The Wrong Time to Find Out Your Arc Flash Study is Outdated…
by Jason Mazzola on Oct 21, 2021 10:30:00 AM
My name is Jason Mazzola and I am the Director of Electrical Safety at Hallam-ICS for Southern New England. I will be sharing my opinion on when I feel the worst time is to find out that your Arc Flash Study is either outdated or hasn’t been conducted at all. And, the worst time to find out that your systems protection coordination is incorrect or lacking. I will walk through two situations to support my feelings. One of them I have a personal connection to because it was an event that changed my opinion on electric safety and how fast things can change while preforming electric operations or maintenance.
Situation One “Protection Coordination”:
Ok, for this example let’s imagine that you are a manufacturer of a component for another supplier or product line. Things are rolling along smoothly as they mostly do every day; output is on target to meet customer demands and your customers are happily receiving their orders on time. One day a fault occurs in your electrical system. It could be anything from old or cut wires becoming exposed and making contact with ground or with each other, a bad contact decides to let go, or maybe a worker is careless and lets an energized wire make contact with a panel housing. Today, let’s say it’s a mouse escaping the winter cold, because in the world that I used to work in they were one of the main culprits for secondary (480v-120v) faults in our system. The mouse decides that it wants to build a nest and begins to chew on some of your cables, enough so to expose the conductor, ultimately resulting in a flash occurring in your electrical system.
In a properly coordinated system, the protective device that is next upstream from the fault position will clear the fault and prevent the fault from doing what it wants to do; make its way back to the source. If your system coordination is not correct (for example your relays aren’t set properly or your fuses/breakers are not sized appropriately), that fault has the ability propagate and make it all the way back to your main. The result is that the main opens up leaving you in the dark or running off of generation. The risk of extended damage to your system also goes up as that fault charges its way through your cables and other devices.
Now what are the consequences of this event? There are three big ones I see.
- First, you are going to incur costs related to inspecting your system for damage along with the repair costs associated with the findings.
- Second, we all want to provide the best service to our customers and as a best practice I always keep the end user in mind and whether or not any decision I make will result in something they need and want. In this case I am sure that the end user is going to suffer if the manufacturing of their goods is halted! Furthermore think of the chain of events that may take place as a result of one mouse’s decision to bite a wire within an inadequately protected system. Yes, your direct customers are going to feel the burden of a loss in their supply chain but ultimately that shortage is going to be passed along to their customers and possibly passed onto their customers’ customers and so on. The impact potential could be massive. Now go one step further and imagine if you are a hospital and the end user is a patient on life support!
- Finally, there will be a hit to your bottom line and in a world of cycle and takt times, you can bet that every lost minute has a dollar value and someone in your company is going to be losing sleep over it.
This same example can be applied to any facility doing work for any industry; think about your end user and what complication would arise if you couldn’t work at full capacity or had to stop working all together.
Situation Two “Arc Flash Study”:
Imagine a flash occurs while someone on your team is performing electrical work on your system and they aren’t in the correct personal protective equipment (PPE) for the incident energy that was produced during the event. I think it goes without saying how tragic this event could be and the results of it reach far outside of your company’s walls. I would like to share a story from my own experience. I worked for a major utility company for the better part of a decade, most of my time was spent supporting and working inside of substations ranging in primary voltages from 345Kv to 4Kv. By the very nature of that industry you are surrounded by hazards and forced to deal safely with them daily.
One day my colleague and I accompanied two of our substation maintenance workers into a substation to investigate a set of disconnects that had been arcing during a rain storm. The cause was quickly discovered and easily fixed so we thanked and joked with our guys about giving them an easy afternoon job, told them to go get lunch and the group had smiles on our faces as we made our way out of the yard. On the route to our exit we walked past a set of regulators and, as the last worker passed by, it failed for no obvious reason! The top was blown off spraying oil in every direction, shooting a fire ball straight up into the air. Covered in oil and a little scraped up from diving on trap rocks and jumping animal fences the lot of us was left shaken but luckily unharmed. We sent the employees home to shower and relax and we began making phone calls to have the event looked into.
