Ventilation of Gas Cabinets and Exhausted Enclosures, Part 3
by William Neuburger on Feb 11, 2021 10:30:00 AM
Gas cabinets and exhausted enclosures are found in many of our client’s facilities, primarily in semiconductor fabrication and research laboratories. The appropriate amount of airflow is not always obvious to the designer. This blog is the third in a series of three that will focus on code requirements and ventilation rates for gas cabinets and exhausted enclosures associated with compressed gases and their distribution.
Part 1: Ventilation of Gas Cabinets and Exhausted Enclosures – Part 1 Overview
Part 2: Ventilation of Gas Cabinets and Exhausted Enclosures – Part 2 Gas Cabinets
What is an Exhausted Enclosure?
- International Code Council (ICC) and National Fire Protection Association (NFPA) harmoniously define an enclosure with specificity
- Size can vary, for gas and liquid chemical distribution, they are commonly 3’ and 4’ tall, with an electronic controller on top or below, 2’ to 3’ wide and 1’ to 1’-6” deep
- Contains gas or chemical distribution control elements (pressure regulators, solenoid valves, manual valves, pressure and flow controls, safety features)
- The configuration of control elements varies by application and user requirement
- The front of the cabinet:
- Is entirely openable for access
- Has slots or adjustable louvers to allow air to flow in and around exhaust neck on top for duct connection, often 4” or 6”
- The enclosure’s purpose is to provide a physical separation of the gas or liquid controls from users, contain small liquid leaks or ventilate gas leaks
- Common example: Valve manifold box (common in semiconductor industries for gases and liquids) or a paint booth
- Odd example: Chemical fume hoods in laboratories – though described as an exhausted enclosure in both ICC and NFPA, we do not treat them as exhausted enclosures
The International Fire Code Defines Exhausted Enclosures:
An appliance or piece of equipment which consists of a top, a back and two sides providing a means of local exhaust for capturing gases, fumes, vapors and mists. Such enclosures include laboratory hoods, exhaust fume hoods and similar appliances and equipment used to retain and exhaust locally the gases, fumes, vapors and mists that could be released. Rooms or areas provided with general ventilation, in themselves, are not exhausted enclosures.
Chemical Fume Hoods
This definition hints at laboratory chemical fume hoods, which is worth discussion here. ICC ventilation requirements for exhausted enclosures are appreciably different than we use in chemical fume hood design; the IFC requires 200 feet/minute through the open face of the enclosure.
There are no statutory, prescriptive requirements for chemical fume hood ventilation; ANSI/AIHA Z9.5, Laboratory Ventilation, 2012 is an excellent reference document. This standard recommends a range of 80-100 feet/minute for ventilation. Also, ASHRAE 110 is a test procedure which the designer can consult when contemplating a chemical fume hood installation.
These different ventilation rates are not perfectly coherent in the codes, though our experience is no code official or authority having jurisdiction has ever expected chemical fume hoods to comply with the exhausted enclosure rates.
Valve Manifold Boxes
In gas distribution we frequently deploy valve manifold boxes (VMBs) to allow safe distribution and isolation of multiple gas demands. VMBs are not specifically covered in the ICC family, however the International Fire Code discusses “ventilated enclosure” in the semiconductor chapter, always next to exhausted enclosures. One can argue a VMB is not an exhausted enclosure, as it does not meet the geometric definition. At Hallam-ICS we consider VMBs as exhausted enclosures, to be conservative and offer a likely simpler permitting path with code officials (or authorities having jurisdiction).
Applications for Exhausted Enclosures:
- Valve manifold box for gas or liquid distribution and leak containment or control
- As a convenient, safe location to house control and safety elements
- Spray paint booth
- Local Exhaust Ventilation (LEV) for hazardous activities – manually weighing and transferring explosive powders
Exhausted Enclosure Ventilation Requirements
Advice for Gas Cabinets and Exhausted Enclosures Design
- Review the current, statutory code and memorialize your airflow decision in a basis of design.
- Always schedule the gas cabinet and exhausted enclosure airflows on a drawing. It is the clearest way to describe the needed ventilation particularly if you are not the HVAC engineer. For projects with multiple cabinets and enclosures in the same room, consider scheduling access port open and access port closed values to give the HVAC engineer and balancing contractor flexibility.
