Confessions of a Control Engineer: Sometimes PID is Just Wrong
by Ray Racine on Jul 2, 2020 10:30:00 AM
We’ve all seen it. You have a process that seems to defy your best attempts to control it. Many times, it is because PID control is just the wrong way to go for your loop. This short blog addresses the loops that by the time you tune them to where they aren’t chasing themselves, they respond so slowly that they take forever to recover from a process upset.This blog addresses processes with dead time. All loops have some process lag to them. When I make an output change, the process value does not simply jump to a new steady state value. Plotted Control Output & Process Value vs time will usually look something like this:
Most Flow Loops, Pressure Loops, Temperature Loops will behave in a manner similar to above.
Do I have dead time in my control loop? The easiest way to tell is to put your PID loop in manual for a few minutes and let it settle out wherever it settles out. Now make a 5% change (if your process allows) to the output and start counting. If your process does not even start to change for more than 30 seconds, then you have dead time.
Now, not all loops with Dead Time are a problem for PID control. If you are heating up a 2000 gallon reactor, there may be some dead time (on the order of a minute or two), but the process also takes a very long time to level out (on the order of tens of minutes). This is a big, slow loop; and PID control will work quite nicely, once you properly tune it. The plot below shows a loop with some dead time, and a lot of process inertia (or Lag) and demonstrates a loop like our 2000 gallon reactor. No amount of control will make this loop faster than it actually is.
So when does Dead Time lead to bad control? Dead Time in your loop leads to bad control whenever the Dead Time is the dominant reason for slow response.
I recently had a client that produces a granular product. In order to keep dust down, they spray the product with a water-based solution. The product travels a fairly long way on a conveyor belt, before they measure the average moisture content. They can’t move the sensor closer to the spray for processing reasons. Too low of a moisture reading and bad product quality is the result. Too high of a moisture reading and they make a slurry that plugs the process. If we put the PID in manual and make a change to the spray, it takes almost two minutes before we see any change in the process; but once it starts to change, it levels out pretty fast. They tried to use the PID controller in the drive for this system; but never got good results. They ended up with a speed pot on the drive and operators making changes (among all of their other responsibilities) when they saw the process getting out of control. Many times, the system plugged up due to high moisture, or they were producing dry – out of spec. – product.
This is the perfect place to ditch your PID, and address the loop with a proper Dead Time control strategy. At Hallam-ICS our Control Engineers aren’t just programmers. They understand process. If you have Dead Time issues or any other control challenges, please give our Control Professionals a shot at improving your process.
About the author
Ray has retired from Hallam-ICS, but his contributions to the company continue to be valued.
Read My Hallam Story
About Hallam-ICS
Hallam-ICS is an engineering and automation company that designs MEP systems for facilities and plants, engineers control and automation solutions, and ensures safety and regulatory compliance through arc flash studies, commissioning, and validation. Our offices are located in Massachusetts, Connecticut, New York, Vermont and North Carolina and our projects take us world-wide.
You May Also Like
These Related Stories
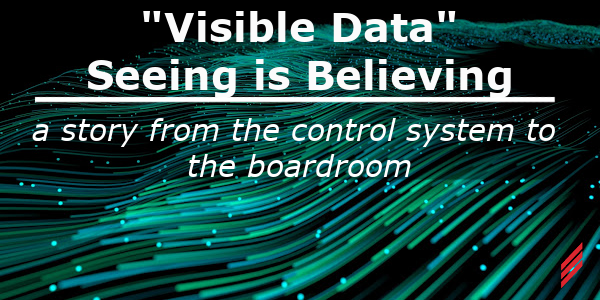
'Visible Data' – Seeing is Believing. A story from the Control System to the Board Room.
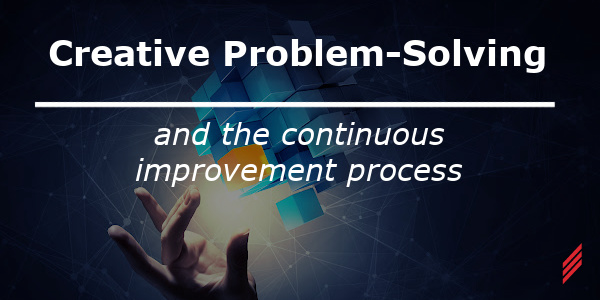
Creative Problem-Solving and the Continuous Improvement Process
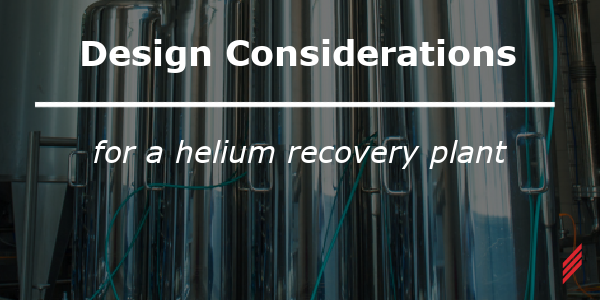
No Comments Yet
Let us know what you think