'Visible Data' – Seeing is Believing. A story from the Control System to the Board Room.
by Sam Lacasse on Nov 5, 2020 11:00:00 AM
IIoT, Cloud Computing, Cyber-Security and Virtualization are all topics that have been around for many years. Real momentum is being seen with smaller manufacturers with how control systems are implemented and how these systems are now an integral part of the business model.
At Hallam-ICS we have deployed many virtualized Process Control Systems (PCS). These systems are scalable from a large enterprise system to a small manufacturing facility. It is interesting to see the level of interest from operations, maintenance and management staff as they are introduced to the ‘Visible Data’.
Project Highlight I
We recently implemented a data historian project at a client’s site for a project that had not been approved previously due to budgeting. In this solution we used Rockwell Automation’s suite of products that included FactoryTalk View Studio, PlantPAX Faceplates and Add On Instructions, RSLinx Enterprise communicating with ControlLogix L73 Processors, Smart Motor Control Centers, FactoryTalk Historian and VantagePoint EMI. The Virtual Machine (VM) running VMware’s ESXi v6.0 containing the data historian was developed in our office, tested, copied to a USB Hard Drive and then installed on the production system. This eliminated the need for site development.
Once the site installation and testing were complete, I conducted a live training session for teams on ‘how to view your data’. Through the power of technology we sat in the production facility’s conference room and, upon completing several levels of authentication, we remoted in to the PCS Engineering Work Station (EWS) from the Enterprise Level system and proceeded to start the training session on a large screen Hi-Definition TV.
Within the first 30 minutes of training, the Plant Manager used the system to drill down into areas of the plant to see how things had been running. Much to his satisfaction, he found a few items with the plant’s operation that he suspected but never had the data to prove it. At that moment, I saw the light go on in their heads about how important this information will be for them to improve their processes. It was hard to curb their enthusiasm but there were many other details to cover over the course of the day. The remaining sessions went just as well. Everyone had that same ‘a-ha moment’. This was the first time in the course of this year long PCS install project that I was able to collaborate with every department within the organization. It was very satisfying to see how this system would help this organization grow and learn via this process information.
Now the infrastructure is in place to facilitate organizing and viewing this historical data through a web browser using dashboards, faceplates and trends all available on your device of choice. Here are a few screen shots that provide an example of this particular training session:
Figure 1 – Client is asking “Why is the Jacket Temperature (blue line) fluctuating after we fill the tank?”
Hallam-ICS response is “Well let’s add the Agitator Run Status to see if there is a correlation.”
Figure 2 – Depicts when the agitator cycled on/off the Jacket Temperature was affected.
This is just a small example of how this ‘Visible Data’ can promote interest within an organization. This particular food manufacturer has experienced massive growth over the past year. To sustain this growth, the people and the processes will need to embrace modern technology to achieve the highest quality, maximum efficiency and reduce or eliminate downtime.
Systems today, if designed correctly, are expected and sometime contractually obligated to have 99.999% uptime. Designing a control system for this level of uptime requires some planning. Every project will have a scope, schedule and a budget. That is just the reality of each project. It is our job to work within those constraints to design and implement the absolute best solution possible. Design considerations, from a controls perspective, should be:
- Fault tolerance - Hardware and/or software
- Hardware, software & licensing to support the fault tolerance solution
- Communications infrastructure i.e. ISA-95 model
- Power systems - Generators, Smart MCCs, etc.
- Field devices
Control systems have merged into the IT world. This merge requires significant coordination and training for all staff involved from the CEO to the operations staff and everyone in between. Training in my experience has ranged from introduction to Personal Computing 101, though this has been reduced over the past few years, to backing up your SQL database. It is very important to be sure the staff understands how to interact with these highly sophisticated systems.
In the event the end user is not yet able to support the technical aspect of the system Hallam-ICS offers support either through a remote support contract or onsite technical staff presence. This is a great way to promote a continual improvement plan to optimize system performance.
Project Highlight II
Another recent project used FactoryTalk View Studio, CompactLogix Process Automation Controller (PAC) and Flex I/O to control 10 curing ovens using the existing network infrastructure. We worked with the IT department to create a VLAN, installed an operator terminal with visualization software and configured secure remote access. This allowed the use of traditional computer trending and the removal of old paper & pen chart recorders. The control is consolidated and uniform and more importantly data is centralized for access to other applications to integrate detailed information of each customer’s order.
