How a Variable Frequency Drive Works
by Jeff Conner on Jul 7, 2020 10:30:00 AM
Using a variable frequency drive (VFD) can save you on energy costs and consumption. VFDs can also tighten processes, reduce maintenance, increase production, and prolong the life of your equipment.
What Is a VFD?
A VFD or variable frequency drive is an electronic device used to control an AC induction motor or synchronous motor. A VFD controls the torque, speed, and direction of the motor, smoothly starting and accelerating the motor to the desired speed at a controlled acceleration rate. Deceleration is also controlled, and braking is available as an option.
VFDs allow you to use a single motor for a variety of processes and conditions that may require different speeds. Other names for a VFD include:
- Adjustable speed drive
- Adjustable frequency drive
- Variable-voltage/variable frequency drive
- AC drive
- Microdrive
- Inverter
- Variable speed drive
Unlike the fixed frequency supplied by utility power which runs the motor at full speed all the time, the variable frequency drive provides flexibility as well as cost-savings in manufacturing and other industries. VFDs are available in a range of types and ratings from less than 1 horsepower to thousands. Also, you can choose from PWM V/HZ scalar control, PWM closed loop vector control, open loop vector control, direct torque control (DTC), and other motor control methods.
How a VFD Operates
A variable frequency drive takes in fixed AC voltage and frequency into a rectifier bridge to convert the voltage to DC, uses a capacitor bank and inductors to filter the DC, then inverts the DC voltage back to AC and sends it out to the motor at the frequency desired.
- A microprocessor or digital signal processor (DSP) communicates with the PLC and user (via an HMI or keypad), oversees motor operation and checks for faults.
- Control circuitry coordinates the switching of power devices to activate the power components in the right sequence. The motor speed varies by changing the voltage and frequency supplied by the output devices.
- Basic VFDs maintain motor torque by keeping the volts-to-frequency ratio constant. Advanced units use more intelligent & adaptive algorithms to improve motor performance.
In short, a VFD translates one voltage and frequency to another to change motor speed without losing torque.
A VFD drive system could be divided into three subsystems:
- An AC motor, most often a three-phase induction motor but sometimes a single-phase or synchronous motor.
- A main drive controller using a solid-state power electronics conversion system containing the rectifier bridge converter, a DC link or filter, and a switching or inverter section.
- A monitoring and control interface, providing the operator or PLC a way to start and stop the motor, adjust the speed, change direction, etc. This interface also provides information about the operation of the motor, health of the drive, etc. Communication with a PLC may be accomplished through a number of serial communications protocols or may be through “old school” relay inputs and output combined with 4-20mA or 0-10V analog signals.
Over the decades, variable frequency drives have become smaller, thanks in particular to microprocessors replacing solid-state components. In many applications, drives often have a return on investment above the price of the drive.
When to Use a Variable Frequency Drive
VFDs are used on systems run by AC electric motors in applications from manufacturing to air conditioning. There are many reasons to select a system with a variable frequency drive.
- To precisely control the speed of a manufacturing process.
- To provide a smooth start and careful acceleration to operating speed.
- To create energy savings, especially in applications where a load’s torque and power vary in a non-linear way. Variable torque fans & pumps are good candidates for savings.
- To make process and quality improvements in your application’s acceleration, flow, monitoring, speed, temperature, tension, torque, and pressure.
- To run a motor in specialized patterns to minimize mechanical and electrical stress.
VFDs significantly reduce or eliminate the current surges needed to start a motor “across the line.” Besides current surges of up to eight times the motor’s full-load current, this kind of starting can be damaging to mechanical components in the driven load as well.
Keeping Your Variable Frequency Drive and Equipment Running
A little maintenance is all a VFD asks of its operators. Keep the drive free of dust, ensure you have proper ventilation, and keep everything dry and protected from moisture. Occasionally check to make sure all electrical connections are tight.
VFDs are incredibly reliable devices. When a VFD does indicate a fault, onboard diagnostics can help determine the cause and sometimes the remedy. Many faults do not represent a failure in the VFD itself, but may mean problems with incoming power, the motor, or the driven load.
A variable frequency drive, whether regulated manually or with a PLC, can help you tighten your process controls while increasing production. Costs for maintenance and repairs across your lines go down, as does your electricity bill.
With fewer errors and less downtime, your bottom line will grow with less effort from you and your equipment.
About the author
With over 25 years of experience in the industrial automation repair industry, Jeff Conner is the Dallas Service Manager for Control Concepts and serves on the Advisory Committee for the Electronics Technologies Department at Texas State Technical College.
Control Concepts helps design, fabricate, install, test, and program control systems. They service almost any brand of control found in automated systems and can send an experienced technician anywhere, wherever one is needed 24 hours a day, 7 days a week.
About Hallam-ICS
Hallam-ICS is an engineering and automation company that designs MEP systems for facilities and plants, engineers control and automation solutions, and ensures safety and regulatory compliance through arc flash studies, commissioning, and validation. Our offices are located in Massachusetts, Connecticut, New York, Vermont and North Carolina and our projects take us world-wide.
You May Also Like
These Related Stories
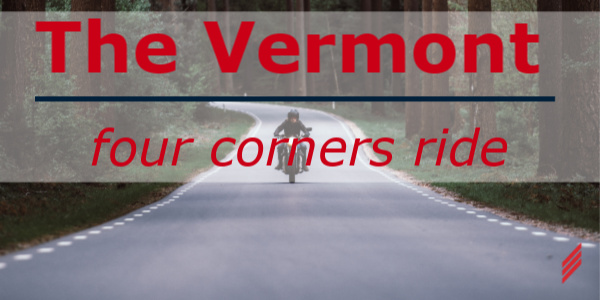
The Vermont Four Corners Ride
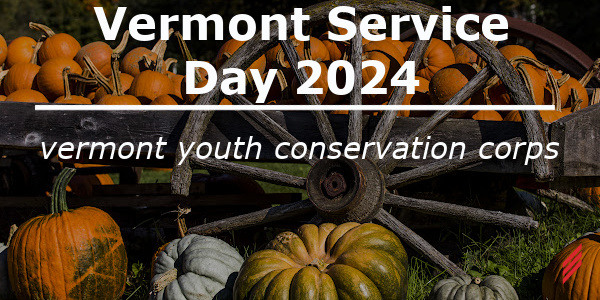
Vermont Service Day 2024 – Vermont Youth Conservation Corps
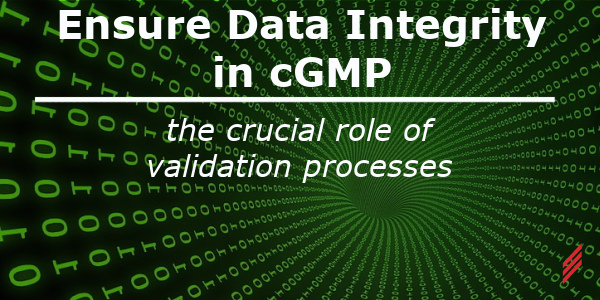
Comments (5)