8 Steps to Create an Electrical Safety Program Part 2
by Jason Mazzola on Jan 21, 2021 10:30:00 AM
Welcome back to my 5-part blog series on Electrical Safety Plans. In part 2 we will continue on to the next sections to consider when creating your document.
I will cover Requirements and Protective Measures in this section. This will be more content heavy section than the ones discussed in part 1.
Part 1: Purpose, Scope and Responsibilities
Part 2: Requirements and Protective Measures
Part 3: Required Safe Work Practices
Part 4: Required Safe Work Practices Continued
Requirements
Requirements will be the next section of your plan. This is going to be one of the more robust sections of your electrical safety program. You will set the parameters for a person to be qualified, including the appropriate training and experience for a given task. Other topics in this section should include;
- Risk Assessments
- Fall protection
- Human Error
- Job Safety Planning
- Emergency Preparedness
- Investigations
Outlined in your plan you need to include the need to conduct “Risk Assessments” to identify all hazards, electrical or not. Remember sometimes the biggest hazard could be hidden or not in your direct work site, so it’s a good idea to step back and look at the big picture. This is a practice I would encourage you to instill in your workers. Address that any hazards found need to be addressed to create the safest work environment possible. As part of the assessment, shock and arc flash risk should be evaluated. This should include at a minimum the voltage, and shock boundaries for that voltage as laid out in NFPA 70E, and the PPE requirements that must be implemented.
The second component of this is the arc flash risk assessment. You need to have an arc flash study conducted for your site or be familiar with the table method laid out in NFPA 70E. You are responsible to provide the appropriate labels for your equipment reflecting the information associated with the hazard. This information can be found in the NFPA 70E document. To summarize, the label can contain the available incident energy OR the PPE Category listed in the tables in Article 130.7 of 70E, the minimum arc rating of clothing rating, and/or a list of specific PPE required by your worksite as determined by your management. The main goal of an arc flash hazard label is to inform employees about the hazard and provide them with the information they need to select PPE and perform work safely.
Your plan should lay out your company's fall protection requirements. If you determine there is a need for fall protection the risk should be evaluated to determine the level of protection required to safely work at heights. If working on electrical equipment in an elevated state, the fall protection harness must meet ASTM F 887 and be arc rated. This is an important point to consider when choosing fall protection for your group. I would recommend if there is ever a chance that your staff may be presented with an electrical hazard while wearing a harness you should just choose a good arc rated harness. There is no need to have two different harnesses, as either will provide adequate fall protection.
A good section to include is human performance and you should establish tools to combat human error. Some examples are including job planning and pre-job briefing and procedural checklists. I have found pre-job briefings to be a great tool to address human error. It also works as a great tool to get everyone on the same page before the work starts. It should be a time to review the job, talk about hazards, go over procedures, and answer any questions that the crew may have. There are a lot of great tools out there for combating human error and it should not be overlooked and needs to be integrated into your plan.
Another section to include in your plan is job safety planning. Your company needs to determine the appropriate requirements to include but at a minimum I would ask that you consider:
- Hazard identification
- PPE
- Work Zones
- LOTO
- Site-specific procedures you have created
- Emergency response plan
- Fall Protection and the need for it
One section to not overlook is your emergency plan. In the case where someone is injured you want to lay out what will happen and what not to do, such as touch the victim until source voltage is de-energized or they are clear of the hazard. A plan for calling for help should be included; this small section could mean the difference between life and death of a colleague if an incident occurs.
It is also important to include some kind of incident investigation standard in your plan. This will follow whatever method your company chooses to implement. The investigation should take place if an event occurs or if an event could have occurred and changes should be made based off of your findings. This is a very important concept for improving workplace safety and should be included. These simple investigations and findings reports can lead to changes in work practices and can increase overall safety within your group.
