Seven Recommendations to Ensure Proper Building Operating Sequences
by John Butterfield on Jul 9, 2019 10:21:00 AM
Many years ago, when I first got into building commissioning one of my mentors told me that over 70% of building operating issues stem from unclear expectations, and/or unclear communication.
Despite significant changes in equipment, codes and technology; clarity of expectations and communication remain as pertinent today as they did back then.
Here are seven recommendations for ensuring that MEP building systems, operate as they are intended to.
Overview
The purpose of the sequence of operation is to define how the system will function, throughout its various operating modes. If the sequence of operation is not defined and implemented correctly, then system performance will suffer.
The project begins with the development of the Owner’s Project Requirements (OPR). The purpose of the OPR is to define the user requirements that the building, and its integral systems, must perform to. Every phase of the project, including the MEP Engineering, from this point forward must perform to the OPR.
Project Design Phase: The sequence of operation is typically developed by the MEP engineering team as part of the system design. System design therefore consists of two parts:
How the system will be built (system architecture, component specifications, how the individual components interface with each other).
How the system is intended operate (sequence of operation).
Project Construction Phase: The controls contractor furnishes and installs the system in accordance with the design. Control system programming is determined by the sequence of operation so that the system operates as it is intended to. Controls programming includes the logic for how the system will operate, as well as operator interfaces such as graphics, alarming, trending and reporting.
Project Commissioning Phase: Working with the engineer, contractors and equipment suppliers, the commissioning agent verifies that the systems operate as intended through the functional testing process.
In a perfect world all these phases would mesh together seamlessly, and the system would operate exactly as it was intended it to. However, in reality, there are numerous places where this process can break down. When this happens, the system fails to operate as it was intended to. The result is complaints of occupant discomfort, out of spec products or environments, as well as high energy consumption. In essence, the OPR is not being met.
Recommendations
Some red flags that we look for in the commissioning process include:
1. The sequence is unclear
Situation: We’re all human, and we don’t always commit all of the details in our head into the design documents. Frequently, those “minor” details that we “leave to the controls contractor to figure out”, are critical to intended system performance. Discrepancies arise when the controls contractor misinterprets the sequence, and programs the system to operate as they understand it should; which may differ from the engineer’s intended sequence.
Solution: Hosting sequence of operation review meetings early in the project is time well spent. Walking through the operating sequences with the owner, engineer, controls contractor and commissioning provider can clarify the intended operating sequences. Often times, project team members offer recommendations and suggestions for how the operating sequences might be simplified or improved. These revisions can then be incorporated into the sequences of operation. Another added benefit is that all project team members have a clearer understanding of how the system is intended to operate.
2. The sequence is too complicated
Situation: Spurred on by technology, code requirements, and the desire for innovation and creativity, the designer may develop overly complex control sequences. Though technically elegant, these complex sequences may not function well in the real world. If complex sequences are difficult to analyze and troubleshoot, they may confuse the operations and maintenance personnel to the point where they simply give up and “do what they have to in order to keep the system running”. This often takes the form of manually overriding operating set points and sequences. These field changes are often un-documented, and lead to further confusion and deterioration of system performance down the road.
Solution: Know your audience! A key requirement is to provide a system that is understood, and maintainable by the owner’s operations and maintenance personnel. The building operators and technicians must understand what their systems are, and how they operate. It is better to have a simpler control sequence that operates properly, than a complex one that doesn’t.
3. Conflicting controls
Situation: Equipment such as commercial air handling units are often furnished with their own factory installed controls. These integral controls frequently consist of “black boxes” whose operating sequences are unclear to everyone except perhaps the factory technician. Equipment is then interfaced to the building control system, which controls the overall system per the sequence of operations. If the on-board controls are trying to control to one set of parameters, and the building control system to another; then the two systems will conflict, or “fight” each other.
Solution: The ideal solution is to commit to a single control platform. In larger, more complex buildings, equipment might be furnished without controls, so that they can be controlled by the building control system. In smaller facilities, the on-board equipment controls meet the OPR. In this case, if a building control system is installed, it should be used for monitoring, alarming, trending, and scheduling, and leave the controlling to the on-board equipment controls.
4. “We already have a program that does the same thing”
Situation: In today’s cost competitive environment, equipment manufacturers and controls contractors strive to standardize their control platforms. Most of the controls companies have standard libraries of control sequences which they apply to commonly used equipment. Standardization is fine, except when these “canned” sequences differ from what the designer intended. Then, what started out as a good idea, can turn into conflicting systems operation.
