This Is The Year Of Retro-Commissioning. Here’s why!
by Keith Sheldon on Jan 23, 2018 10:00:00 AM
There are many buildings out there that were built in the 1980’s, 1990’s and early 2000’s that are now approaching thirty to forty years old and are still in perfect working operation, or are they? What’s old is now new again, right? Maybe in some cases, but I don’t know too many people that are still wearing jean jackets, listening to walkmans and sleeping on waterbeds these days. That being said, in the world of facility management there are plenty of old jean jackets, walkmans and waterbeds that are still in operation in these buildings that we all work in or on every day.
Unlike those luxury items of our past, these aging buildings are very much still being used, and are being counted on for many more years to come, which brings up some relevant questions, such as are they still in proper working order? Have they been adequately maintained and are they still efficient as the day they were built? Sure you can still wear that jean jacket and sleep on that waterbed each night, but your appearance alone will cause people to make many unfair assumptions of your physical wellbeing not to mention the stiff necks and bad backs you will be waking up to more mornings than not.
l have walked into many of those old hidden away mechanical rooms, where there is dust as old as I am, yet the equipment keeps running and humming away with most of the building occupants not even knowing that room exists. Filters have never been changed or don’t even exist; dampers and valves are locked open just to keep the equipment running. That being said, even the best maintained buildings could probably use a tune up too. Just like those old mechanical rooms, today’s world of building automation systems can make it even easier to lock those items in place and to keep the building running without even going into the mechanical room.
Retro commissioning doesn’t always mean your building is old, some of the newer buildings built in the last few years, might be hiding even bigger issues, without anyone even realizing it yet. Change of seasons can be torture on a not well maintained building new or old. How many times have valves been commanded open or overridden just to satisfy a short term request of being too cold or too hot? Once that has taken place, all those fancy sequences that the engineers have developed to keep the systems running efficiently are now thrown right out the window. Suddenly a new building is operating as inefficiently as the old building that was never maintained. Either way you look at it, I am willing to bet you will find that most of these buildings are not running as they were designed and intended to be.
There are many reasons why retro commissioning isn’t performed as frequently as it should be. The most common reasons are that there isn’t enough money budgeted for this activity, because it is already being spent elsewhere on newer buildings or equipment, or has been budgeted for replacements of failing equipment that may have been prevented if properly diagnosed earlier. The overall scope of the retro commissioning can be a daunting task for sure. Start by looking into one or two building systems each year, and perform a full system tune up, dig out those old drawings, revisit the sequence of operations and O&M manuals, and look at your alarm history. You may find that what you thought was failing, has just been running incorrectly or not per the intended sequence of operation for these last couple of years. These quick fixes or Band-Aids that were applied in the middle of the night, just to get the system back up and running, have been forgotten and are causing issues all over your building. As a facility manager, if you can narrow your retro commissioning scope down to what has been causing the most heartburn recently or the most heartache over the years, you will be better positioned to take on more and more retro commissioning projects as time goes on.
If we knew then what we know now, we could change everything, and who’s to say we can’t jump back into the DeLorean time machine and punch up a previous date in time, and go “Back to the Future”, and revisit some of our old friends from our commissioning projects of years past. Maybe we can right some of those wrongs that were done either in design or in the years of maintenance that followed and prolong the equipment and buildings future. On our travels back to simpler times we may discover that there are also many oldies but goodies out there that could be brought back into style as well. There are plenty of old technologies and methods that are working just great, and in those cases, we should maybe dust off the old waterbed, fill it up with some new water, check for any leaks and then precede to get a great night’s sleep for many years to come.
As we begin this new year of new, fancy, state of the art commissioning projects, our commissioning team is also going to be reaching out to some of our old friends from our previous projects. We will be checking in to see what’s working well and what has already been replaced and the reason why. Taking that all in, we may be able to share some of our recent successes, and work with our old friends to help them rediscover the glory days of their buildings past.
About the Author
Keith Sheldon is the Commissioning Manager for Hallam-ICS. Keith started his Hallam career in the Hallam-ICS Vermont office and now works out of both the Hallam-ICS Massachusetts and Connecticut offices. Keith has a Bachelor’s of Science degree in Engineering and Management from Clarkson University, and holds a certificate in project management from Worchester Polytechnic Institute. Keith is a member of the ISPE International Society of Pharmaceutical Engineers, and has performed commissioning and qualification projects in the pharmaceutical industry for over 15 years.
Read My Hallam Story
About Hallam-ICS
Hallam-ICS is an engineering and automation company that designs MEP systems for facilities and plants, engineers control and automation solutions, and ensures safety and regulatory compliance through arc flash studies, commissioning, and validation. Our offices are located in Massachusetts, Connecticut, New York, Vermont and North Carolina and our projects take us world-wide.
You May Also Like
These Related Stories
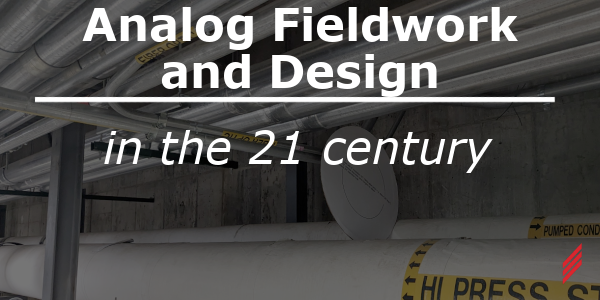
Analog Fieldwork and Design in the 21 Century
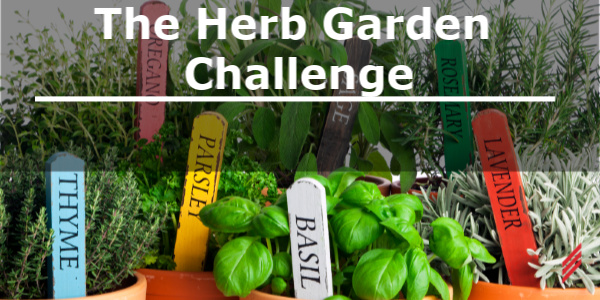
The Herb Garden Challenge
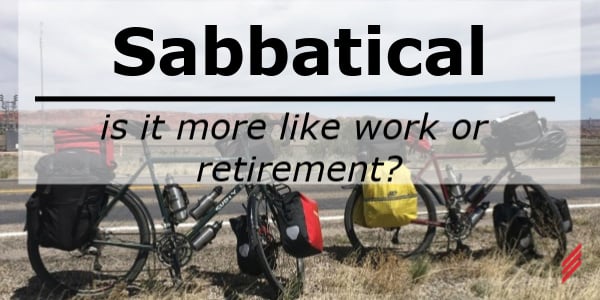
No Comments Yet
Let us know what you think