Containment Piping for Hazardous Liquids - Design Considerations
by Ash Kreider on Dec 7, 2023 10:30:00 AM
Piping design for hazardous liquids often includes double walled piping. This piping system consists of a carrier pipe and a larger concentric containment pipe. The carrier pipe carries the process liquid under normal operating conditions. In the event of a carrier pipe failure, the containment pipe contains the liquid.
This blog explains when to employ a containment pipe strategy, what types of products are available, and important design considerations for liquids. For information on gaseous piping, refer to my article on Containment Piping for Gases.
Why Use Containment Piping?
Code Requirement
The most obvious reason to add containment pipe is if it is required by code. In general, the requirements are the same through the United States. Codes require leak detection and emergency shutoff or excess flow control for liquids with these conditions:
- Liquids that are in piping at a pressure greater than 15 pounds per square inch gauge (psig), and
- Liquids that have a NFPA 704 hazard ranking of
- Health hazard Class 3 or Class 4
- Flammability Class 4
- Instability Class 3 or Class 4
These codes do not directly require double-walled piping, but this is often the best way to meet the leak detection or excess flow control requirement.
Code Details
The governing fire code for locations within the United States is usually either:
- NFPA 1 as published by the National Fire Protection Association, or
- The International Fire Code (IFC) as published by the International Code Council.
The relevant code sections for the 2021 code revisions are below.
The wording in these two codes is rearranged somewhat, but is nearly identical, so regardless of which code is in effect, the requirements are the same. Depending on location, the effective edition may change, but recent editions have similar language. It is possible, but infrequent, that local amendments change these requirements.
Good Engineering Practice
The statutory codes cover most but not all situations. It is our job as engineers to use good judgement when designing piping systems to protect life, health, and property in situations that the code writers did not consider. There are many situations like this. A few examples of when to consider adding containment piping are:
- When the liquid is less hazardous than the code requirements, but leaks could go undetected for long periods of time.
- Where a leaked liquid could combine with nearby incompatible materials.
- When a leak could cause significant property damage.
Owner Requirements
In some instances, the owner of a facility requires containment piping even when it is not required by code. In these instances, the engineering decision is easy.
Containment Piping and Equipment
Piping/Tubing
There are many ways to provide containment piping. Here are some common examples in our practice:
- Manufactured ASTM A269/A270 double walled stainless steel tubing and fittings
- Several manufacturers including Dockweiler, Swagelok, and Valex provide off-the-shelf stainless steel tube fittings for double walled piping systems. These can be difficult to find in sizes greater than 1 ½”.
- Polypropylene double walled piping and fittings
- Several manufacturers including Asahi America, GF and Simtech USA provide off-the-shelf polypropylene double walled piping systems.
- PVC or CPVC double walled piping and fittings
- Several manufacturers including Asahi America, GF, and IPEX provide off-the-shelf PVC or CPVC double walled piping systems.
- DIY solutions
- Using an off-the-shelf system is generally the easiest solution, but it is not required for double walled piping systems. If a design requires a specific pipe system, an engineer can specify a do-it-yourself solution for the contractor to install. This can get complicated fast. Some things to consider include:
- How will you join the containment pipe after installing the carrier pipe?
- How will you support the carrier pipe within the containment pipe?
- What size containment pipe can be used for which carrier pipe size? Remember to include fitting dimensions.
- Will the contractor understand the system you have in mind? You will likely need to provide several details with any complicated joints.
- PFA carrier pipe contained within a PVC or CPVC containment pipe is a common solution for process chemicals in semiconductor fabs.
- Using an off-the-shelf system is generally the easiest solution, but it is not required for double walled piping systems. If a design requires a specific pipe system, an engineer can specify a do-it-yourself solution for the contractor to install. This can get complicated fast. Some things to consider include:
PFA carrier and clear PVC containment pipe containing Hydrochloric Acid
Pumps, Valves, and other Appurtenances
In general, our designs locate pumps, valves, and other appurtenances within a pit or container designed for containment. These locations have leak detection and can serve to be the leak detection for the double walled piping that leads to and from them.
There are some double walled valves available from manufacturers such as GF. Hallam-ICS designs do not use these frequently.
Leak Detection Methods
There are several options for liquid leak detection with double walled piping systems.
- Provide Visual Inspection Locations.
- An engineer can design a piping system with visual inspection locations. These require periodic visual checks to confirm that liquid has not leaked. Some common examples include:
- Sight glasses located below the piping and connected only to the interstitial space between the pipes.
- Clear sections of containment piping. This is a common strategy with PVC containment piping because PVC is available in the traditional opaque as well as clear.
