Designing for AIC Ratings in Low Voltage Panelboards
by Jeff Babineaux, PE on Oct 3, 2024 10:30:00 AM
I hate giving people bad news. I also hate when people use words like ‘hate’ when they really mean a mild dislike of something. In conjunction with the arc flash studies that we offer, we will occasionally run into existing electrical distribution equipment that can’t handle the worst-case short-circuit fault current, and we have to give bad news. The hardest part of an existing equipment evaluation report is a recommendation that things aren’t okay when to date, everything has pretty much operated as needed.
We don’t do arc fault calculations for typical scenarios, though, nor do we consider average short-circuit current when we make sure that breakers will withstand a fault. What is fault current? What happens if our protection devices aren’t sufficiently rated for the worst case? How can we make sure that it’s installed correctly the first time, and what can we do to mitigate costs for remediation when we find something installed that is over-duty?
Fault Current
When the electrical system is in an abnormal condition, it is considered to be in fault. The resulting current is the fault current, which can exceed normal limits, damaging the distribution system (cables, buses, transformers, etc.) or utilization equipment (the expensive stuff that you connect to the outlet). The motors, transformers, and other inductive loads on your system can’t stop on a dime, though. These things will provide a decaying DC offset that reduces to zero over time. The resultant fault current looks something like the waveform below, taken from IEEE’s guide on protection of power systems (IEEE Std 242).
Figure 1: Fault Current Sinusoidal Wave with AC and DC Contribution (IEEE 242)
The driving factor that determines how fast this waveform goes to steady-state is the X/R ratio, or the ratio of reactance (inductive/capacitive) to resistance of the system. This X/R ratio is related to the power factor of the system, in that the power factor is the ratio of real to apparent power, and a high reactance produces a low power factor.
Figure 2: The Power Triangle
Figure 3: The Impedance Triangle
Understanding where this reactance comes from and how it relates to the power factor of your system will help with mitigation, but let’s set that aside for now and talk about how our protective devices should clear this fault current.
To Clear, or Not to Clear
Protective devices are rated to clear this fault current up to a point, but it takes money to build in robust protection. Devices at the far end of the distribution won’t see nearly as much current even in the worst-case fault, so manufacturers offer more economical ratings. Most people’s homes, for example, have breakers rated for up to 10kAIC (thousands of Amps Interrupting Current), while industrial low voltage distribution at 480V are more likely to be rated at 65kAIC. Other typical breaker ratings include 22 and 42kAIC, and code requires us to make sure we size them correctly (NEC 110.9).
Switchgear, switchboards, motor control centers and panelboards (defined here as the assembly of main circuit breakers, buses, and the branch circuit breakers provided as a single assembly) will be either fully-rated (minimum AIC rating on the panel equals the fully-rated value) or series-rated (a tested combination of different AIC ratings with total rating defined by the manufacturer). This AIC rating must meet or exceed the calculated fault current in order to properly clear the fault. If it doesn’t, your protection fails and the event just keeps going until copper melts/vaporizes and breaks the circuit, something else on the system clears it, or the grid runs out of fuel. This is why it is so profoundly important to consider the worst-case scenario, and why IEEE 242 uses the worst case up to and including a bolted fault current, which will likely never happen.
The system X/R matters here because the longer it takes for the fault current to decay, the more energy is going into the pieces and parts holding our overcurrent devices together, and the mechanisms that allow them to open the circuit and cut power to the downstream devices. UL tells manufacturers how to test their equipment, and circuit breakers are each tested at a specific X/R to come up with this number. For many manufacturers, these are tested at an X/R of 1.75, or an approximate 50% power factor.
A short-circuit event changes this, though. Enter Thevenin’s Theorem. IEEE 242 talks about the nature of short-circuit currents, noting that the reactance of the load is predominantly resistive, while the reactances of the source and circuit are predominantly inductive. When the load is evaluated using Thevenin’s Theorem, it is shorted, and the current now lags the voltage by an angle approaching 90° (heavily inductive, power factor nearing 0.0). While the length of cables introduces a capacitance to offset the inductive nature of transformers and utility sources, it still means that the X/R at the protective device will typically be very close to the X/R of the upstream transformer (mostly inductive, so much higher X/R, so much longer decay).
This difference between the manufacturer’s tested X/R and the system X/R means that we need to apply a multiplier to the calculated fault current to more accurately ensure that the breaker can open in the worst-case scenario. IEEE 242 has a table for that, or your calculation software should provide the additional step. SKM has a great article explaining how they do it, and the link can be found at the end of this article.
Sizing For Worst Case: Early Assumptions and the Requirement for Evaluation
It would be great if we knew on day 1 of design what the fault current would be across our system. It would be great on day 2, or day 90. These things take time, though, so we need a preliminary guess to help us in early design to plan for breakers that might take longer to order. IEEE 242 provides a list of multipliers depending on the AIC rating of the breaker, and we can make some assumptions about the X/R and fault current characteristics of the upstream transformer.
