Which Underground Electrical Solution is Right for You?
by Jeff Babineaux, PE on Oct 17, 2024 10:30:00 AM
In January of 2024, the US Department of Energy announced a $34 Million dollar program to increase grid reliability across eleven states. Kudos to the DOE for a weirdly complicated name that made me laugh. They called it the Grid Overhaul with Proactive, High-speed Undergrounding for Reliability, Resilience, and Security, or GOPHURRS for short. We know that moving power underground makes our distribution more reliable, and for large commercial and industrial customers, it’s not only better aesthetically, but it makes more sense than running overhead cable trays and conduits in many applications. Options for underground distribution below the utility scale are varied, though, and each one comes with its own benefits and drawbacks. Keep reading to learn more about direct burial, metallic and non-metallic conduits, and concrete-encased duct banks to learn what questions to ask to find the best solution for your needs.
Defining Risk and Weighing Cost
What factors affect the risk to people in the installation area? Even though underground power is naturally insulated from the general public, the old ‘out of sight, out of mind’ adage is a cautionary reminder that workers in the area of underground power might damage cable through soil disturbance when digging or driving heavy equipment, and soil content might allow for prolonged exposure to moisture or freezing temperatures. Is the installation area one with high foot traffic or small vehicles? Will the area have surface cover like a parking lot, sidewalk, or other equipment slab that provides an extra layer of protection? Are the people who pass through this area part of the general public, employees only, or qualified persons only?
Defining cost can be considered from the perspective of initial cost versus cost over the life of your distribution assets. While the most economical up-front cost is generally accepted to be an overhead line, direct burial is a close second and provides reduced maintenance costs. You can incur more expenses by installing in conduit underground, or encasing conduit in concrete. Every level adds to the initial investment and reduces future maintenance costs down the road. So how do you decide how much to pay upfront?
The graphic above might be over-simplified, but gives an approximate relative cost of 200’ of 200-amp service. While less common than the rest of the categories seen here, I’m highlighting fiberglass as an alternative approximately equal to EMT for cost as installed, since it costs more per foot in material, but saves on labor in a market where labor costs are an increasing concern. If we considered the same categories for reliability, we might come up with an almost perfect duplicate. While exact reliability numbers would be difficult to even estimate for a single line of such short length, and historical overhead numbers might be conflated with utility reliability, the below scale can be used as a guide:
It’s important here to note that fiberglass offers many strength advantages similar to rigid, but better for corrosion. I think most would agree, however, that nothing beats concrete-encased PVC for durability and resistance to outside disturbances like digging, tree root growth, and heavy traffic above.
A Few Notes on Underground Solutions
Direct-burial is a great no-nonsense solution for remote areas that don’t get a lot of foot traffic, but you should still have a maintenance plan in place to monitor the integrity of the cable. Remote means you might have root growth in the area, and trees have a way of taking out even underground circuits given enough time.
Schedule 40 PVC is more common than Schedule 80. This refers to the wall thickness, so it might be more prone to cracking. PVC is non-metallic, so it resists corrosion better, and non-magnetic which unfortunately makes it harder to find after installed. If you’re specifying PVC for underground, the marking tape that is required per code for service conductors should also be considered for ease of maintenance in raceways other than service conductors. While schedule 40 is more common, schedule 80 is required where the raceway is subject to physical damage, so I typically specify this in industrial and large commercial applications. The last note I’ll make on PVC is that it expands at a much higher rate than rigid metallic or fiberglass. If you have the room to put in expansion fittings, it might be worth the cost of a few of these, but you also have to consider the effect of conductors in long runs of PVC, and make a service loop at the termination to accommodate.
Fiberglass is a great all-around raceway that has the financial and anti-corrosion advantages of PVC and the durability advantages of rigid metallic conduit. It’s lightweight and installs quickly. Barring a preference from my clients, I recommend fiberglass conduit for everything between direct burial and concrete-encased raceway.
EMT (Electrical Metallic Tubing) is not actually conduit, as evidenced in the name. As such, many jurisdictions do not allow it to be used in underground applications. While advances are being made in EMT construction and the 2023 code now allows for it to be used in direct-burial applications with fittings listed for this use, the concerns of corrosion with this thin-walled tubing are based on years of experience, and I can’t think of an advantage to using EMT above the other options listed.