- Include an expected exhaust differential pressure (sometimes called static pressure) in the schedule. If you have an access port open/closed value, consider scheduling the differential pressure for both values. Differential pressure requirements vary by vendor, absent other information use -0.5” for the schedule/specification but design the ventilation system around -0.75” as margin. The static pressure is a nontrivial issue, particularly for cabinets or enclosures with high ventilation rates (silane or highly toxic materials for example). A submittal for a silane gas cabinet project on a recent project came through expecting -1.0” of differential pressure, the exhaust system design included -0.5”. We resolved it with the vendor, they added a second exhaust connection.
- When there are multiple gas cabinets in a space, think carefully about how you specify the exhaust airflows, it is difficult to configure and balance an air handling system (supply and exhaust) to meet “port open” airflows for all cabinets or enclosures concurrently.
- Often gas cabinet vendors include an exhaust airflow in either their standard product literature or submittals, the airflows will almost always be different than our scheduled value. If you did your design work correctly, confidently tell the vendor and contractor to kick rocks when they suggest your airflow is incorrect because the vendor’s design is “SEMI compliant” or “they always do it that way.” You designed the ventilation based on statutory requirements.
- Ventilation rates for gas cabinets with silane mixtures will require additional conversation with users as their intended cylinder supply affects the airflow.
*CGA G-13
The Compressed Gas Association publishes this document, “Storage and Handling of Silane and Silane Mixtures” which covers all aspects of silane system design. This blog post covers gas cabinets and exhausted enclosures and describes valve manifold boxes (VMBs). The ICC and NFPA codes more generally describe VMBs as exhausted enclosures.
Ventilation rate selection is an important part of the deployment and use of gas cabinets and exhausted enclosures. The ventilation provides a measure of safety and deserves thoughtful attention by the design team. The time between initial rate selection and testing can be years, memorialize the important elements of your design work so the owner, supplier, installer, test agency, and code official understand the design requirements.
About the Author
Bill has been a mechanical engineer since 1995 and with Hallam-ICS since 2010. His career has brought him to the top of the Transamerica Pyramid Center, chemical plants, underground mines, paper mills, and semiconductor fabrication facilities. He has experience designing, specifying and installing mechanical and electrical systems in the built environment covering industrial, institutional and commercial facilities.
Read My Hallam Story
About Hallam-ICS
Hallam-ICS is an engineering and automation company that designs MEP systems for facilities and plants, engineers control and automation solutions, and ensures safety and regulatory compliance through arc flash studies, commissioning, and validation. Our offices are located in Massachusetts, Connecticut, New York, Vermont and North Carolina and our projects take us world-wide.
You May Also Like
These Related Stories
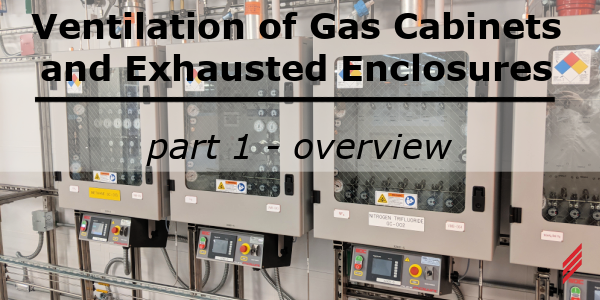
Ventilation of Gas Cabinets and Exhausted Enclosures, Part 1 Overview
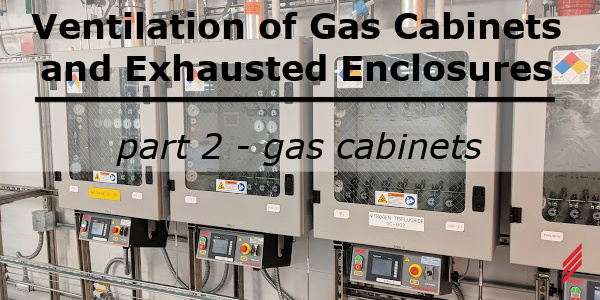
Ventilation of Gas Cabinets and Exhausted Enclosures, Part 2

Comments (4)