Autoclave Adventures-Navigating Qualification for a Sterile Future
by Bill Deyncourt on Aug 3, 2023 10:30:00 AM
One of the most commonly used pieces of equipment in primarily healthcare, pharmaceutical, and laboratory settings is the Autoclave or Steam Sterilizer. For compliance, quality and safety concerns these autoclaves must be qualified to sterilize equipment and materials with high-pressure saturated steam. Qualifying an autoclave refers to the process of validation and assuring that the autoclave is meeting the requirements as set for its use.
Defining the User Requirements is the beginning step of the qualification process. This is where the intended use and requirements for the autoclave will be defined. These include identification of what will be sterilized and the required parameters such as temperature, pressure, and exposure time. The next step is the Design Qualification phase. During this phase the autoclave specifications and design are assessed by reviewing the manufacturer provided information. This helps to verify that the autoclave is appropriate for its intended use and meets all the necessary design standards as stated in the User Requirements.
Installation Qualification (IQ)
The Installation Qualification (IQ) phase ensures the autoclave has been installed correctly and meets all the requirements determined during the design phase. Calibration of the sensors and instruments used to ensure accuracy and control of critical steps are confirmed. Verification of utility systems such as steam, water, and power occur during this step.
Qualification (OQ)
The next phase, Operational Qualification (OQ), is when the autoclave is tested to confirm that it is functioning as normal and within the desired parameters. Test cycles with representative or simulated loads are performed, monitored, and recorded to ensure temperature, pressure, and exposure are operating as required and within limits.
Performance Qualification (PQ)
The last phase of the validation process is the Performance Qualification (PQ) where the autoclave’s performance is tested under normal operating conditions. This can include conducting multiple sterilization cycles with maximum and minimum loads and monitoring the critical parameters. The results from these runs are compared with the determined acceptance criteria to ensure the desired sterilization results.
Re-qualification and ongoing maintenance are required to be planned once the autoclave is qualified. Routine maintenance, calibration, and critical component monitoring are necessary. This will ensure that the autoclave will continue to perform as required and ensures reliable and consistent operation.
During a recent qualification of an autoclave, I found my experience as an equipment operator to be a valuable resource. A vacuum leak test is a critical step performed on autoclaves to verify the integrity of the autoclave's sealing system and ensure that it can maintain the required vacuum pressure during sterilization cycles. Following a successful Site Acceptance Test, Hallam-ICS was engaged to perform the qualification of a new laboratory sterilizer for use by a large manufacturing site. In the qualification process, I noticed that the Vacuum Leak Test was taking almost all the time allowed to hit the set point. But since the chamber pressure met the set point within the test’s allowed time limits it was considered successful. My real-world experience using autoclaves in a manufacturing environment alerted me that something was not right, even after a successful leak test. My reasoning was that a chamber with a good seal and full integrity should have been able to pull a vacuum much quicker than that. After relaying this information to site maintenance, a thorough check of all connections was performed and the original equipment manufacturer was contacted and brought in to re-inspect the equipment. It was determined during this inspection that the vacuum pump had been installed backwards at the factory.
The vacuum pump is a critical component on an autoclave with regards to its sterilization capabilities. Backwards installation creates inefficient vacuum generation. Being installed backwards, the reversed pump was pushing air into the chamber instead of creating the expected negative pressure necessary. Ergo, the autoclave fails to effectively remove air and moisture, which are essential for successful sterilization. The pump installed backwards now introduces the risk of contamination of dust, particles, or microbes. The presence of contaminants can affect the elimination of pathogens, leading to incomplete or ineffective sterilization. The autoclave becomes unreliable and poses a significant risk to patient safety despite passing an initial qualification. Autoclaves are equipped with safety features and interlocks to ensure safe functioning for the operators. However, installing the vacuum pump backward can bypass these safety mechanisms. By circumventing these safeguards, the autoclave becomes vulnerable to potential hazards, including pressure buildup, overloading of components, or malfunctions that could endanger people and or the surrounding environment. The safety of personnel and compliance with regulatory standards are in fact jeopardized when a vacuum pump has been incorrectly installed.
My experience helped us to recognize that there was a potential issue and further investigation was required. Inefficient vacuum generation, reduced sterilization efficacy, equipment damage, and safety risks are among the prominent issues that arise from such an installation. To maintain the autoclave's performance, reliability, and the well-being of those relying on it, strict adherence to manufacturer guidelines and proper installation practices are imperative. The Commissioning, Qualification, and Validation team within Hallam-ICS combines qualification knowledge with real world industry experience to meet all your qualification needs.
About the Author
Bill joined our Apex, NC office as a Commissioning and Validation Associate in 2022. A graduate of East Carolina University, Bill has over 7 years of experience in manufacturing environments. As a member of the Commissioning Team, Bill works alongside the commissioning, qualifications, and validation team on multi-disciplined commissioning/qualification/validation projects in the region.
Read My Hallam Story
About Hallam-ICS
Hallam-ICS is an engineering and automation company that designs MEP systems for facilities and plants, engineers control and automation solutions, and ensures safety and regulatory compliance through arc flash studies, commissioning, and validation. Our offices are located in Massachusetts, Connecticut, New York, Vermont, North Carolina Texas and Florida and our projects take us world-wide.
You May Also Like
These Related Stories
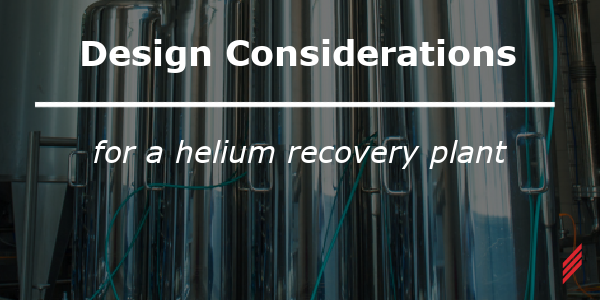
Design Considerations for a Helium Recovery Plant
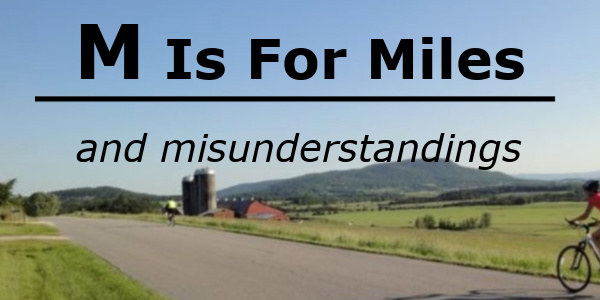
M is for Miles and Misunderstandings
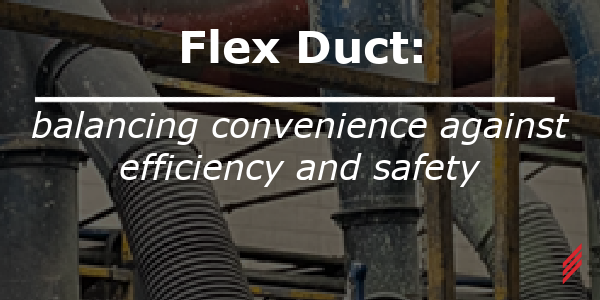
No Comments Yet
Let us know what you think