Notes From the Field- Unqualified Arc Flash Firms Create Safety & Compliance Issues
by Scott King, PMP on Jul 3, 2019 9:08:00 AM
Over the past 10 years, my team has conducted hundreds of Arc Flash assessments for a range of clients, including municipalities, K-12 schools, colleges & universities and industrial facilities. We’ve also walked down numerous facilities and have been surprised by the number of blatant errors made by firms who have completed Arc Flash assessments.
These errors endanger the safety of employees working on electrical equipment as well as creating OSHA compliance risk for the facility.As Plant Managers, EH&S professionals or electrical engineers, you are responsible for selecting a capable firm to ensure electrical safety at your facilities. Have you ever wondered whether the firm you hired to complete your arc flash assessment is truly qualified? Don’t get me wrong, there are a lot of reputable firms out there with a ton of experience and passion to ensure accurate results. However, it is my true belief that many firms simply DO NOT understand what it takes to complete an arc flash assessment accurately. This concerns me and it should you too because let’s face it --we are dealing with the fragility of a human being. This is dangerous stuff! Most understand the extreme importance of these assessments, as they are a requirement of OSHA. Unfortunately, all too many people out there see this as an opportunity to “get on the band wagon” without a true understanding on how to properly utilize the tools for an accurate assessment. They lack the knowledge and experience.
The problem
Let’s put this in perspective. One of the main reasons we are completing these arc flash assessments is to get your facility in compliance with the OSHA mandate to provide electrical safety in the workplace for your personnel. But more importantly, we are identifying the “incident energy level” at the various pieces of electrical distribution equipment within your facility. Once we know this, we can then identify the proper level of personal protective equipment (PPE) a person needs to wear if performing live energized work on that particular equipment.
So, what is “incident energy”? In simplistic terms, incident energy is a measure of thermal energy at a working distance from an arc fault. The measurement is typically in calories/cm2. The working distance or the arc flash boundary (AFB), is the distance from where a worker stands to the flash location of which they would receive a second degree burn. A second degree burn produces 1.2 cal/cm2.
A second degree burn, although painful, will eventually heal. All the calculations for the arc flash assessment are based on the premise of a person avoiding a second degree burn or worse. Now that you understand what 1.2 cal/cm2 can do to you, just imagine what 40 cal/cm2 can do to the human body. A 40cal/cm2 arc flash event would cause excessive burns to the upper and lower parts of the body, the face and neck and in some cases (without the proper protection), death may result. 40 cal/cm2 has typically and historically been the threshold for the maximum allowable PPE. Although, the 2015 version of NFPA will allow higher levels as long as the manufacturers can produce higher levels of protection.
The Concern!
As I mentioned above, myself and my team have completed hundreds of assessments over the years including updates as required by NFPA 70E. When we complete an update, we are required to verify the existing study that was completed by XYZ Company and confirm the results. We do this by field verifying the existing one-line diagram for accuracy.
Here’s my concern: When I receive the existing information from our customer and I see this;
OR this;
You may say to yourself; “Ok, the arc flash label says that the arc flash boundary (AFB) is 5613 inches or 467.75 feet and the incident energy is 14787 cal/cm2.” Really?? In other words, you would need to be 467.75 feet from the equipment in order to AVOID receiving more than a second degree burn during an arc flash incident. If someone were to work on the equipment and cause an arc fault, 14787 cal/cm2 of energy would be released and essentially “vaporize” the building. Basically, this is so much energy, it’s unimaginable what it would do.
This in itself, makes the light bulb go off above my head. Something is wrong here. It’s virtually impossible for this much energy to be released. In other words, this assessment was done INCORRECTLY. The customer should question this immediately. It’s not uncommon for much of the front end electrical distribution equipment to have high levels of incident energy due to the contribution of available fault current coming from the utility company during an arc fault situation. Typically, these levels are less than 200 cal/cm2. Anything higher should be questioned. The vendor most likely had certain settings within the software program used improperly.
Why is this important?
Management and Safety Professionals should be cognizant of who they hire. Does the firm have a good reputation and the experience to be conducting an engineered arc flash assessment? How long have they been doing these studies? Do they have references? Are the people performing the assessment degreed electrical engineers? (Blog – Do I need a PE to perform an Arc Flash Study?)
Unfortunately, if you come across extremely high incident energy levels in your study, it’s likely that the information was calculated incorrectly. Now let’s look at what are the business and safety risks associated with an inaccurate study?
- The study is susceptible to an OSHA audit
- Personnel protected improperly
- High level sense of danger to personnel
- Costly equipment replacement. Plant engineering may decide to replace the equipment with arc rated equipment
- Insurance liability. Your insurance carrier may impose higher rates
- In reality, non-compliance to the 70E guideline
- PPE costs go up for higher levels of protection which may not be necessary
These are just some of the things to consider. If you feel you may be in this situation, I would love to hear from you and discuss it further.
About the Author
Scott King is the VP & National Director of Electrical Safety Services. Scott has been with Hallam-ICS for over 30 years. Scott and his team have been conducting power system studies for over 15 years.
Read My Hallam Story
About Hallam-ICS
Hallam-ICS is an engineering and automation company that designs MEP systems for facilities and plants, engineers control and automation solutions, and ensures safety and regulatory compliance through arc flash studies, commissioning, and validation. Our offices are located in Massachusetts, Connecticut, New York, Vermont and North Carolina and our projects take us world-wide.
You May Also Like
These Related Stories
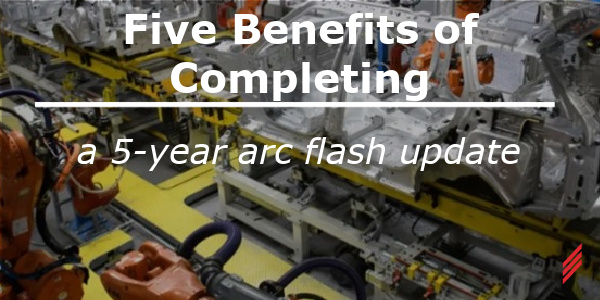
Five Benefits of Completing a 5-Year Arc Flash Update
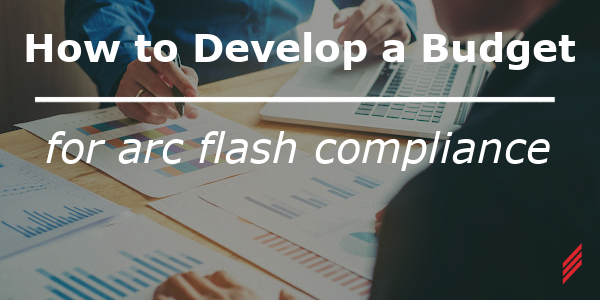
How to Develop a Budget for Arc Flash Compliance
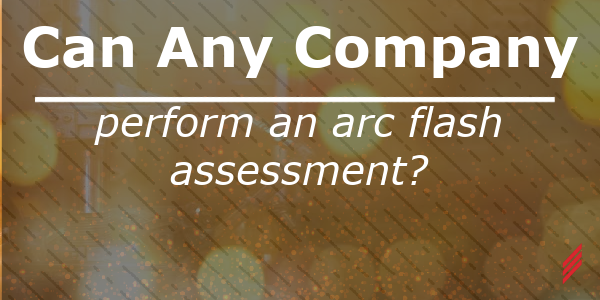
No Comments Yet
Let us know what you think