What is High Purity Piping? A Brief Look at ASME B31.3 Chapter X.
by Aaron Eicoff on Sep 2, 2021 10:30:00 AM
Are you involved in the design, operation, or ownership of process facilities, particularly in the biopharmaceutical or semiconductor spaces? Read on to learn more about ASME B31.3, Process Piping, with a focus on Chapter X, High Purity Piping, including different types of fluid services and code requirements. This series will go further in-depth with ASME BPE (BioProcess Equipment).
Process Piping is the topic of ASME B31.3 and covers many services found in a process facility such as chemicals, petroleum products, fluidized solids, refrigerants, cryogenic fluids, as well as gas, steam, water, and air. The tone of B31.3 is much different from that of a typical building, as defined in ASME B31.9, Building Services. With B31.9, the Owner is only burdened with the decision of selecting the code and B31.9 is the obvious choice.
The world of B31.3 is a bit different. The Owner is further burdened with specifying the requirements of each of the piping systems, whereas under B31.9 the design is generally the responsibility of the Engineer. Therefore, the Owner must take a bigger involvement, likely meaning a larger time commitment, in the design of B31.3 systems.
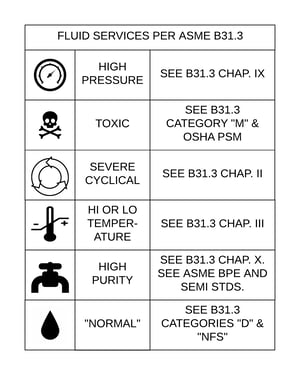
B31.3 classifies certain piping systems
based on danger to people and property.
Appendix M “Guide to Classifying Fluid Services” of B31.3 contains a wonderful flow chart for piping classification but is subject to copyright. I have created an abridged version here.
B31.3 contains numerous topics, and this series focuses on Chapter X, High Purity Piping, which was introduced in the early 2010’s. The semiconductor and biopharmaceutical industries had a need for cleanness and cleanability on a more demanding level than B31.3 had allowed. Representatives from both industries met extensively and developed Chapter X as a safety code while allowing for other industry-specific requirements in “extension” codes. Such codes include the SEMI E49 and the ASME BPE which will be further explored in this series. Although not based on Chapter X, the OSHA PSM refers to B31.3 and may required if the fluid service is toxic. The major classifications are based on temperature, pressure, toxicity, cyclical conditions, and purity. Some considerations for flammability exist, but they are sprinkled throughout the code. More than one classification can apply, but the design may become exponentially more difficult.
So, what is High Purity Piping? While there is no exact definition, high purity pipe generally produces a controlled level of “cleanness”. This requires alternative methods of fabrication, inspection, examination, and testing not covered elsewhere by B31.3. Common applications of Chapter X include high purity, ultra-high purity, hygienic, and aseptic piping systems. More specific bioprocess services such as Water for Injection (WFI), purified water (PW), and clean steam will be covered in a future article.
Some things to note about Chapter X include the extreme difficulty of combining high purity piping with high pressure piping. The code does not cover this intersection, and each component of the piping system would have to be calculated. On the other hand, combining high purity piping with toxic fluids is discussed in Part 11 of Chapter X.
Other requirements of the Chapter include those related to intermixing of components from different manufacturers which is permitted only when specified in the engineering design. Flanges, threaded joints, and other types of joining methods defined in the Code should be avoided whenever possible and may be prohibited altogether. Alternatively, hygienic clamps are a common sight in high purity systems due to their ability to provide a complete and even seal. Seemingly simple in construction, clamps must be installed with extreme care.
Examination and inspection of both equipment and piping installation are essential components of any mission-critical construction project. While similar in dictionary definitions, the terms take on distinctly different meanings under ASME B31.3. Examinations are generally self-checks done by the Contractor or Manufacturer whereas inspections are done by the Owner or their representative. Typical examinations include visual, physical, radiographical, and weld-coupon.
Inspections are an area where we, once again, see that B31.3 leans on the Owner by making the Owner responsible, through their Inspector, to ensure the system has been installed per Code and engineering design. In general, the inspector must rely on the examination and record-keeping procedures of both the Manufacturer and Contractor. There are four levels of inspector qualification which are defined in B31.3.
B31.3 allows for many different types of leak testing including hydrostatic, pneumatic, hydro-static pneumatic, sensitive, and alternative methods. All High Purity piping must be tested. The Code discusses the preferred methods for testing High Purity piping including special testing that minimizes the chance of contamination.
I hope you’ve found this article to be educational. Please reach out to Hallam for your Process Piping, High Purity Piping, and Bioprocess Piping needs. Questions and comments are encouraged and welcomed.
About the Author
Aaron has left Hallam-ICS to pursue other endeavors, but his contributions to the company continue to be valued.
About Hallam-ICS
Hallam-ICS is an engineering and automation company that designs MEP systems for facilities and plants, engineers control and automation solutions, and ensures safety and regulatory compliance through arc flash studies, commissioning, and validation. Our offices are located in Massachusetts, Connecticut, New York, Vermont and North Carolina and our projects take us world-wide.
You May Also Like
These Related Stories
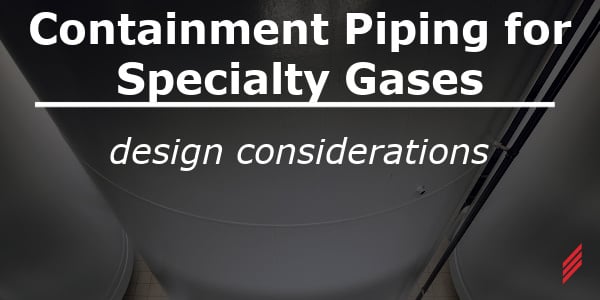
Containment Piping for Specialty Gases - Design Considerations
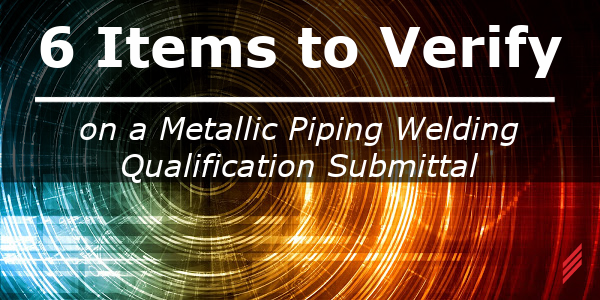
6 Items to Verify on a Metallic Piping Welding Qualification Submittal
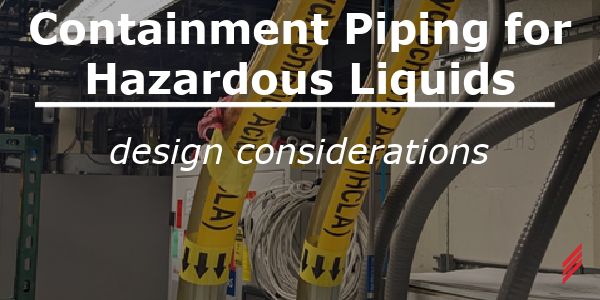
Comments (1)