5 Examples of Good Engineering Practice Exceeding Minimum Requirements of Building Codes
by Mark Felgate on Sep 17, 2020 10:30:00 AM
As we progress in our growth as a design engineer, we have teachers along the way. Some teachers are senior design engineers that instruct and teach us what good engineering practice is all about. Some teachers are lessons learned from experiences that teach us that there may be a better way to design something.Some teachers are journals, papers, books (and even blogs) that share experiences that we can gleam some valuable lessons from. Whichever teacher (or teachers) you have, whom have been mentored themselves, you gain insight on what good engineering practice is. You also become more and more aware that codes are not design standards. Rather, codes are minimum requirements to ensure the safety and well being of occupants in a building.
Codes do not provide direction for better use of a space, efficient use of a space, or achieving a better life cycle of a building or space. As NPFA 70 (National Electrical Code) – 2017 Edition states in Paragraphs 90.1(A) and 90.1(B):
“The purpose of this Code (National Electrical Code) is the practical safeguarding of persons and property from hazards arising from the use of electricity. This Code is not intended as a design specification or an instruction manual for untrained persons.”
And,
“This Code contains provisions that are considered necessary for safety. Compliance therewith and proper maintenance result in an installation that is essentially free from hazard but not necessarily efficient, convenient, or adequate for good service or future expansion of electrical use.”
I recently reviewed conditions in a building that illustrated this point with poignancy for the building Owner. The Owner is now spending a significant amount of money repairing systems in the building that have already failed or shows signs of deterioration due to poor engineering practices or poor installation methods. The following is a short list of possible design decisions or installation methods and the possible ramifications (some of which occurred in the building that I recently reviewed):
- Use of Type M copper versus Type L copper tubing. Type M is permissible to use but has a thinner wall structure. Eventual leaks are more likely to occur with the use of Type M copper tubing.
- ABS piping may be acceptable in many applications. However, ABS does not like heat or tension; especially the combination of both. ABS piping in the building will likely fail due to the impacts of both heat and tension. Heat from electrical wires pressed up against the ABS and extremely hot water (including pouring boiling water down a drain in a kitchen), will cause rapid aging and deterioration of the ABS material.
- Always specify that the grounding electrode system be measured to ensure that the measured impedance is 25 Ohms or less. Also note that supplemental grounding electrodes are required when the water main is the only other grounding electrode. The impedance should be tested and, if the measured results are higher than 25 Ohms, additional grounding electrodes (of various methods) may need to be added to meet the 25 Ohm limit.
- Always ensure that hot and cold water piping are insulated properly. Gaps in insulation can cause dripping water and corrosion.
- Where metal piping has fittings, equipment, or sections of piping exist that do not provide a conductive path for electrical current to flow, bonding jumpers are required to ensure that the entire path of piping provides an electrically conductive path to ground. If a section of metal pipe does not have an electrically conductive path to ground, and a compromised wire or equipment short applies voltage to that pipe, someone who comes into contact with that pipe can receive an electrically shock. That electrical shock could be lethal.
Note that this list is not complete or even comprehensive. It just lists some examples of possible design decisions or construction methods that could have a long term impact on a building or compromise occupant safety. The bigger lessons that we learn are as follows:
- Just because lower cost materials and lessor grade materials are allowed by code to be used, the long term results can spell disaster for an Owner.
- The codes usually dictate the minimum requirements for fire, health and safety purposes. However, those minimum requirements may not be enough for a long-lived, energy efficient installation.
- Pay attention to what is being installed during construction to make sure Contractors are not missing important elements. Quality project execution takes quality documents and quality installation.
If you have ever asked yourself, “what difference does it make”, the answer is likely “a big difference.” Or, if you asked the question “what is the big deal?,” the answer might be “it’s a big deal.”
About the author
Mark Felgate is the Lead Electrical Engineer for the Massachusetts and Connecticut Offices for Hallam-ICS. Mark has been in the construction industry for 32 Years, has a Bachelor’s of Science Degree in Electrical Engineering from the University of Connecticut, and is a LEED Accredited Professional. Mark is a Member of NFPA and is currently serving as Past President of the Hartford Section of IES. Mark also continues to volunteer as a mentor through ACE Mentor since 2001.
Read My Hallam Story
About Hallam-ICS
Hallam-ICS is an engineering and automation company that designs MEP systems for facilities and plants, engineers control and automation solutions, and ensures safety and regulatory compliance through arc flash studies, commissioning, and validation. Our offices are located in Massachusetts, Connecticut, New York, Vermont and North Carolina and our projects take us world-wide.
You May Also Like
These Related Stories
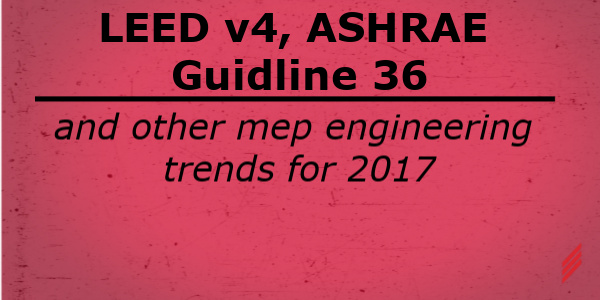
LEED v4, ASHRAE Guideline 36 and other MEP Engineering trends for 2017
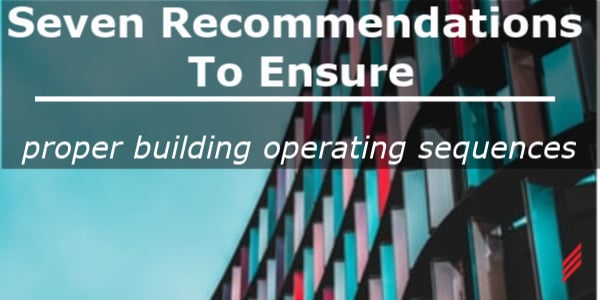
Seven Recommendations to Ensure Proper Building Operating Sequences
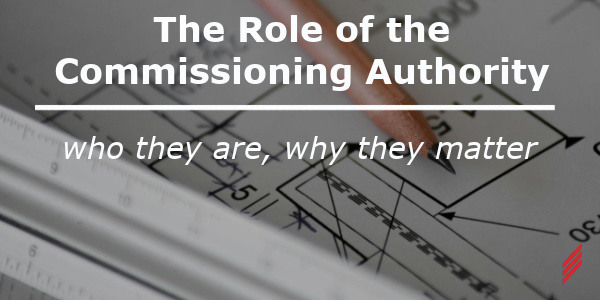
Comments (1)