-ICS.com.
About the Author
Ash Kreider is a Mechanical Engineer at Hallam-ICS. He has process engineering experience in multiple industries. He currently designs systems for a wide range of applications including gas distribution, cryogenic fluid recovery, process equipment hookup and HVAC.
Read My Hallam Story
About Hallam-ICS
Hallam-ICS is an engineering and automation company that designs MEP systems for facilities and plants, engineers control and automation solutions, and ensures safety and regulatory compliance through arc flash studies, commissioning, and validation. Our offices are located in Massachusetts, Connecticut, New York, Vermont and North Carolina and our projects take us world-wide.
You May Also Like
These Related Stories
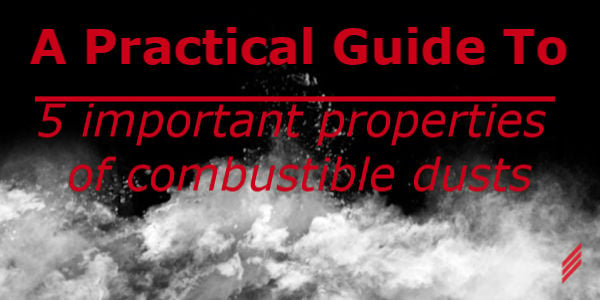
A Practical Guide to 5 Important Properties of Combustible Dusts
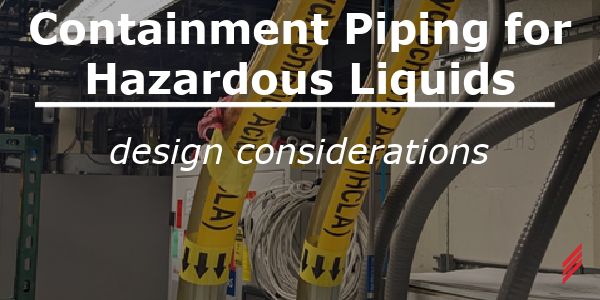
Containment Piping for Hazardous Liquids - Design Considerations
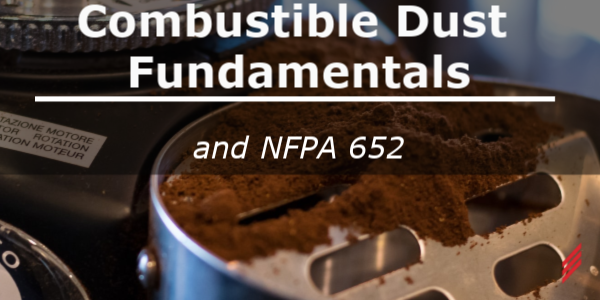
No Comments Yet
Let us know what you think