The 4 Steps of an Instrumentation Project Plan
by Pete Niarchos on Sep 21, 2021 10:30:00 AM
An experienced Main Instrumentation Vendor (MIV) knows the importance of establishing an effective project plan prior to beginning work (the old saying measure twice, cut once comes to mind).
While each project has unique elements, there are typically 4 steps to every successful MIV project plan.
Additional blogs in this series:
The Benefits of Using an Independent Main Instrument Vendor
How To Choose The Best Main Instrument Vendor For Your Project
Step 1 - Select an Experienced Team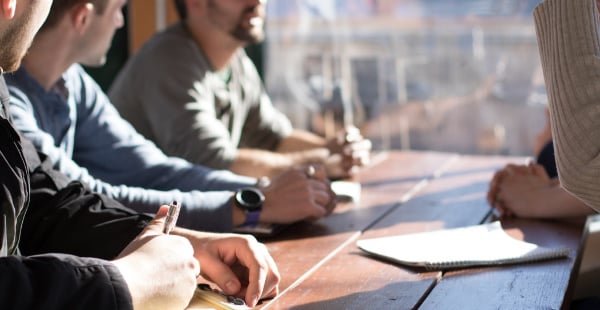
The foundation of a successful project is the formulation of the proper team. In selecting a team, the MIV will need to consider the size and scope of the project, the industry served, schedule, location, and relationships with the client, general contractor and subcontractors. At minimum, the following key positions will need to be filled:
- Project Manager: The right project manager should not only have specific industry experience but understand the execution of large I&C projects and have experience working with electrical and mechanical subcontractors.
- Procurement Manager: This person should have strong relationships with the supply chain in order to manage deliveries and returns (inevitable), leverage pricing and source multiple/alternative material suppliers if needed to maintain project costs and schedule.
- Field Superintendent: Similar to the project manager, this person should have a strong understanding of construction projects and a track record of establishing good working relationships with the general contractor and subcontractors, with whom they will work on a daily basis. A solid instrumentation and controls background is essential.
- Lead Instrumentation Technician: This role should be filled by a good communicator who has extensive instrument installation, troubleshooting, configuration and calibration experience. This person, and other I&C Technicians (as needed), will be the “boots on the ground” working closely with the installation subcontractors, client metrology team and systems integrator to collaboratively execute the project.
- Instrumentation Engineer: As needed, this person will help the client and/or engineering firm of record with selecting, or confirming, the appropriate instrumentation and valves for the application.
Step 2 - Set Expectations
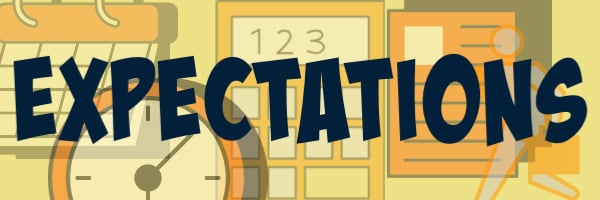
To ensure that the project runs smoothly it is important to engage all of the project stakeholders (i.e. construction manager, engineering firm, electrical / mechanical subcontractors, and the client’s engineering, validation and operations teams) at the project onset to establish the milestone, logistical, and documentation requirements. With the end in mind, the important tasks at this stage of the project include:
- Establish Key Milestone Dates: A given for any successful project.
- Establish Roles and Responsibilities: Many stakeholders mean opportunities for gaps in scope.
- Determine Material Storage Locations(s): For ease of logistics, on-site material storage is preferred but may be difficult given the potential volume of devices and construction activities. Two locations may be required: one location for instrument processing / testing and one for staging / release to the installation contractors.
- Agree upon required SOPs & Training: Determine what SOPs and training is required for the project and train the team as soon as possible.
- Establish ETOP Requirements: Establishing the documentation requirements with regard to both the content and deliverable format is an important as any installation task, especially for the Life Sciences industry. This is often overlooked at the beginning of the project resulting in lost time and money due to returns, expediting and rework of the turnover package. Anybody who has failed to order a Material Traceability Report or Certificate of Calibration after a device has been delivered knows the pain of not being organized up front.
