3 Reasons Why a Commissioning Authority Should be Executing Checklists
by Keith Sheldon on May 23, 2024 10:30:00 AM
It has been a standard practice within the commissioning process, that the Commissioning Authority (CxA) is a 3rd party working directly for the owner who then produces the pre-functional checklists for all of the project’s Mechanical, Electrical and Plumbing (MEP) equipment. The CxA then issues those checklists to the installing contractors to complete and return. Once returned, the CxA is to review the checklists for completion, as well as accuracy and then proceed the commissioning process to the next phase of commission which would be functional or operational testing. I have found although this process is routed in good practice, it is rarely executed successfully and in a timely manner.
In this blog, I’ll describe three important reasons why you as the project owner should consider having these pre-functional checklists be executed by the Commissioning Authority instead of the installing contractors.
Reason #1 Accuracy of Completion
When the commissioning authority submits these checklists to the installing contractors, they assume that they will be filled out accurately and completed fully by the contractor who installs the equipment being checked out. However, it has been my experience that these checklists rarely get completed by the installing contractors during the actual installation, without lots of prodding from the CxA to complete them. The checklists are often completed well after the installation has been completed and they are frequently handed off to an apprentice rather than the skilled installer who actually completed the installation. As such, many times they are just completed with every single answer being answered a “YES” or a “PASS”. This is due to inexperience in completing the checklist and due to the fact you’re asking someone to complete a checklist based on the accuracy of their own installation. It’s like a teacher asking a student to grade their own homework. Surprise they always get a perfect score every time, and guess what the checklist was most likely filled out on the back of their pickup truck in five minutes rather than the full hour it should have taken while standing in front of the equipment.
Reason #2 Schedule Delays
As described in Reason #1 above, the process tends to lead itself to multiple passing back and forth of paperwork. First the contractor receives the checklists, and if they are delinquent with returning them, as they almost always are, the project won’t move forward on time until they are complete. Typically, the contractor will wait till all of the equipment they are responsible for to be installed before executing the checklist for an individual piece of equipment. Sometimes this is weeks or months after it was originally installed. This delays the return of the checklists to the CxA, which in turn delays the CxA from coming to the field to verify the accuracy of the installation. And if these checklists were filled out on the back of the pickup truck, good chances are that when the CxA is able to walk everything down they are going to find something that might not be quite right with the checklist upon further review and will need that to be corrected or a clarification issued as to why the installation is different. This further delays the commissioning process from moving forward why the team waits for the resolution to be determined, pushing out the completion of the project.
Reason #3 Budget Savings
Finally, most specifications for commissioning state that the contractor will be required to support the commissioning effort and describe the process within the specification. The installing contactor bids the work and includes hours within their bid to meet this scope, the general contractor then gets that bid and marks it up and submits it to the owner. Problem with this approach, is the estimator who is bidding the project is not usually the actual installer themselves, and the estimator will then short the hours that would be required for commissioning, because they want to win the job, and they know that if they were to be accurate with their time for this Cx effort, that their bid may be considered too high now and they will not be selected for the project. That being said the CxA contract is usually held by the owner themselves, and that contract is limited to the CxA only verifying the completion of the checklists and not the extra time to resolve issues. When there is extra time required to chase down the checklists to be reviewed, or extra time is needed to correct the checklists due to incompleteness or inaccuracy is required, that extra time is then captured within a change order to the owner from the CxA, which could result in back charges to the general and installing contractors thus causing even further schedule overruns as the owner secures funds for the CxA’s extra time.
How Can This All be Avoided?
Very simply, require that the pre-functional checklists be written and executed by the CxA and take the execution of checklists away from the installing contractors within the commission specification. Installing contractors will no longer shortchange the hours required to complete the commissioning effort, the general contractor will no longer be marking up those extra hours included. The CxA fee of course will increase in this model, however this will easily be offset by the schedule delays and change orders as described previously. The extra time and fee to be paid to the CxA up front will be well worth it later on. By the CxA executing those checklists in real time, less non-conformances will be found and when they are found they will be corrected in a timelier manner usually at a lower expense than had they been found later in the project. All that time that was spent chasing down getting the checklists returned and verifying their completeness can now be used by the CxA to keep the project moving towards meeting the schedule at no extra cost to the owner. This overall result is the commissioning process for the project is now completed accurately, on time and within the allocated budget.
About the Author
Keith Sheldon is the Commissioning Manager for Hallam-ICS. Keith started his Hallam career in the Hallam-ICS Vermont office and now works out of both the Hallam-ICS Massachusetts and Connecticut offices. Keith has a Bachelor’s of Science degree in Engineering and Management from Clarkson University, and holds a certificate in project management from Worchester Polytechnic Institute. Keith is a member of the ISPE International Society of Pharmaceutical Engineers, and has performed commissioning and qualification projects in the pharmaceutical industry for over 15 years.
Read My Hallam Story
About Hallam-ICS
Hallam-ICS is an engineering and automation company that designs MEP systems for facilities and plants, engineers control and automation solutions, and ensures safety and regulatory compliance through arc flash studies, commissioning, and validation. Our offices are located in Massachusetts, Connecticut, New York, Vermont and North Carolina and our projects take us world-wide.
You May Also Like
These Related Stories
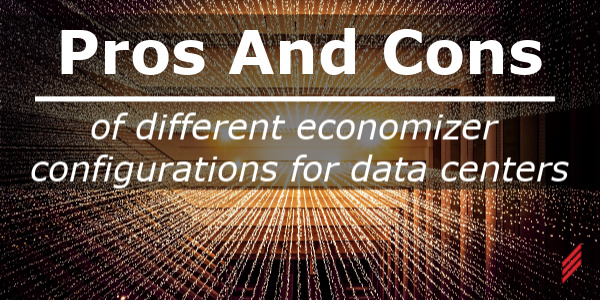
Pros and Cons of Different Economizer Configurations for Data Centers
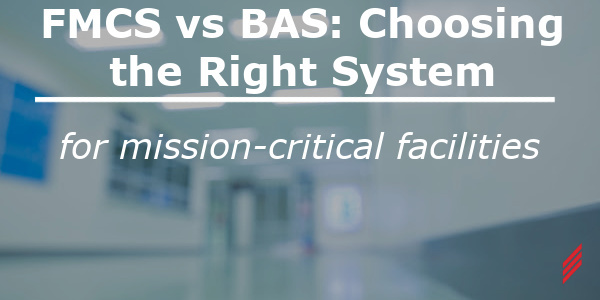
FMCS vs BAS: Choosing the Right System for Mission-Critical Facilities
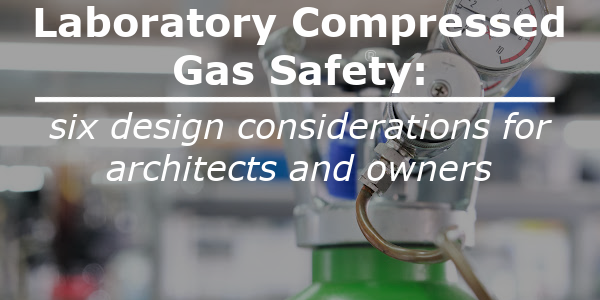
No Comments Yet
Let us know what you think