Why Ongoing Commissioning is the Key to Long-Term Building Efficiency
by Matt Reed on Feb 3, 2025 1:16:00 PM
I was discussing Ongoing Commissioning (OCx) with a client and got asked the question: “I had Commissioning performed on my building during its construction, isn’t that enough?” “If they (the CxA on the project) did their job, I shouldn’t need anything else right?” The way I see it, NO. When commissioning is performed on a new construction project, or a renovation and/or retrofit project, that is a line in the sand. It’s a verification that the project met the Owner’s Project Requirements (OPR), the design intent, and was constructed per the approved design and construction documents. What that initial commissioning process cannot do is look into the future and perform an assessment of the buildings ongoing building performance. That’s where OCx comes in!
In the world of modern construction and facility management, maintaining optimal building performance is crucial. From reducing energy consumption to ensuring occupant comfort, OCx is an effective approach to achieving these goals. Unlike traditional commissioning, which is typically done at the end of a building’s construction, OCx is a continuous process that ensures systems remain efficient and perform as designed throughout the building’s life cycle. Let’s dive into what OCx is, how it is implemented, why it is important, and how it can benefit building owners and managers, with some real-world examples.
What is OCx?
OCx is the practice of continuously monitoring and adjusting a building’s systems and equipment to ensure they perform efficiently over time. This process involves regular assessments of how a building is being used, the HVAC (Heating, Ventilation, and Air Conditioning), lighting, plumbing, electrical, and other building systems to identify issues, rectify inefficiencies, and optimize overall performance. The idea is to proactively manage a building’s operations, rather than waiting for problems to arise.
Unlike traditional commissioning, OCx is a sustained process that continues throughout the building's life cycle. It involves a combination of real-time data monitoring, periodic inspections, adjustments to building systems, and staff training.
How Does OCx Work?
OCx typically involves the following steps:
- Building Usage Assessment
The first step in the OCx process should be to evaluate the building and its current use against the original OPR. Remember that the building was designed, constructed, and commissioned to meet the requirements of the OPR. If the building, or portions of it, is being used in a different way or for a different purpose the building systems should be re-evaluated to ensure that they are configured properly and are capable of maintaining those new requirements. Any easy example would be if the occupant load is significantly increased.
- Data Collection and Monitoring
The installation of sensors and monitoring equipment that gather data about the building’s performance in real time. This includes energy usage, HVAC system operation, lighting patterns, and other key metrics. This data is usually collected through building automation systems (BAS) or energy management platforms. The installation of these sensors and/or monitoring equipment ideally occurs during the initial construction or renovation/retrofit.
- Analysis and Reporting
The data collected is then analyzed to identify performance trends, inefficiencies, and potential issues. This can be accomplished using Analytic or Fault Detection and Diagnostic (FDD) software, or by your commissioning professional during a site visit. The advantage to the software is it is always running in the background performing that assessment. However, if this was not set up during the initial project or the initial installation and membership cost prices you out of that service, this can be performed by a person on an annual basis. Commissioning professionals can generate detailed reports that highlight areas of concern and opportunities for improvement.
- Adjustments and Optimization
Based on the analysis, building systems can be adjusted and optimized. This might include recalibrating sensors, adjusting HVAC settings, fixing faulty equipment, or reprogramming control systems. This process should be repeated at regular intervals to ensure continuous improvement.
- Training and Collaboration
Staff members, including facility managers, building operators, and maintenance teams, are trained to recognize performance issues and take corrective action as needed. Collaboration between owners, managers, and technical experts is crucial to the success of OCx.
- Continuous Feedback Loop
The process of OCx is continuous, creating a feedback loop where the performance of the building is always under review. This ensures that the building evolves with changing needs, technology, and energy standards.
Why is Ongoing Commissioning Important?
I read an article from the National Renewable Energy Laboratory where they referenced reports from the U.S. Energy Information Administration and the U.S. Environmental Protection Agency stating that buildings are the largest consumers of energy and one of the largest sources of greenhouse gas (GHG) emissions. Buildings in the United States account for about 70% of electricity use, about 40% of the total U.S. primary energy consumption, and about 30% of operational GHG emissions.
Building new energy efficient buildings, or renovating/retrofitting existing buildings is a great start to help reduce the negative environmental impacts, but OCx ensures that this contribution to the reduction of energy and GHG emissions is maintained throughout the life of that building, not just initially.
OCx can ensure:
- Long-Term Energy Efficiency
One of the most significant benefits of OCx is its ability to reduce energy consumption. As stated above, buildings are responsible for a large portion of global energy use, and inefficient building systems can contribute to excessive energy consumption. Through OCx, building owners can ensure that their energy management systems are always functioning at peak efficiency, reducing waste and lowering utility costs.