Like so many electrical systems, whether it be in a 345Kv substation or a 480V facility’s electrical system, they age and change over time and what the available fault currents were on initial install may not be the same today. This is what was discovered during my incident. It was determined that no one should have been working on or within the arc flash boundary of those regulators without the 40 cal/cm2 suite on. As a result a massive study was conducted and many areas in our system had to be relabeled with updated PPE requirements. I can’t image the guilt if someone had gotten seriously injured or killed because of our lack in understanding about the safe work practices required in this instance. I took away from this experience a firm belief that Arc Flash studies and updates are 100% necessary and are worth every penny to have done. I learned to never assume that the level of protection I am wearing is going to be enough to save my life and I know now to never work on electrical apparatus that is not labeled with the proper Arc Flash Incident Energy level or PPE requirements. I ask that you be proactive with the protection and safety of your employees because the wrong time to find out what an events arc flash potential is after an event has occurred.
I hope these two situations highlight the necessity and advantages to you of having an Arc Flash Assessment or the 5-year updated done as well as having a review or your systems coordination conducted.
About the author
Jason Mazzola is the Director of Electrical Safety Services for Southern New England out of our Mansfield, MA office. He joined Hallam-ICS in 2019 and prior to that spent 10 years in utility industry in various engineering and leadership roles.
About Hallam-ICS
Hallam-ICS is an engineering and automation company that designs MEP systems for facilities and plants, engineers control and automation solutions, and ensures safety and regulatory compliance through arc flash studies, commissioning, and validation. Our offices are located in Massachusetts, Connecticut, New York, Vermont and North Carolina and our projects take us world-wide.
You May Also Like
These Related Stories
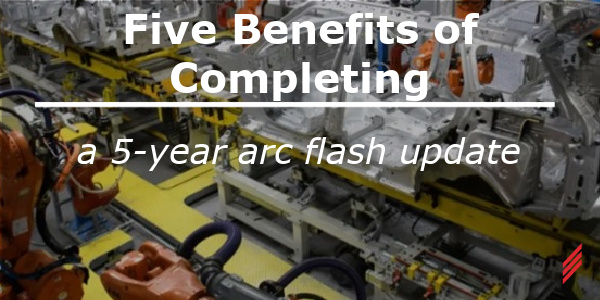
Five Benefits of Completing a 5-Year Arc Flash Update
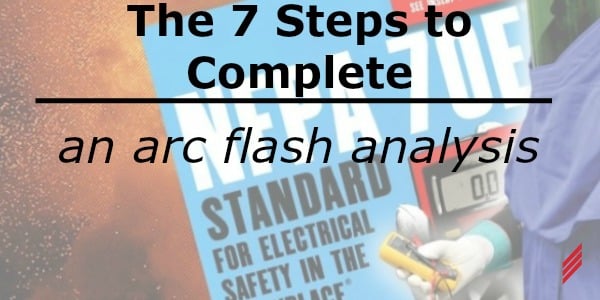
The 7 Steps to Complete an Arc Flash Analysis
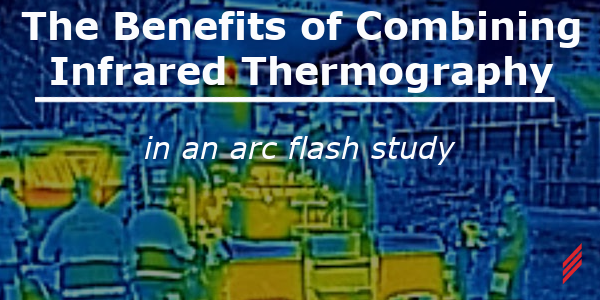
No Comments Yet
Let us know what you think