Industrial Sensor Data Integration with Ignition
by Elizabeth Engler on Jul 17, 2025 10:30:00 AM
Centralizing Data in Complex Industrial Environments
Modern industrial manufacturing facilities rely on hundreds—if not thousands—of process instrumentation devices to monitor automated processes, equipment, and building systems. As sensor technology advances and installations proliferate, managing the resulting data deluge becomes increasingly challenging. Even when standardizing across one or several brands, and especially across multiple vendors, devices have unique communication protocols, data formats, and connectivity requirements, which can create a fragmented data landscape. Disorganized and scattered data risks overlooking critical insights, complicates maintenance, and hinders data-driven decision-making. Ignition by Inductive Automation rises to the challenge with a robust, flexible, and scalable platform for aggregating and visualizing sensor data. We will explore how Ignition unifies data, delivers actionable insights, and ensures secure access for stakeholders onsite and remotely.
Universal Device Connectivity and Communication
We’ve used Ignition to interface with a wide range of devices, regardless of brand, protocol, or connection type. Its gateway includes native drivers for seamless communication with major programmable logic controllers (PLCs) and protocols, including:
- Allen-Bradley PLCs: Direct tag browsing and communication for ControlLogix, CompactLogix, MicroLogix, PLC5, and SLC 5/05.
- Siemens S7 PLCs: Connect to S7-300, S7-400, S7-1200, and S7-1500.
- Modbus TCP/RTU: Widely used for sensors, requiring only a Modbus address-to-datapoint mapping from device documentation.
- IEC 61850 MMS: For electrical substation automation and compatible devices.
- TCP/UDP Protocols: For custom or proprietary device communication.
- OPC-UA Server/Client: Embedded OPC-UA functionality enables Ignition to serve its own tag data and interface, as well as read/write from other OPC-UA-compliant devices, such as Beckhoff TwinCAT PLCs.
For sensors lacking native digital communication, such as those using 4-20mA or 0-10V analog signals (common in HART-enabled process instrumentation), we deploy cost-effective adapters like analog-to-Modbus TCP or HART-to-Modbus TCP converters. These adapters are simple to setup and translate analog signals into digital data streams, which Ignition ingests effortlessly.
Emerging IoT-enabled devices often provide JSON-based REST APIs. Ignition supports these through its scripting capabilities, allowing integrators to parse and process API responses. This flexibility ensures compatibility with both legacy and modern devices, future-proofing your data infrastructure.
Practical Example: Modbus TCP Integration
To integrate a temperature sensor via Modbus TCP, obtain the device’s Modbus register map (e.g., register 40001 for temperature in °C). In Ignition, configure a Modbus TCP device connection, map the register to a tag, and the data becomes available for real-time monitoring or historical logging. This process typically takes minutes, minimizing setup time.
Dynamic and Informative Visualization
Ignition’s Designer tool empowers engineers to create tailored dashboards that present data in a clear, actionable format. Device’s real-time status is always available and can be stored along with calculations to create historical trends for complex analysis. Display live status and trends with any of the available components:
- Process Symbols: P&ID-style representations of equipment and workflows.
- Gauges and Meters: Real-time value displays for pressure, temperature, or flow.
- Charts and Graphs: Time-series trends, histograms, or scatter plots for historical analysis.
- Tables: Expandable rows for detailed data exploration.
- Progress Bars and Indicators: Visual cues for thresholds or operational status.
- Printable PDF Reports: Feed data into custom PDF reports which can be emailed, downloaded from Ignition data views, and printed. Now data can be shared across the organization and in multiple settings.
Each component and view are fully customizable, to create responsive and dynamic displays which stretch or shrink to fit any screen size and resolution. Multiple display types are supported including HMIs, TV monitors, laptops and desktop computers, smartphones, and tablets. Engineers can modify dashboards on the fly, adding new tags, adjusting layouts, or incorporating calculated metrics – without disrupting operations. Published updates are instantly available to users, ensuring timely access to critical information.
Safely View Data Onsite and Remotely
Ignition centralizes data from disparate sources into a single platform, accessible onsite as well as remotely. With clear data in your hands and enlightening historical analysis, suddenly the answers are apparent to once puzzling enigmas and teams can make powerful informed decisions. Ignition protects projects and data by authenticating users internally, against a SQL database, using Active Directory, or allowing administrators to connect Federated Identity Providers (idP). We assign roles and security zones to users to limit access to projects and pages. Remote on-demand access gives you statuses on a moment’s notice when you need them most, and can be accomplished safely with VPNs, SSH, reverse proxies, or other secure connections.
Q&A: Industrial Sensor Data Integration with Ignition
Q: What is the main challenge when integrating industrial sensors with SCADA systems like Ignition?
A: The biggest challenge is getting raw sensor data into a usable digital format that can be read by SCADA platforms. This often involves selecting the right hardware and communication protocols to bridge the gap between physical sensors and software systems.
Q: What role do edge devices play in sensor integration?
A: Edge devices act as translators or data aggregators. They collect data from sensors, convert it into a standard protocol (like MQTT or Modbus), and send it to platforms like Ignition for visualization, logging, and control. These make it possible to communicate with LoRaWAN, HART, and analog devices which don’t have a direct native communication driver in Ignition.
Q: Why use Ignition for sensor data integration?
