Why Temperature Calibrations Matter: Ensuring Precision and Safety
by Shane Hamlin on Oct 10, 2024 10:30:00 AM
As I dive deeper into these metrology blogs, I will focus on more specific types of calibrations and why it is important you keep your equipment in precise working condition. In this blog, let us discuss the importance of temperature calibration. Across any industry, temperature can be one of the most critical calibrations you do. As a calibrator, knowing the exact temperature is essential to having accurate measurements and proper working equipment. As temperatures change, other readings and instruments you are measuring can fluctuate which can ruin product quality, process efficiency, equipment reliability, and worst of all, can create safety hazards.
Since we all can relate to food, let us start with the food industry and how having an accurate temperature is crucial to success. Every degree counts in food service, but we often take it for granted that our food is safe. However, there are numerous ways food can spoil or become unsafe throughout the process. From proper storage of your food, whether freezing, refrigerating, or maintaining dry storage, ingredient temperatures need to be monitored to ensure the highest quality. During food preparations, maintaining the food’s temperature will prevent spoilage, and ensure food safety. Constantly checking temperature is essential to guarantee the food you serve is safe and delicious. Cooking temperatures is the key to making the perfect dish, but it is also key to making a safe dish. Equally important is storage of cooked foods and proper cooling procedures. This is why it is essential to use accurate equipment monitor, prepare, cook, and store food. Without accurately calibrated equipment, the safety of your guests is only one malfunctioning thermometer away. Additionally, it is important to adhere to the guidelines from the Department of Health (DoH), ServSafe, and the US Food and Drug Administration (FDA) to ensure food safety and avoid being shut down.
We started with food, to get you thinking about everyday temperatures. Now, let us consider a more critical industry, biotech. This is where our medicines, vaccines, and cures originate. In biotech, precision is not an option, with a tolerance of 0.1⁰ Celsius or less, the demand for accurate equipment is paramount. This means that the precision of the equipment needs to be tested more often and with the highest of standards. If an incubator holding a virus or cure is the wrong temperature, then the samples may become nonviable leading to wasted resources and costly delays. If a lab’s temperature is off, the research findings can be inaccurate, compromising the integrity of the entire study. If a freezers’ temperature changes for too long, then viruses, medicines, and other sample vials can spoil, leading to the possible destruction of valuable research. Freezers, fridges, storage areas, and labs must all maintain precise temperatures. Ensuring accurate temperatures is crucial to safe and cost-effective research. And Biotech facilities must adhere to safety and quality regulations put forth by the FDA. These guidelines and regulations have been put into place to protect everyone’s safety and maintain operational compliance.
Somewhere between everyday food service and high-level biotech research lies calibration of industrial equipment. This encompasses a wide range of equipment and varying levels of importance depending on the product. Most products require accurate temperatures for successfully manufacturing. Whether it is a plastic that needs to be heated just right for proper molding or metal that needs to be tempered to the correct temperature, accurate temperature control is crucial for industrial businesses. Proper temperature measurements ensure operational efficiency and staff safety. If a furnace overheats, it can destroy products and create safety hazards for the employees. If the temperature in your quality control lab is inconsistent, testing your products will give you inconsistent results. An inaccurate temperature reading with an HVAC system can cause a domino effect, resulting in production issues, recalls, and equipment damage. Regular calibrations are essential to maintain the integrity of temperature systems and equipment, supporting product quality, equipment reliability, operational efficiency, and overall safety.
Let's face it, temperature is a critical factor in all types of businesses. We have discussed several key reasons for calibrating temperature, so let us recap.
Accuracy and Reliability: Calibrated temperature equipment ensures precise readings, which are essential for quality control, safety, and regulatory compliance across various industries.
Process Efficiency: Accurate temperature measurements help optimize production, reduce energy consumption, improve quality, minimize waste, and can enhance the lifespan of your equipment.
Regulatory Compliance: This keeps us honest, adhering to calibration standards is crucial for meeting safety and quality regulations in most industries. These regulatory requirements are outlined by various organizations and following them is important for success.
Cost Savings: Calibrated equipment minimizes the risk of costly errors, product recalls, and equipment damage due to incorrect temperature readings.
Safety: The most important reason. Accurate temperature readings prevent issues that can affect people’s health and physical safety. Everyone’s goal should be to create a safe and healthy work environment for all their employees.
Inaccurate temperatures can compromise product quality, lead to process inefficiencies, and create safety hazards. This is an outcome that no company wants. As a calibrator, it is important to know how to do help your business succeed. Partnering with Hallam-ICS can ensure your business follows regulatory guidelines and fosters a better workplace for your employees. While temperature calibration is one of our metrology services, it is only the beginning of what we can offer you.
About the Author
From his diverse work experiences to his current role with Hallam-ICS, Shane has learned the critical importance of not just having the right tools but properly calibrated tools to get a job done right. Having worked across various industries has given him a unique perspective on the importance of precision. In this blog, he will show that no matter what profession you work in, the difference between a job done and a job done well stems from the calibrations of your tools.
Read My Hallam Story
About Hallam-ICS
Hallam-ICS is an engineering and automation company that designs MEP systems for facilities and plants, engineers control and automation solutions, and ensures safety and regulatory compliance through arc flash studies, commissioning, and validation. Our offices are located in Massachusetts, Connecticut, New York, Vermont, North Carolina , and Texas and our projects take us world-wide.
You May Also Like
These Related Stories
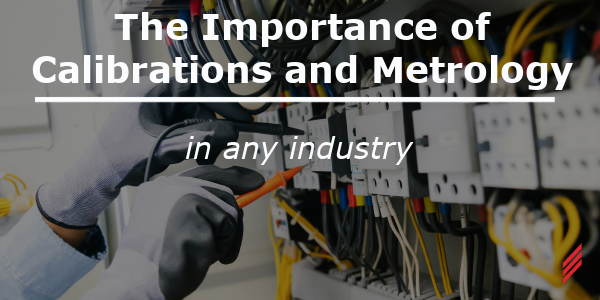
The Importance of Calibrations and Metrology in Any Industry
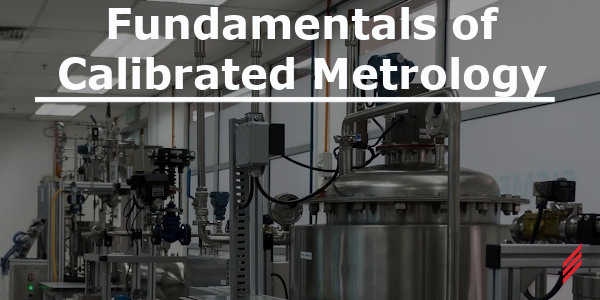
Fundamentals of Calibrated Metrology
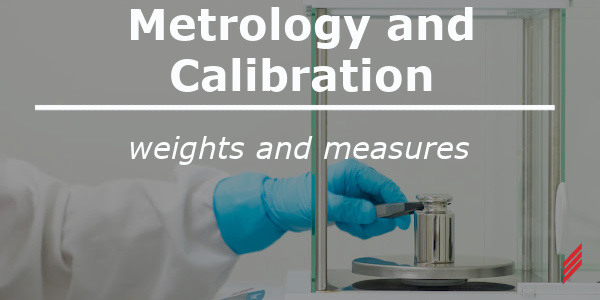
No Comments Yet
Let us know what you think