Rigid metallic conduit is the workhorse of industrial applications. It’s probably on the truck if your run goes long, or if you need an extra piece because of cutting/bending mistakes. It doesn’t have the expansion issues of PVC, but is not used in concrete-encased applications partly because of the overkill factor, and partly because it can experience severe corrosion where it exits the concrete and is exposed to soil or salt or air. Rigid is also the preferred method for hazardous locations, since PVC and fiberglass would have to be encased in two inches of concrete.
Concrete-encased PVC affords a measure of reliability above and beyond the rest of the solutions discussed. While much more labor is required for a good installation, often it’s the best option for sites that have seen the damage and inconvenience of underground raceways that fail and know that they are at a higher risk.
After you’ve chosen your installation type, consider the cost of buying backfill, and understand that this will be needed when working in rocky ground, when it’s possible for chunks of pavement to get mixed in, or when the material you dig up prevents adequate compaction. Sand is cheap and helps to drain water. Gravel under sand is the best drainage solution, but you don’t want large rocks coming into contact with conductors or raceways.
With all of the possibilities, the best solution is one where clear objectives are shared between the owner, consultant, and installing contractor. The value in a specification or product has less to do with my own preference as a consultant, and more to do with where the owner finds value in the finished installation. If you have questions about underground electrical installations, feel free to reach out to us. With offices from Texas up to Vermont, we’ve seen a wide range of environmental considerations, but would love to hear your own experiences on what worked, what didn’t work, and what would have been nice to know at the beginning of a project.
About the Author
Jeff has a B.S. in Electrical Engineering from Louisiana Tech University. Prior to coming to Hallam-ICS, Jeff had 7 years of experience working in prefab construction for mechanical and electrical buildings and skids. He holds a professional engineering license in multiple states, participates in all phases of the project design from concept through construction, and cooks a mean gumbo.
Read My Hallam Story
About Hallam-ICS
Hallam-ICS is an engineering and automation company that designs MEP systems for facilities and plants, engineers control and automation solutions, and ensures safety and regulatory compliance through arc flash studies, commissioning, and validation. Our offices are located in Massachusetts, Connecticut, New York, Vermont, North Carolina and Texas and our projects take us world-wide.
You May Also Like
These Related Stories
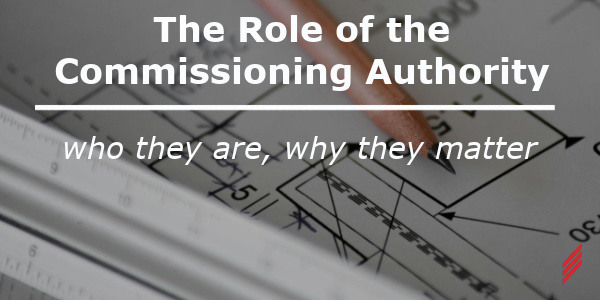
The Role of the Commissioning Authority: Who They Are, Why They Matter
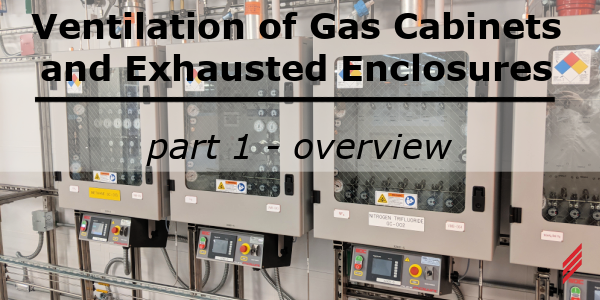
Ventilation of Gas Cabinets and Exhausted Enclosures, Part 1 Overview
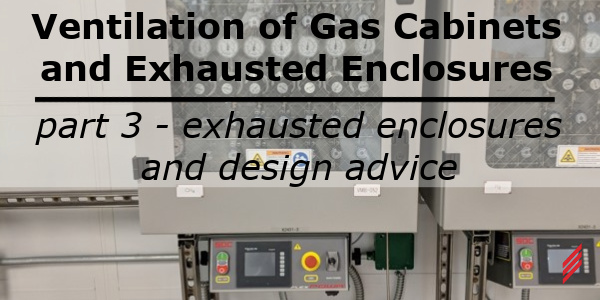
No Comments Yet
Let us know what you think