The original system used antiquated process controllers requiring an operator to program each individual oven separately for each temperature profile. Multiply this times 10 units and this is a bit of a task. It was sufficient for what they needed but some features were not available. One feature was that the recirculation fan would run continually even after a cycle was complete or an operator shut the fan off. This was a particular problem on the weekend where someone had to come in on a Saturday morning just to turn off the recirculation fan. The new system was able to develop standard temperature profiles in the form of recipes. Each oven could receive a template recipe with just a click of a button. Once the recipe was started the system logged all the process data electronically and would shut down the recirculation fan automatically after the cycle was complete.
This was a very small project but deployed concepts that would not have been applied just a few years ago. The client was very happy with the deployment time of 2 weeks, no irregular down time and being brought into the 21st century.
Summary
Most if not all of the systems that we deploy have in some aspect integration with IT, Building Management Systems (BMS), Security Access Systems, Remote Access/Support and smart network field devices. The way we do business has certainly been changed by the advancements and adoption of trends within the IT and Automation world. On a daily basis I develop on VMs, remote access into multiple client sites, Skype with colleagues and share content for troubleshooting or collaboration. We are able to do more in a shorter amount of time and benefit in so many ways. If some of these concepts seem to be unlikely to be integrated into your systems just wait a year or two they will get there.
It is both exciting and reassuring to see positive changes in our industry, and I look forward to the many opportunities in 2021 to be an agent of change for our clients and partners.
If you would like more information, please contact me at slacasse@Hallam-ICS.com or contact us via Help Desk.
About the author
Sam Lacasse is a Senior Process Controls Engineer for Hallam-ICS with 22 years of experience. Graduating from New England Institute of Technology 1993 with an A.S. Science Degree. He has extensive experience in Toxic Gas Monitoring, Food & Beverage, Robotics/Vision/Motion control and large scale Water/Wastewater applications.
Read My Hallam Story
About Hallam-ICS
Hallam-ICS is an engineering and automation company that designs MEP systems for facilities and plants, engineers control and automation solutions, and ensures safety and regulatory compliance through arc flash studies, commissioning, and validation. Our offices are located in Massachusetts, Connecticut, New York, Vermont and North Carolina and our projects take us world-wide.
You May Also Like
These Related Stories
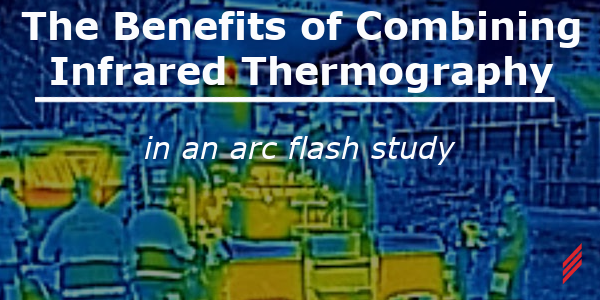
The Benefits of Combining Infrared Thermography with an Arc Flash Study
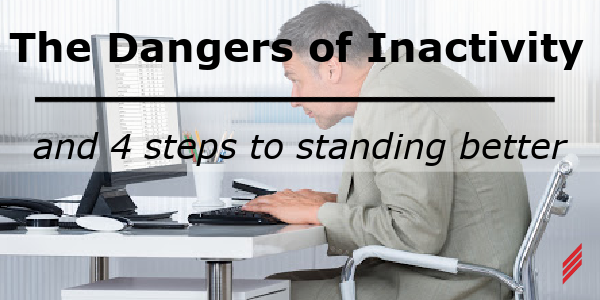
The Dangers of Inactivity and 4 Steps to Standing Better
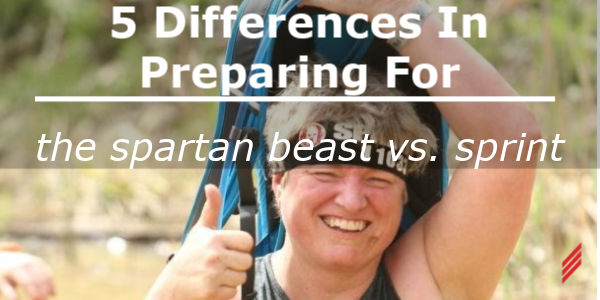
No Comments Yet
Let us know what you think