Management of Change Protocol for a Chemical or High Tech Facility
by John D. Cox, PE, CIH on Jan 2, 2020 10:22:00 AM
What is Management of Change (MOC)?
Management of Change, or MoC, is a best practice used to ensure that safety, health and environmental risks are controlled when an organization makes changes in their facilities, documentation, personnel, processes, experimental conditions or manufacturing operations. MoC is a formal protocol explicitly required by the Occupational Safety and Health Administration (OSHA) under its Process Safety Management (PSM) Standard and the US Environmental Protection Agency (EPA) in its Risk Management Plan requirements called out in the Clean Air Act Amendments, where thresholds of hazardous chemicals stored onsite are exceeded.
In this short blog I will briefly describe some of the most critical elements that must be incorporated into a MoC protocol to eliminate surprises when making various levels of changes in manufacturing or research operations.
The purpose of an effective “management of change” process and protocol is to eliminate uncontrolled change as a contributor to accidents, incidents, near misses or laboratory / manufacturing quality issues at a facility.
A well founded MoC process calls for all modifications to equipment, experimental procedures, hazardous materials and processing conditions other than an “identical change” and / or a “replacement in kind” change (see definitions given below) be thoroughly reviewed and authorized prior to implementation of the change. Minimum requirements for “management of change” include:
- establishing written procedures to manage proposed modifications;
- addressing the technical basis, impact on safety and health, modification to operating or experimental procedures, necessary time period for implementing changes, and authorizations required;
- informing and training affected employees; and
- updating process safety information and operating / experimental procedures or practices.
4 Types of Changes and Specific Examples
An Identical Change:
Is a replacement of an experimental procedure or manufacturing process with an identical procedure or one corrected for typographical errors, or incorporation of a change in a procedure that has been pre-approved and has no possible impact on environmental health and safety, quality or experimental / manufacturing issues, or the replacement of a tool, tool installation or experimental process set-up with the same manufacturer, model number, specification and materials of construction (See Appendix A for examples of Identical Change Types).
To implement an Identical Change, the following steps must be followed:
- A simple review by the person requesting the change and the person implementing the change must be done.
- No authorization of this change is required except that the supervisor of the person requesting the change should confirm that it is an identical substitution.
- The only documentation necessary for this type of change is to update preventive maintenance records or tracking documents, as appropriate.
Examples of an Identical Change include:
- Exact replacement of a valve or fitting;
- Replacement of a plugged pipe or tube with an identical pipe or tube;
- Retyping of procedures or instructions to correct spelling or grammar;
- Implement pre-approved transparent changes in PPE (e.g., go to the use of a new improved and approved [by EH&S] cartridge for an air filtering respirator)
A Replacement in Kind:
Is a replacement of an experimental procedure or manufacturing process with one that has been rewritten to more clearly define the same tasks, a change in a procedure that has been pre-approved and has little impact on other environmental health and safety, quality or research / manufacturing issues, or a replacement of a tool, tool installation or experimental process with different model numbers or manufacturers with the same specifications. In all cases, the implication of the change must be easy to understand (See Appendix A for examples of Replacement in Kind Types of Changes).
To implement a Replacement in Kind, the following steps must be followed:
- Conduct a formal (i.e., written) Risk Assessment depending upon the level and scale of change being proposed.
- The Department Manager or Supervisor affected by the change must approve it.
- A description of the change and the formal review Risk Assessment checklist and Preliminary Hazard Analysis (PHA) must be documented. This documentation must include any concerns that were raised during the risk assessment and describe how these issues were resolved.
Examples of a Replacement in Kind include:
- Replacement of a valve of fitting from a different manufacturer;
- Minor rewrites to experimental procedures that do not require a process change;
- Addition of a description of a chemical reaction to an experimental / process procedure; and
- Incorporation of a general recommendation for a change of PPE that is not transparent (e.g., adding a new requirement for a researcher or operator to don a face shield and chemically impervious sleeves before conducting a specific operation, which may have implications on dexterity, vision and potentially heat load on employee).
A Basic Change:
Is a change in an experimental procedure or manufacturing process which changes the chemistry, conditions, methods of operation, rate, equipment, or any other aspect of the actual experimental procedures including but not limited to any variation in size, type, order of additions, deletions or addition of new equipment.
To implement a Basic Change, the following steps must be followed:
- Conduct a formal (i.e., written) Risk Assessment depending upon the level and scale of change being proposed.
- The Department Manager or Supervisor affected by the change must approve it.
- A description of the change and the formal risk assessment must be documented. This documentation must include any concerns that were raised during the risk assessment and describe how these issues were resolved. Recommended corrective actions must be completed prior to implementing the change.
Examples of a Basic Change include:
- Change from a ball valve to a diaphragm valve;
- Minor changes in the order of addition of chemicals to an operation;
- Minor changes in chemical concentrations, temperatures, pressures or residence times for well-known chemical reactions outside of pre-approved operating windows;
- Small scale experiment involving a new process chemical or gas; and
- Rewrite of an experimental procedure or the development of a new policy or procedure generated in response to a risk assessment.
A New Process or Significant Process Change:
Includes any major new installation of an experimental process or manufacturing process change involving hazardous materials new to the facility or area impacted (See Appendix A for examples of a New Process).
