5 Benefits of Infrared Thermography
by Bryan Campbell, PE on Jan 9, 2025 10:30:00 AM
Infrared thermography is a cutting-edge technology that measures the infrared radiation emitted by an object, translating it into a visual representation of the temperature distribution of that object. This non-contact, non-destructive, and non-invasive technique is invaluable in many industries, including electrical, mechanical, and building maintenance. It plays a crucial role in inspections, diagnostics, and predictive maintenance, offering a range of benefits that go beyond simple temperature readings. In this blog, we will delve deeper into the advantages of infrared thermography and how it is transforming the way we monitor and maintain systems and infrastructure.
Early Detection of Problems
One of the standout features of infrared thermography is its ability to detect potential issues at their earliest stages. Often, equipment malfunctions or system failures begin with subtle temperature anomalies that are not visible to the naked eye. Infrared thermography detects these temperature variations with exceptional accuracy, allowing experts to identify problems before they escalate into costly or hazardous failures. For example, a small temperature rise in an electrical circuit could indicate an impending failure, and addressing it early can prevent expensive repairs, minimize downtime, and avoid safety risks. Early detection using infrared thermography can be a game-changer for maintenance teams, as it helps them fix issues before they cause significant damage or system disruptions.
Increased Equipment Lifespan
The longevity of machinery and infrastructure is a critical concern for businesses across various sectors. Regular use of infrared thermography in maintenance practices can help extend the lifespan of equipment by ensuring it operates at its optimal condition. By detecting temperature irregularities, infrared thermography identifies issues like overheating, friction, or misalignment that can lead to excessive wear and tear. For example, overheating in a motor or electrical component can cause premature aging, but infrared thermography enables technicians to address the root cause before it results in permanent damage. As a result, equipment that undergoes frequent thermographic inspection runs more efficiently and lasts longer, reducing the need for costly replacements and repairs.
Reduced Downtime
Unexpected equipment failure is one of the leading causes of downtime, which can have severe consequences for productivity and revenue. Manufacturing facilities, power plants, and other critical infrastructures are highly dependent on continuous operation, and any unplanned outages can disrupt operations for hours or even days. Infrared thermography helps to minimize this risk by detecting early warning signs of malfunction. For instance, an electrical panel or a mechanical component might be running hotter than usual, signaling an impending failure. By identifying such issues early on, maintenance teams can perform corrective actions without interrupting operations. This proactive approach drastically reduces the likelihood of unplanned downtime, ensuring that systems run smoothly and business operations continue uninterrupted.
Enhanced Safety
Safety is a paramount concern in every industry, and infrared thermography plays an essential role in ensuring the safety of personnel and equipment. The technology can quickly detect potential fire hazards, electrical faults, gas leaks, and other dangerous conditions before they result in accidents. For example, electrical circuits that are overheating or poorly insulated can pose significant fire risks, while gas leaks can endanger the health of workers and lead to explosions or environmental contamination. Using infrared thermography to detect these threats allows facility managers to address them before they escalate into life-threatening situations. Furthermore, by reducing the risk of workplace injuries and accidents, infrared thermography helps create a safer working environment, which is essential for employee morale, productivity, and compliance with safety regulations.
Improvements in Energy Efficiency
Energy efficiency is another area where infrared thermography provides significant benefits. It is an excellent tool for identifying areas of energy loss in buildings, machinery, and systems. Heat loss through walls, roofs, windows, or insulation is often invisible to the naked eye, but infrared thermography reveals these inefficiencies by detecting temperature differentials. For example, the technology can pinpoint areas where insulation is damaged or where drafts are occurring, which can lead to unnecessary heating or cooling costs. By addressing these energy loss points, building owners and facility managers can make necessary repairs or improvements that not only enhance comfort but also lower energy bills. Additionally, reducing energy consumption through better insulation, sealing leaks, or optimizing HVAC systems can contribute to sustainability goals by decreasing carbon emissions and reducing the facility's overall environmental footprint.
Conclusion
Infrared thermography is a highly effective and versatile technology that provides numerous benefits across industries. It enables early detection of issues, increases equipment lifespan, reduces downtime, improves safety, and enhances energy efficiency—all of which contribute to greater cost savings and operational efficiency. By leveraging infrared thermography, companies can stay ahead of potential problems, optimize maintenance schedules, and create safer, more energy-efficient environments. Whether used in electrical, mechanical, or building inspections, infrared thermography is an indispensable tool that ensures systems and equipment are running at their best while minimizing risk and improving productivity.