Solution: Back to the operating sequences review meeting. This is an excellent opportunity for everyone to understand the intended operating sequence, and to offer suggestions.
5. “We already know what the owner wants”
Situation: Larger building owners typically have legacy systems that are similar to the new system. The operations and maintenance personnel prefer to have the new system operate just like the last one. However, there may be valid reasons why the engineer has developed a different sequence of operations for the new systems. Current building energy codes may dictate new requirements that the legacy system was not intended to perform to.
Solution: Again, another excellent reason to host the operating sequence review meeting.
6. “My part works fine, it’s somebody else’s problem”
Situation: Systems, even those found in a typical building, can be very complex, and they are made up of multiple mechanical, electrical and control components. Malfunction or improper adjustment of any component can impair system performance. When the system malfunctions, it’s generally “somebody else’s problem”.
Solution: Define the problem first, and then form assumptions. The first step is to get the project team together, to clearly define the problem. This avoids suppositions, assumptions, “finger-pointing”; and keeps the project team focused on solving the problem.
7. "Why are these problems still not fixed?”
Situation: As the project winds down, contractor personnel move on to the next job. Meanwhile, the commissioning process is still ongoing. System issues, are still being identified, but there are few, or no qualified personnel left on site to address them. Getting engineering and contractor personnel back on site to support this effort can be lengthy and frustrating.
Solution: Recognize that the contractors’ staffing requirements will peak during construction, and the commissioning requirements will peak during startup, turnover and post occupancy. Ensure that the project requirements include time and budgets for correction of problems in a prompt and efficient manner.
In Summary:
The key is to communicate, communicate, and communicate! Lack of communication, incorrect assumptions and misunderstandings can impair the performance of even the best designed system.
About the author
John has retired from Hallam-ICS, but his contributions to the company continue to be valued.
Read My Hallam Story
About Hallam-ICS
Hallam-ICS is an engineering and automation company that designs MEP systems for facilities and plants, engineers control and automation solutions, and ensures safety and regulatory compliance through arc flash studies, commissioning, and validation. Our offices are located in Massachusetts, Connecticut, New York, Vermont and North Carolina and our projects take us world-wide.
You May Also Like
These Related Stories
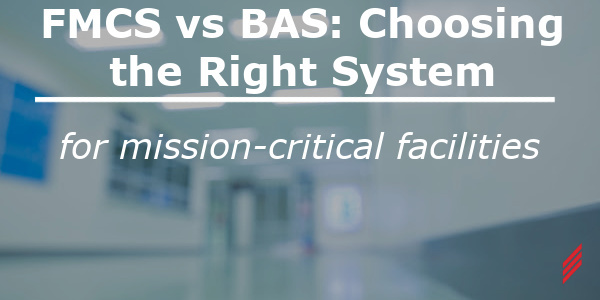
FMCS vs BAS: Choosing the Right System for Mission-Critical Facilities
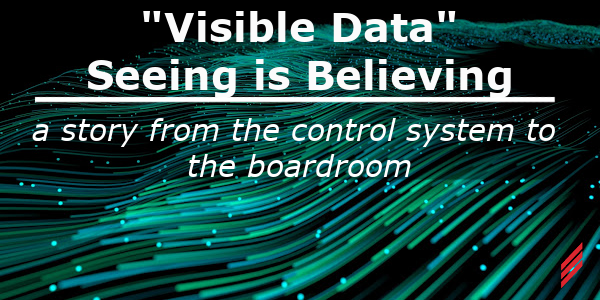
'Visible Data' – Seeing is Believing. A story from the Control System to the Board Room.
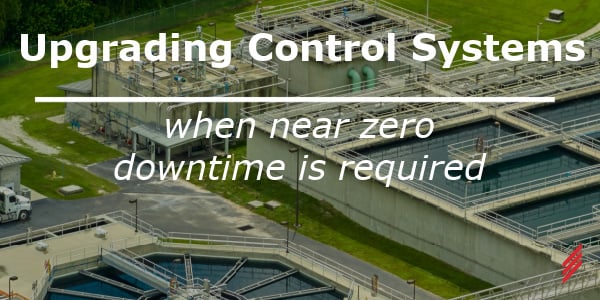
Comments (2)