To implement a New Process, the following steps must be followed:
- Conduct a formal (i.e., written) Risk Assessment.
- The Functional Vice President or his/her Designee affected by the change must approve it.
- The PHA, Job Safety Assessment (JSA), “What-If?” hazard analysis, Failure Mode Effects and Criticality Analysis (FMECA) or Hazards and Operability (HazOp) study must be documented and the follow-up action items be completed before the New Process is implemented.
Examples of a New Process include:
- Installation of a new tool or a large scale reaction vessel;
- Introduction of new and highly reactive process chemistry; and
- Fundamental process changes involving highly toxic, strongly oxidizing or pyrophoric process chemistry.
It should be noted that ineffective management of change is one of the leading causes of serious incidents. According to the U.S. Chemical Safety and Hazard Investigation Board (CSB), “In industry, as elsewhere, change often brings progress. But it can also increase risks that, if not properly managed, create conditions that may lead to injuries, property damage or even death.” Ineffective management of change is one of the major contributing factors in many of the incident investigations conducted by the CSB.
Potential Hazards:
In undertaking research experiments and processes in a chemical or high technology industry, personnel may be exposed to chemical, physical, biological and ergonomic hazards. Some of these specific hazards include, but are not limited to:
- Large Liquid Spill—Exposure to flammable, toxic, reactive, pyrophoric or corrosive chemicals;
- Hazardous Gas Generated;
- Fire or Explosion;
- Electric Shock;
- Sharp Edges or Pinch Points;
- Extreme Temperatures (hot and cold surfaces) -- thermal burns or frostbite from contact with cryogenic materials;
- Broken agitator shaft from thick slurries (loss of stirring);
- Glass breakage from pressure or vacuum;
- Projectile glass pieces from over pressurization of sealed vessel or chamber; and
- Variations in heating and cooling reaction vessels or other containers. Be aware that as volume of a process increases, cooling and heating capacity becomes less efficient due to surface area to volume ratio decreasing.
All Chemical facility and High Technology Researchers and Operators who will undertake experiments or processes at a facility must be trained in the value and necessity of a comprehensive Management of Change protocol. All written Risk Assessments conducted in support of a MoC activity must be retained in historical process records, which can then be used as the basis for all future changes.
About the author
John Cox is the founder of Advanced Technology Solutions, LLC located in Harvard, MA. He specializes in the development of value-added EHS management systems, industrial hygiene studies, prevention-based indoor air quality programs, health and safety training programs and facilitating product/process/equipment safety reviews. Mr. Cox has over 30 years of experience in the environment health and safety (EHS) field and has had considerable success in implementing proactive, prevention-based programs, accomplishing significant reductions in operating costs.
About Hallam-ICS
Hallam-ICS is an engineering and automation company that designs MEP systems for facilities and plants, engineers control and automation solutions, and ensures safety and regulatory compliance through arc flash studies, commissioning, and validation. Our offices are located in Massachusetts, Connecticut, New York, Vermont and North Carolina and our projects take us world-wide.
You May Also Like
These Related Stories
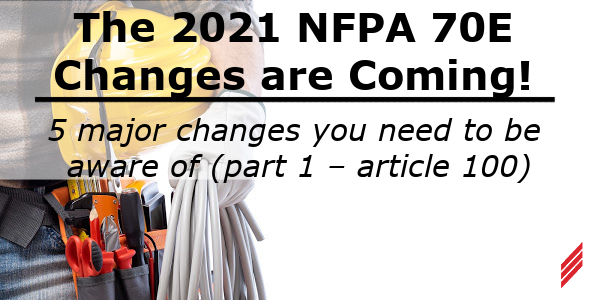
The 2021 NFPA 70E Changes are Coming! 5 Major Changes You Need to be Aware of (Part 1 – Article 100)
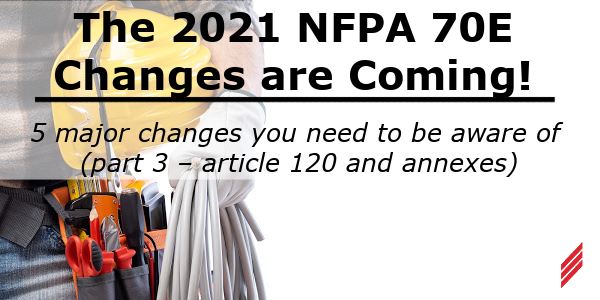
The 2021 NFPA 70E Changes are Coming! 5 Major Changes You Need to be Aware of (Part 3 – Article 120 and Annexes)
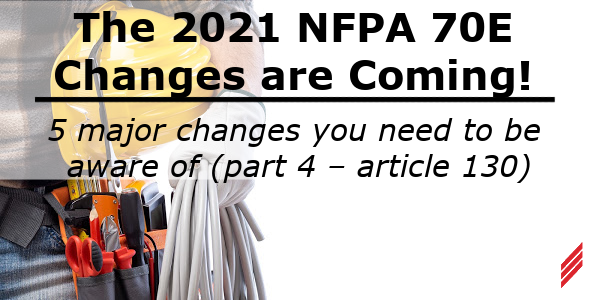
No Comments Yet
Let us know what you think