8 Steps to Create an Electrical Safety Program Part 3
by Jason Mazzola on Feb 4, 2021 10:30:00 AM
Welcome back to my 5-part blog series on Electrical Safety Plans. In parts 3 & 4, we will continue on to cover Required Safe Work Practices. This section will be covered in two parts due to the amount of information required for this section.
Part 1: Purpose, Scope and Responsibilities
Part 2: Requirements and Protective Measures
Part 3: Required Safe Work Practices
Part 4: Required Safe Work Practices Continued
Required Safe Work Practices
The next component to include in your ESP is required work practices. This is the most labor-intensive section to create because you need to outline all the parameters for safe work practices coving a wide array of topics. For the most part this information can be pulled directly from the NFPA 70E document. I will now cover some of the topics that need to be included but it is important to remember that you can expand and include anything you think is relevant locally to you and your staff.
You need to clearly define what an electrical space is, and the determination needs to be made who may enter those spaces. This information should be included in the plan and is located in the 70E document. The individuals that may enter most likely will be those that are considered electrically qualified to work on or be near energized parts. In the instance that an individual needs to enter a space, all proper work procedure and PPE should be referenced here.
A section on electrical equipment should be included; this will cover the safe operation of the electrical apparatus. This should take into account all possible scenarios including those listed below:
- Damaged Electrical equipment
- Hazardous areas
- Operating Equipment
- Overcurrent Protection Tripping
- Interlocks
- Working overhead
When addressing damaged electrical equipment, you should state that the damaged equipment needs to be immediately reported to management. Some examples of typical equipment that may become damaged are MCC’s, transformers, circuit breakers, and disconnect switches. However, any other electrical equipment at your facility that is damaged needs to also be reported. The direction needs to be given to DO NOT TOUCH damaged equipment until proven safe by someone on your staff that is electrically qualified.
If you have areas in your facility that have additional hazards above the electrical hazards it is important that additional consideration is given to these areas. In the case that electrical equipment will be located in a hazardous area, all equipment must be approved for use in the hazardous area and must installed, operated and maintained based on manufacturers specifications.
In reference to operating electrical equipment, it must be stated that no one who is unqualified or unauthorized will operate electrical equipment. This is a requirement that under no circumstance will be neglected. It can be viewed as a Golden Rule due to the potential ramifications of an electrical accident.
Another important issue to address is if a device is unable to operate because of an over current device; the cause must be investigated and resolved before re-energizing the device. This means you can’t just replace a fuse or make a setting change, unless uncoordinated to your system, to keep the device from operating. It is very important that the cause is determined as it may save you from a greater incident in the future.
Along the same lines, interlock systems shall not be bypassed or otherwise rendered inoperative while the equipment is energized, except when testing is being performed or when work is being completed under an Energized Electrical Work Permit. A low voltage qualified person shall perform these tasks. Upon completion of the task, the interlock system shall be restored to full operable condition. Under no other circumstances shall the interlock system be disabled or permanently rendered inoperable. You must address that the work environment is clear of hazards and suitable to safely complete the task at hand.
Working overhead should address that all small equipment and tools used aloft shall be raised and lowered by a non-conductive hand line (such as clean polypropylene), canvas bucket, or other suitable method. Nothing shall be thrown or intentionally dropped. Personnel shall take care when working overhead to prevent dropping tools and materials. Personnel below are to stay clear of overhead work to avoid being struck by falling objects.
This concludes the third part of my 5-part blog series on ESPs. The fourth part will continue to cover Required Safe Work Practices. Again, if you have any questions please feel free to contact us and we would be more than happy to discuss with you.
About the author
Jason Mazzola is the Director of Electrical Safety Services for Southern New England out of our Mansfield, MA office. He joined Hallam-ICS in 2019 and prior to that spent 10 years in utility industry in various engineering and leadership roles.
About Hallam-ICS
Hallam-ICS is an engineering and automation company that designs MEP systems for facilities and plants, engineers control and automation solutions, and ensures safety and regulatory compliance through arc flash studies, commissioning, and validation. Our offices are located in Massachusetts, Connecticut, New York, Vermont and North Carolina and our projects take us world-wide.
You May Also Like
These Related Stories
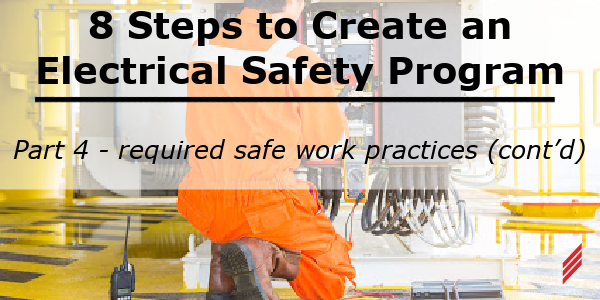
8 Steps to Create an Electrical Safety Program Part 4
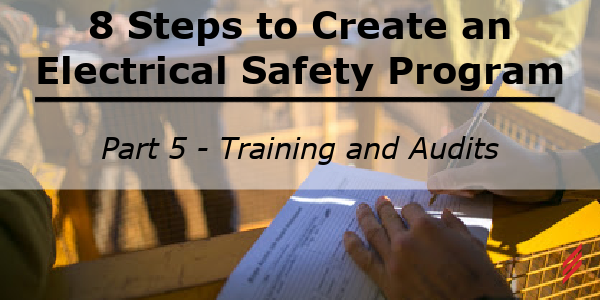
8 Steps to Create an Electrical Safety Program Part 5
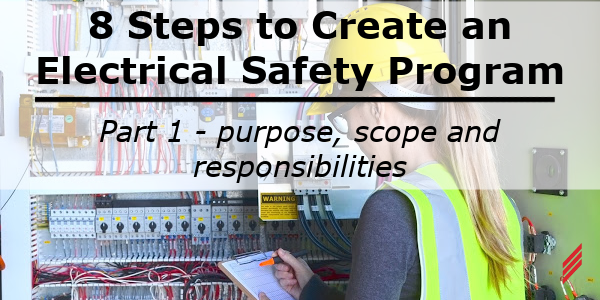
No Comments Yet
Let us know what you think