When we’re taking our first guess, the X/R of 480V-primary transformers might be assumed around 3 to 4.5, which gives a multiplier of 1.28 for 10kAIC breakers, 1.09 for up to 20kAIC, and 1.00 beyond. Typical impedance of an outdoor pad-mount transformer is conservatively 5%, and indoor three-phase dry-type transformers are 1.5% up to 150kVA, 3% up to 300kVA, and 5% beyond. Single-phase transformers will have a conservative impedance of 1.5% up to 50kVA, 2% up to 100kva, 3.5% up to 500kVA, and 5% beyond.
To find the estimated fault current, we first calculate the theoretical fault current of the transformer using the equation below:
Apply the multiplication factor from IEEE 242 based on the approximate AIC ratings of the breaker (1.28, 1.09, or 1.00).
Finally, understand that these numbers are just a good place to start. In our client’s case, a very large distribution with many transformers and motors drove the system X/R well over 4.5. A comprehensive study calculating fault current and system X/R values at the completion of the electrical system design is the best way to ensure your equipment is properly rated.
Remediation: How to Correct a Problem Found in the Field
There are several options to mitigate over-duty breakers on an existing system. The most direct solution is to replace the breakers with those rated at an appropriate AIC rating for the calculated fault current. Where a large panelboard with numerous over-duty breakers exist at the end of distribution, a current-limiting fused disconnect can reduce the available fault current. Providing a series rating for panels can be helpful, but this must be done by consulting the manufacturer’s tested series rating data, which makes future breaker replacements difficult. Where system-wide X/R values drive several distribution points over the rated values, capacitor banks will increase the power factor of the system while lowering system X/R.
Conclusion
NEC tells us that we need to make sure that the protective devices can withstand fault levels, and determining these levels needs to be done when a clear picture of the electrical distribution is achieved at the end of design. System X/R plays a factor, and multiplies fault current by a much higher value on breakers rated at 10kAIC at the farthest end of distribution.
If you’d like to know more about how these studies are done, what our experience is with our two favorites (SKM and EasyPower), or if you have any concerns about the state of your current system, please feel free to reach out! Hallam-ICS performs studies like this all over the country, and we would be happy to help.
References:
IEEE Std 242 – Recommended Practice for Protection and Coordination of Industrial and Commercial Power Systems
SKM, What is the Purpose of the Equipment Evaluation Study Module, https://support.skm.com/KB/View/3725-what-is-the-purpose-of-the-equipment-evaluation-study-module-
About the Author
Jeff has a B.S. in Electrical Engineering from Louisiana Tech University. Prior to coming to Hallam-ICS, Jeff had 7 years of experience working in prefab construction for mechanical and electrical buildings and skids. He holds a professional engineering license in multiple states, participates in all phases of the project design from concept through construction, and cooks a mean gumbo.
Read My Hallam Story
About Hallam-ICS
Hallam-ICS is an engineering and automation company that designs MEP systems for facilities and plants, engineers control and automation solutions, and ensures safety and regulatory compliance through arc flash studies, commissioning, and validation. Our offices are located in Massachusetts, Connecticut, New York, Vermont and North Carolina and our projects take us world-wide.
You May Also Like
These Related Stories
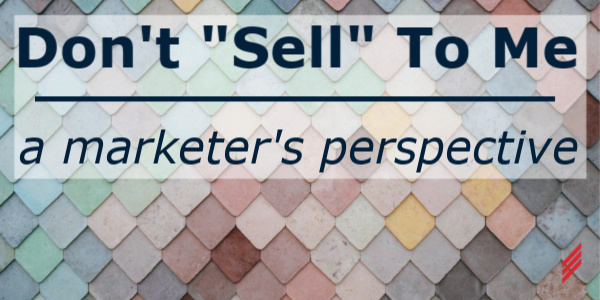
Don’t “Sell” To Me – A Marketer’s Perspective
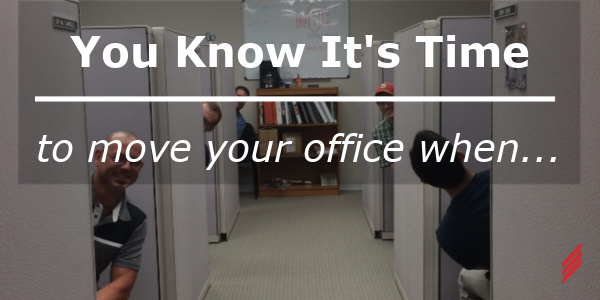
You know it’s time to move your office when…
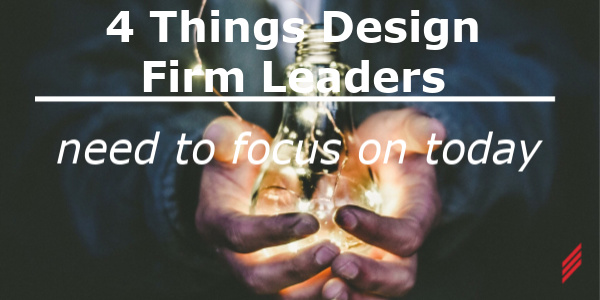
No Comments Yet
Let us know what you think