A study by the U.S. Department of Energy found that OCx could reduce energy consumption by up to 10-15% in existing buildings. This was seen in a case where an office building with a poorly performing HVAC system underwent OCx. Over time, the system's performance improved, saving the building owner significant energy costs.
- Long-Term Cost Savings
Maintaining optimal performance through OCx can lead to significant cost savings over time. By identifying and fixing issues early such as faulty sensors, inefficient equipment, or improper system settings, buildings can avoid expensive repairs and reduce operating costs. A well-commissioned building is more likely to operate smoothly, which also reduces the need for emergency maintenance and unscheduled downtime.
The Empire State Building in New York City is a prime example of the benefits of OCx. According to an RMI case study, after a major renovation, the building adopted OCx as part of its energy-efficiency strategy. This resulted in a 38% reduction in energy use, saving the building approximately $4.4 million annually.
- Enhanced Comfort and Health
Properly calibrated building systems lead to better indoor air quality, temperature control, and lighting, which directly affect occupant comfort and well-being. OCx helps ensure that HVAC systems provide consistent airflow and temperature regulation, which improves employee comfort and productivity.
- Sustainability Goals Are Met
Many organizations and governments are pushing for more sustainable building practices. OCx supports these initiatives by ensuring that buildings are performing at their best, reducing energy consumption, carbon emissions, and overall environmental impact. This is particularly important for buildings aiming for certifications such as Leadership in Energy and Environmental Design (LEED) or WELL Building Standard, which require consistent performance tracking.
- Longevity of Building Systems
Over time, building systems experience wear and tear, and performance can degrade. OCx helps prevent premature failure of key components by identifying and addressing issues before they lead to system breakdowns. As a result, building systems last longer, and building owners can delay costly replacements or upgrades.
OCx is an essential tool for building owners and facility managers seeking to optimize performance, reduce costs, enhance occupant comfort, and contribute to sustainability efforts. By integrating this continuous process into the day-to-day operation of a building, it is possible to ensure long-term operational efficiency and avoid costly problems down the road. As buildings evolve, OCx will continue to be a critical component in the drive for smarter, more sustainable buildings.
About the author
Matt is an experienced team leader with Hallam-ICS. He oversees all commissioning and validation projects and is responsible for the management and mentorship and the personnel within the Connecticut region
Read My Hallam Story
About Hallam-ICS
Hallam-ICS is an engineering and automation company that designs MEP systems for facilities and plants, engineers control and automation solutions, and ensures safety and regulatory compliance through arc flash studies, commissioning, and validation. Our offices are located in >Massachusetts, Connecticut, New York, Vermont, North Carolina, Texas, and Florida, and our projects take us world-wide.
You May Also Like
These Related Stories
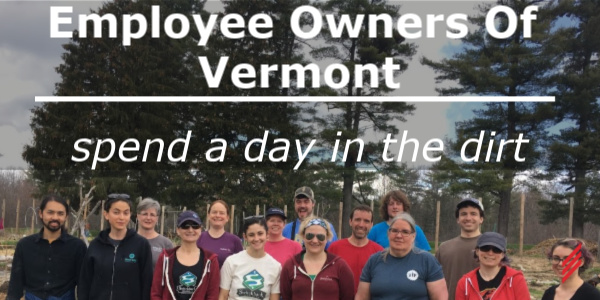
Employee Owners of Vermont spend a Day in the Dirt!
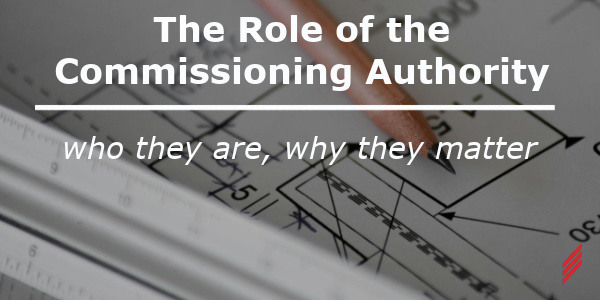
The Role of the Commissioning Authority: Who They Are, Why They Matter
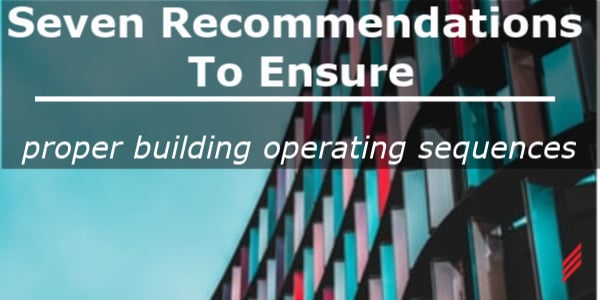
No Comments Yet
Let us know what you think