A: Ignition offers flexibility, scalability, and a wide range of connectivity options. It supports multiple modern protocols and tools (like MQTT, OPC UA, REST APIs, Modbus RTU/TCP, UDP, IEC 61850 MMS, and native Ethernet drivers for some devices). Not only is Ignition capable of communicating with any sensor, it’s a powerful platform to work with for developing applications to view your collected data. Its modular nature means you pay for what you need, and you can expand your system with time to incorporate multiple interconnected gateways. The designer and publishing makes app development easy, fast and instantly usable. These features make it ideal for building robust, real-time monitoring systems.
Q: How can I ensure the accuracy of integrated sensor data?
A: It’s essential to validate sensor calibration, ensure reliable communication, and implement logic within Ignition to flag anomalies or data dropouts. Most sensors come with indicators or settings to display faults and these can be read and interpreted in Ignition. All data readings come with a timestamp and basic diagnostic information, which makes it easy to identify old or faulty data. Conduct thorough testing and verification during integration to establish data integrity, and set up alarms or status indicators in the application to show data age and quality.
Q: Can older sensors be integrated with Ignition?
A: Yes, many legacy sensors can be integrated with the help of converters or edge devices that translate outdated protocols into something Ignition can understand. Let us know the specifics of your sensor devices and we can prescribe the best conversion and collection tools to gather and use your data.
Do you have questions about data collection or process instrumentation expansions? Contact us for more information or to assist with your integration needs.
About the Author
Elizabeth Engler is a Controls Integrator with diverse experience across controls design, programming, and software development. She enjoys logical challenges, user interface design, and programming machines to bring customer's visions to life. In her free time, Elizabeth enjoys gardening, mysteries, movies, and time with family.
Read My Hallam Story
About Hallam-ICS
Hallam-ICS is an engineering and automation company that designs MEP systems for facilities and plants, engineers control and automation solutions, and ensures safety and regulatory compliance through arc flash studies, commissioning, and validation. Our offices are located in Massachusetts, Connecticut, New York, Vermont and North Carolina, Texas and Florida and our projects take us world-wide.
You May Also Like
These Related Stories
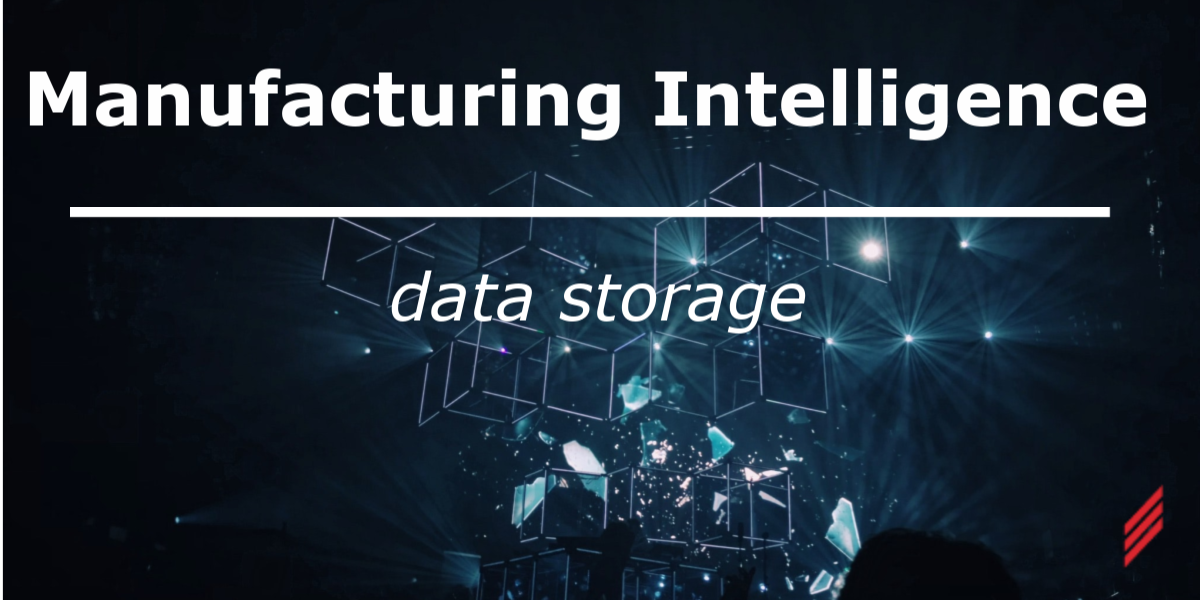
Manufacturing Intelligence - Data Storage
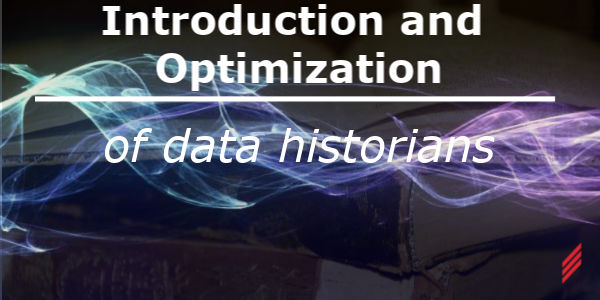
Introduction and Optimization of Data Historians
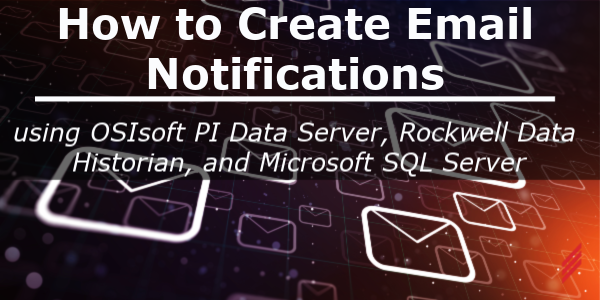
No Comments Yet
Let us know what you think