6 Items to Verify on a Metallic Piping Welding Qualification Submittal
by William Neuburger on Apr 15, 2021 10:30:00 AM
This is the second part of a blog series on the Importance of Metallic Piping Welding Qualification Submittals. The first blog, Metallic Piping Welding Qualification Submittal Process-Definitions, focused on key terms and definitions.
In a perfect world, the engineer has a clear specification in the quality assurance section of their specification and the installer submits a current Procedure for the project which covers the materials, thicknesses, sizes and torch position for the project along with Procedure qualifications for each individual welder who will work on the project.
Rarely is our world perfect. Some unacceptable submittals we have seen include:
- Procedures for materials and sizes which do not cover the scope of the project's work
- Expired qualifications of individuals
- Qualifications for individuals which do not match the project's work
When we require resubmittals we hear "the welder has been doing this for 30 years" or "what we submitted was approved on the last project" or "why do we have to do this, we are leak testing everything." The specifications require a level of quality assurance and a competent installer should have current documentation of their process and their staff’s qualifications. An installer who is unwilling or unable to produce a satisfactory submittal is subtly sending a message to the owner.
When reviewing a submittal package, an engineer should check at least these 6 items
- Piping material matches the project scope
- Pipe sizes (diameters) and wall thicknesses (schedule) match the project scope
- Torch position matches the planned installation process (6G is usually preferred, though others can be acceptable based on the project)
- The submitted filler materials matches the Procedure’s requirements
- The welder’s Qualification references the Procedure (installers customarily provide a name and a numeric code for the Procedure)
- The welder’s qualification is current and won’t expire before the project’s end
Often the time to review, reject, resubmit and ultimately accept pipe welding submittals is far longer than the owner, construction manager, installer and engineer want. While there is no magic bullet to preventing a revise and resubmit situation, communication has a chance at addressing the issue. A few items we use when approaching pipe welding (these steps are useful for all submittals):
Have a clear specification for pipe welding and quality assurance
At the start of a project, make sure the contractor or sub-contractor responsible for pipe welding understands the specification - often a telephonic discussion is adequate. Also, it helps establish a human relationship between both parties which pays dividends beyond a submittal review.
When reviewing the submittal and something is lacking, contact the installer to discuss the issue before simply returning the submittal.
If you must return a submittal, provide specific, detailed notes describing the deficiencies.
Should you and the installer find yourself at an impasse, suggest the installer look at the issue from your eyes.
The weld submittal is important not only to confirm the installer is in compliance with the contract documents, it also is required for the weld inspection program on the project. A weld inspector in the field needs the submittal as part of her or his process to ensure the welder is following the procedure.
Sidebar on torch position
Torch position describes how the welder’s hands (and the torch) are oriented with respect to the pipe joint. The common positions for pipe welding are:
- 1R: horizontal pipe
- 2G: vertical pipe
- 6G: pipe at any angle, often tested at 45 degrees
Welding position graphic description from Baker’s Gas
About the Author
Bill has been a mechanical engineer since 1995 and with Hallam-ICS since 2010. His career has brought him to the top of the Transamerica Pyramid Center, chemical plants, underground mines, paper mills, and semiconductor fabrication facilities. He has experience designing, specifying and installing mechanical and electrical systems in the built environment covering industrial, institutional and commercial facilities.
Read My Hallam Story
About Hallam-ICS
Hallam-ICS is an engineering and automation company that designs MEP systems for facilities and plants, engineers control and automation solutions, and ensures safety and regulatory compliance through arc flash studies, commissioning, and validation. Our offices are located in Massachusetts, Connecticut, New York, Vermont and North Carolina and our projects take us world-wide.
You May Also Like
These Related Stories
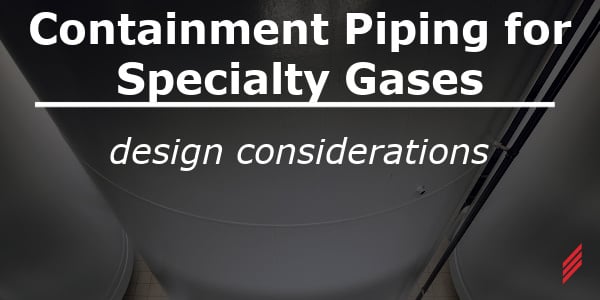
Containment Piping for Specialty Gases - Design Considerations
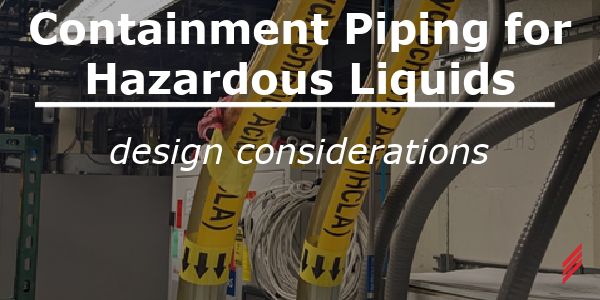
Containment Piping for Hazardous Liquids - Design Considerations
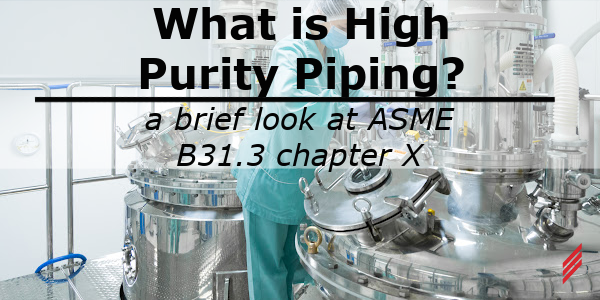
Comments (1)