- Drain from interstitial space to a visible location.
- Visual inspection locations provide a means to detect liquid. They do not provide a means for automatic shutoff.
- An engineer can design a piping system with visual inspection locations. These require periodic visual checks to confirm that liquid has not leaked. Some common examples include:
- Perform pressure or vacuum integrity test on interstitial space.
- Testing the interstitial space simultaneously tests the carrier and containment pipe to confirm that they are both still leak free.
- This can be done on a regular cadence.
- Hallam-ICS recommends this procedure for any piping system even when the interstitial space is monitored with another method. We recently had a client find out that their carrier pipe had been installed improperly over a decade ago and leaked. A simple pressure test every few years would have found this issue.
- The design needs to include a method to connect to a pressure or vacuum testing apparatus. Usually this is simple and inexpensive.
- Automated leak detection using level switches.
- This is traditionally done with a level switch within the interstitial space or in a location that the interstitial space drains to.
- This allows automated shutoff of pumps or valves via the controls system.
- Automated leak detection using interstitial pressure/vacuum monitoring.
- With this method, the interstitial space is either pressurized with a non-hazardous gas or evacuated. The pressure is monitored with a pressure transducer.
- The use of a pressure transducer allows for automated shutoff of pumps or valves via the controls system.
- We design this type of system frequently for gasses. It is possible to use this method for liquids, but it is not commonly used for liquids.
This pipe is connected to the interstitial space of double walled pipe. The clear pipe section allows for visual inspection and the level switch provides automated detection of a leak. This is a common setup in semiconductor facilities.
Summary
Containment piping systems can get complicated, but there are many products and best practices that engineers can use for a complete design. When used effectively, these systems can keep your piping safe and code compliant.
If you would like to learn more about containment piping or have a specific application that you would like engineering support for, contact Ash directly via email at akreider@Hallam-ICS.com.
About the Author
Ash Kreider is a Mechanical Engineer at Hallam-ICS. He has process engineering experience in multiple industries. He currently designs systems for a wide range of applications including gas distribution, cryogenic fluid recovery, process equipment hookup and HVAC.
Read My Hallam Story
About Hallam-ICS
Hallam-ICS is an engineering and automation company that designs MEP systems for facilities and plants, engineers control and automation solutions, and ensures safety and regulatory compliance through arc flash studies, commissioning, and validation. Our offices are located in Massachusetts, Connecticut, New York, Vermont and North Carolina Texas, Florida and our projects take us world-wide.
You May Also Like
These Related Stories
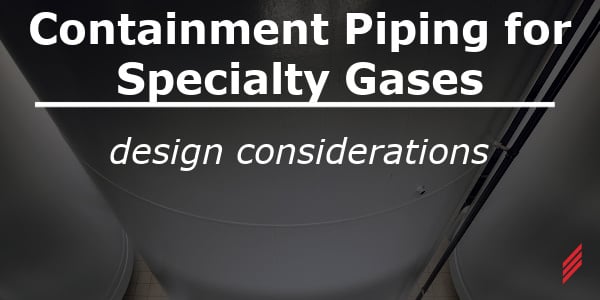
Containment Piping for Specialty Gases - Design Considerations
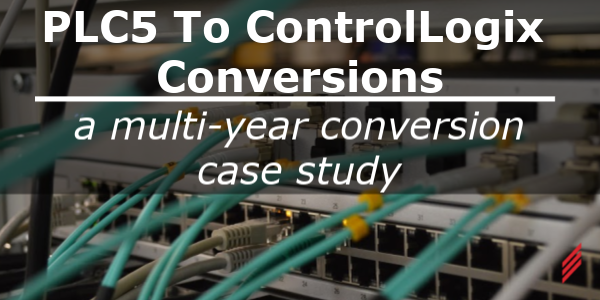
PLC5 to ControlLogix Conversions – A Multi-Year Conversion Case Study
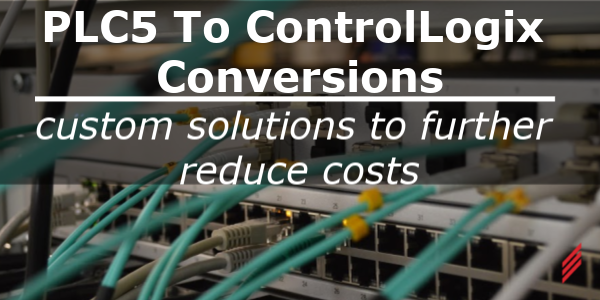
No Comments Yet
Let us know what you think