DC to AC Drive Conversions - Getting Started
by Chris Giusto and Dan Laird on Apr 7, 2022 10:27:34 AM
From the Authors
With over 40 years of combined experience in industry, Dan Laird and I have designed mechanical and electrical systems for an extensive range of facilities.I began my career designing machinery for industrial facilities before eventually transitioning to consulting. My technical strengths are in process improvements, equipment arrangement, material handling, and custom equipment design and fabrication. Dan has an extensive background in drive systems and control, including coordinated systems of continuous processes. We have spent the majority of our professional lives working in and around industrial facilities.
Introduction
We have developed two blogs to help make sure your change from Direct Current (DC) motors to Alternating Current (AC) motors is successful, regardless of why you have decided to make that change. This blog will focus on design considerations such as torque and speed. The next blog will provide specifics on installation considerations that must be taken into account for an effective conversion.
Many online resources discuss at length the advantages and disadvantages of using DC or AC motors for a given application. While an in-depth discussion of this topic is not the goal here, it is worth mentioning that maintenance requirements for DC motors is a common reason that facilities choose to change to AC motors. DC motors use brushes and commutators to transmit current to the rotor, and over time brushes wear and must be replaced. While brushes are usually relatively affordable, the down time [read: lost production] required for replacement can be substantial, especially in facilities that operate 24/7. Such plants must minimize downtime to maximize profitability, and running 24/7 also means brushes will wear faster and must be replaced more frequently. In applications where an AC motor can offer equivalent performance, eliminating the maintenance required by DC motors is often desirable.
Where to Start?
Replacing a DC motor with an AC motor is not as simple as buying a new motor with the same horsepower rating and installing it in place of the old one. For a successful conversion, many details must be addressed.
Torque and Speed
To begin, it is critical to understand what the existing drive is doing. Not just the motor, but the complete drive package. This includes whatever means of speed control might be used, as well as the mechanical power transmission components between the motor and the drive shaft of the machine. In the simplest case, the drive might consist of a motor that only operates at one speed and is direct-coupled to the drive shaft. In this case, the motor output (speed and torque) is equal to the drive shaft input.
More complicated applications can operate at various speeds and involve multiple belt and/or chain drives and/or gearboxes that can change the speed and torque from the motor output before it is delivered to the drive shaft. The end goal is to ensure the new drive can deliver the same amount of torque to the drive shaft at the same speed(s).
When selecting an AC motor to replace a DC motor, it is important to consider the differences in the torque curve. DC motors tend to offer higher torque at lower speeds which can be valuable when starting a machine under load, or when quick acceleration is required. It may be necessary to use an AC motor with a higher horsepower rating to ensure the proper amount of torque is available at start up or at lower motor speeds. DC motors also produce constant torque across the operating speed range of the motor. AC motors can be equipped to do this, but must be specified accordingly. If you are not sure how to select an appropriate AC motor, a knowledgeable motor vendor should be able to help you.
Selecting a replacement AC motor with the correct output speed could be straight forward or relatively complex, depending on the application. Considerations related to speed will be discussed in greater detail below. For now, just remember that you must know the output speed of your existing DC motor, and you may need to know the speed of the drive shaft for your piece of equipment.
Constant Speed vs. Variable Speed Applications
As alluded to already, constant speed applications are simpler. If an AC motor is available with the same output speed as the existing DC motor, then the next step is to evaluate the installation considerations. If not, it is usually preferable to select an AC motor with higher output speed and reduce the speed with a Variable Frequency Drive (VFD) or via mechanical speed reduction.
With variable speed applications, the new AC motor must have a maximum output speed capable of delivering the maximum required equipment speed. As discussed above, but worth mentioning again, drives that are also required to operate at low speeds must be capable of delivering the required torque at those slower speeds. Once a motor with acceptable speed output is identified, the next consideration is speed control.
Speed Control
A DC motor has a nameplate rating showing base speed/top speed in RPM. The torque is constant below base speed and decays between base speed and top speed. The horsepower increases linearly from zero to base speed. Above base speed, the motor has constant, nameplate rated HP. The first thing to consider is whether the load needs constant torque like a conveyor or extruder, or needs constant HP like reels and bridles on a continuous strip operation.
fig 1: Field current vs. RPM and armature voltage vs. RPM for DC motor
For a constant torque load, the speed is controlled by varying the armature voltage and keeping field current constant at maximum value. The motor should achieve base speed in RPM with rated armature voltage and full field current. This speed and armature voltage are linear in this range.