About the author
Bryan Campbell is a Professional Engineer for Hallam-ICS with a focus in electrical power. He has spent his career performing arc flash and infrared thermography studies in a variety of industries including Pharmaceutical, Industrial, Food and Beverage as well as Higher Education. His areas of expertise include SKM, AutoCAD and Revit.
Read My Hallam Story
About Hallam-ICS
Hallam-ICS is an engineering and automation company that designs MEP systems for facilities and plants, engineers control and automation solutions, and ensures safety and regulatory compliance through arc flash studies, commissioning, and validation. Our offices are located in Massachusetts, Connecticut, New York, Vermont and North Carolina, Texas and Florida and our projects take us world-wide.
You May Also Like
These Related Stories
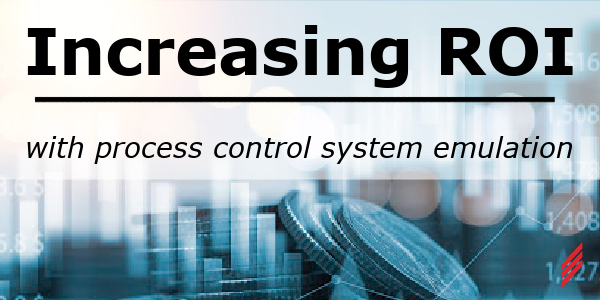
Increasing ROI with Process Control System Emulation
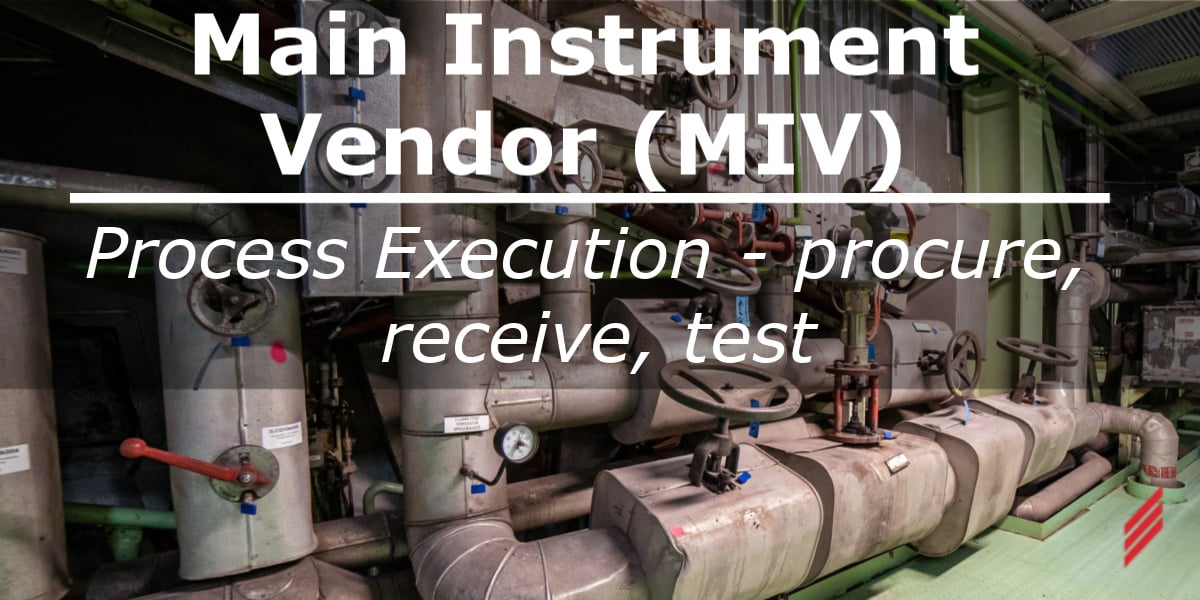
Main Instrument Vendor (MIV) Process Execution - Procure, Receive, Test
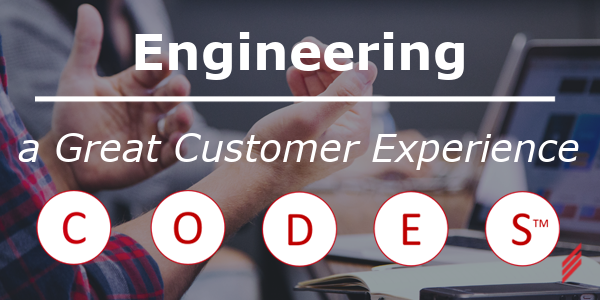
No Comments Yet
Let us know what you think