Protective Measures
The next component of your electrical safety plan will be protective measures; this will address PPE and Tools. This section’s intent is to establish the minimum PPE requirements that your staff will need to adhere to. You should address how to choose the proper PPE to combat an arc flash hazard, either based off your arc flash study or using the table method. It would be a good idea to include the most up-to-date PPE tables in this section for reference. This table can be found in the NFPA 70E document. Other forms of PPE that need to be considered are head, eye, hearing, foot, hand, and fall protection requirements. It is important to make sure that your chosen PPE requirements are meeting all specifications set forth by ASTM and your company policies. With a simple search you should be able to find information on these requirements online.
A section outlining tool selection when working on or near energized parts should not be overlooked and needs to be clearly defined. At a minimum, tools must be 1000V rated insulated and most importantly they need to meet the ASTM F 1505 requirement. The manufacturer will have specific requirements for care of the tools, these should be included in your plan as well. These tools are expensive and if not properly cared for they can become damaged and then would need to be removed from service.
This concludes the second part of my 5-part blog series on ESPs. These sections are going to be time consuming and you need to give a good amount of thought into what requirements you want to include. Fortunately, NFPA 70E has a good road map for creating a compliant work environment. Remember that 70E represents the minimum best practice requirement so please feel free to add things that you feel will make your workers safer. Again, if you have any questions please feel free to contact us and we would be more than happy to discuss this with you.
About the author
Jason Mazzola is the Director of Electrical Safety Services for Southern New England out of our Mansfield, MA office. He joined Hallam-ICS in 2019 and prior to that spent 10 years in utility industry in various engineering and leadership roles.
About Hallam-ICS
Hallam-ICS is an engineering and automation company that designs MEP systems for facilities and plants, engineers control and automation solutions, and ensures safety and regulatory compliance through arc flash studies, commissioning, and validation. Our offices are located in Massachusetts, Connecticut, New York, Vermont and North Carolina and our projects take us world-wide.
You May Also Like
These Related Stories
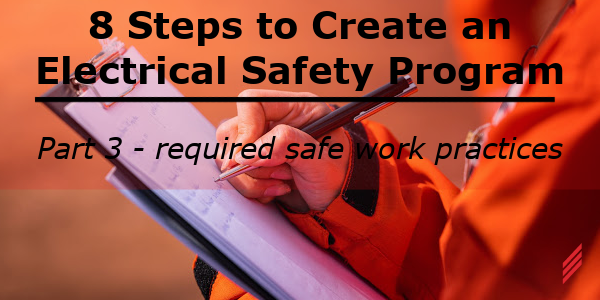
8 Steps to Create an Electrical Safety Program Part 3
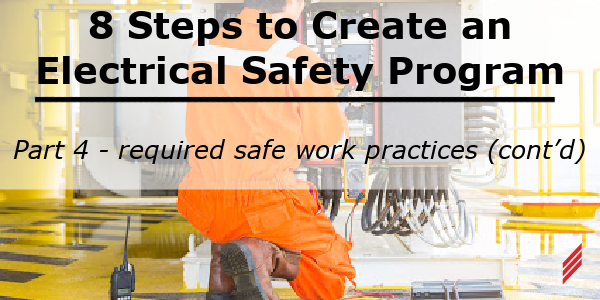
8 Steps to Create an Electrical Safety Program Part 4
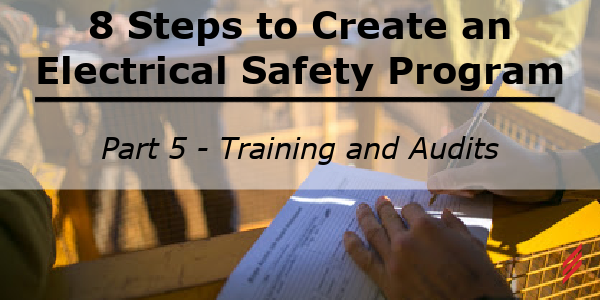
No Comments Yet
Let us know what you think