For a constant HP load, the speed is controlled by weakening the field current and keeping armature voltage constant at its nameplate value. The motor should achieve top speed in RPM with rated armature voltage and minimum field current.
fig 2: Torque vs. RPM at various frequencies for AC induction motor
On an AC motor, speed can be controlled adjusting the supply frequency. The torque, however, is normally maintained by regulating the Volts/Hz ratio.
Electrical Power
On the DC motor, torque is proportional to armature current. Even at low speeds, high torque can be achieved by simply regulating armature current. On an AC motor, however, the stator has to be excited with magnetizing and torque producing flux, which tends to fall off as voltage and frequency near zero. As a result, the older AC drives that simply regulated the Volts/Hz ratio had difficulty controlling torque at low speeds. Flux vector drives with encoder feedback now allow AC motors to achieve rated torque at lower speeds. The torque required for acceleration and sudden load changes must also be considered. If these short time torque requirements are significant, a higher horsepower AC motor than DC motor may be required to handle the load.
For coordinated drive systems on continuous processes, determining the HP and torque requirements is more complicated. Ideally, a tension profile of the process is created that determines web tension at each motor for a range of materials produced. This requires all of the mechanical characteristics of the line to be known such as roll diameters/widths, cylinder pressures/areas, gear ratios, angles of wrap, friction coefficients, and storage dimensions. Material characteristics such as thickness, width, yield strength, line speeds, tension settings, and loop settings must also be known. For each motor, armature voltage, armature current, and field current are recorded for a representative sample of materials. This information is placed into a model and used to determine the range of horsepower and speeds required to manufacture all products. Once this is known, appropriate motors, gearboxes, and drives can be selected.
Installation Considerations
We hope this has provided you with a starting point for you conversion. Our next blog will provide important installation details to help make your project successful.
About the Authors
Chris Giusto is Director of Industrial Projects and works primarily with industrial facilities to improve processes & safety, reduce waste & energy consumption, increase flexibility & capacity, and build new facilities. He has over 15 years of experience in mechanical engineering including design and specification of equipment and systems, detailed machine design, and construction administration. Areas of expertise include process evaluation and optimization, material handling, and custom equipment design and fabrication.
Read My Hallam Story
Dan Laird has left Hallam-ICS to pursue other endeavors, but his contributions to the company continue to be valued.
About Hallam-ICS
Hallam-ICS is an engineering and automation company that designs MEP systems for facilities and plants, engineers control and automation solutions, and ensures safety and regulatory compliance through arc flash studies, commissioning, and validation. Our offices are located in Massachusetts, Connecticut, New York, Vermont and North Carolina and our projects take us world-wide.
You May Also Like
These Related Stories
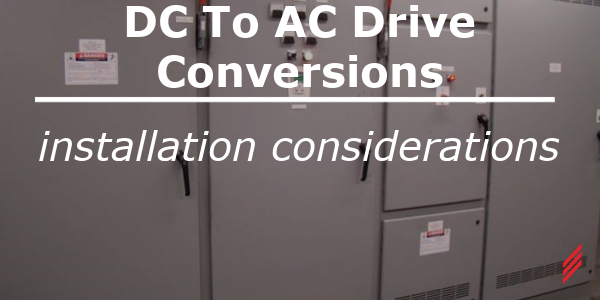
DC to AC Drive Conversions – Installation Considerations
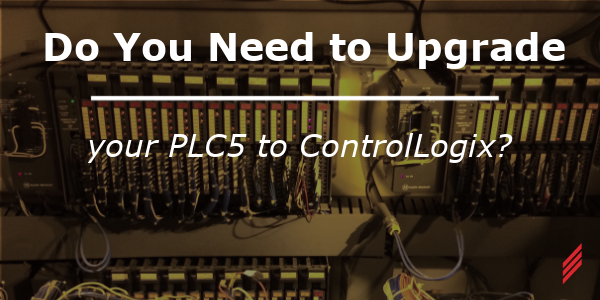
Do You Need to Upgrade Your PLC5 to ControlLogix?
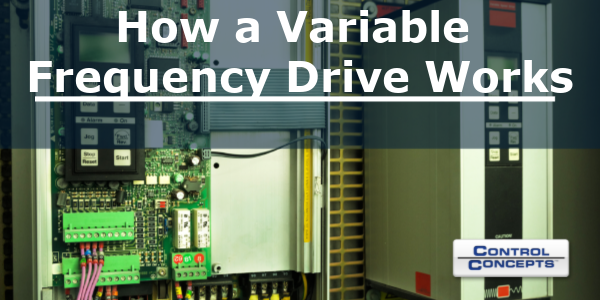
Comments (18)