Step 3 – Mobilize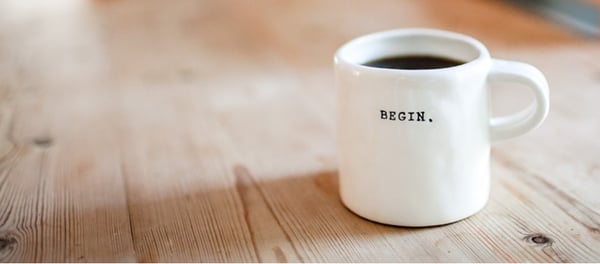
Let’s get started! The next order of business is getting mobilized to execute. That means doing the following:
- Engage the Design Organization and review specifications: The MIV should be a partner and extension of the design firm who has specified the instruments and valves. There will be errors and changes! A knowledgeable MIV can review the specifications, identify errors, provide feedback before issues arise, and offer alternative solutions if needed.
- Populate a Metrology Database with instrumentation data & prepare ETOP “shell”: It’s all about the data! At project start, the MIV needs build the infrastructure to be able to track, report and compile the pertinent instrument documents (certificates, MTRs, drawings, manuals) easily and effectively. The client and installation team needs to know at any given moment the status of an instrument or valve. This is the time to populate your instrument management software / database with all of the instrument and valve specification data so that you hit the ground running.
- Customize Forms, as needed. Material Inspection, Bench Test and Calibration forms should reviewed with the client and modified as needed.
- Prepare space (on-site and off-site): As mentioned, you will want ample and secured space to process and store the materials prior to the first order.
- Engage Supply Chain: Before ordering, expectations about order volume, delivery deadlines, delivery status reporting, shipping & handling, and ETOP documentation requirements should be set with the instrumentation and valve suppliers. Establishing a direct communication line with the equipment manufacturers is also beneficial to ensure expeditious deliveries, returns and / or repairs.
- Calibrate Your Standards: To kick off the project, calibration standards should be freshly calibrated by a NIST laboratory. You want to know that your standards are in good working order and not in the middle of a calibration cycle.
Step 4 – Execute the Plan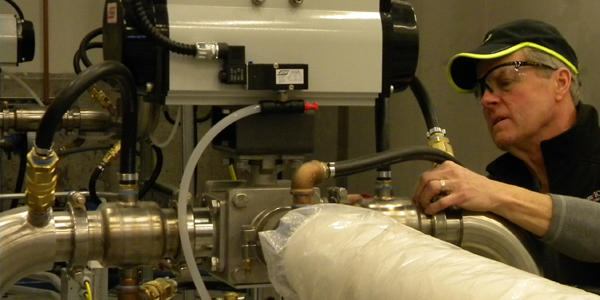
If the early preparatory steps listed above are followed, the ordering and processing of the instruments and valves should flow easily. There will be damaged materials, incomplete documentation, errors in the manufacturer of parts, and late deliveries. But if you have the infrastructure in place, the identification of problems, and recovery from them, will be quicker and easier to manage. It’s time to execute the meat of the process:
- Submit Instrument Information for Record: Time is always of the essence. As mentioned above, the MIV should engage the Engineering Firm early in the project and review the specifications in detail. Specification errors found by the MIV can be communicated directly to the Engineering Firm to address promptly. Then the Instrument Information can be Submitted for Record to avoid a potentially lengthy and iterative review process.
- Implement MIV Process: Depending on the project scope of work, the MIV process will entail some or all the following tasks:
- Instrument & Valve Specification Review
- Submittal Development & Approval
- Procurement
- Instrument & Valve Receipt Verification (against Specification) & Inspection
- Instrument & Valve Bench Test
- Instrument & Valve Installation (by others)
- Instrument & Valve Installation Check and Loop Check (with Systems Integrator)
- Instrument Calibration (pre and/or post commissioning)
- Deliver ETOP
Specifics about the execution of these tasks will be discussed more thoroughly in upcoming blogs. In the meantime, if you have any questions regarding our MIV services, please feel free to reach out to us.
About the author
Pete is a graduate of the University of Vermont, with a B.S. in Electrical Engineering and a Masters of Business Administration. He originally joined Hallam-ICS in 1995 (leaving in 2001 and returning again in 2005) as Controls Engineer. Currently, he serves as a Project Manager and Team Leader for the Control Systems Integration group. Outside of work Pete enjoys skiing, golfing, music, and coaching his kid’s baseball / softball teams.
Read My Hallam Story
About Hallam-ICS
Hallam-ICS is an engineering and automation company that designs MEP systems for facilities and plants, engineers control and automation solutions, and ensures safety and regulatory compliance through arc flash studies, commissioning, and validation. Our offices are located in Massachusetts, Connecticut, New York, Vermont and North Carolina and our projects take us world-wide.
You May Also Like
These Related Stories
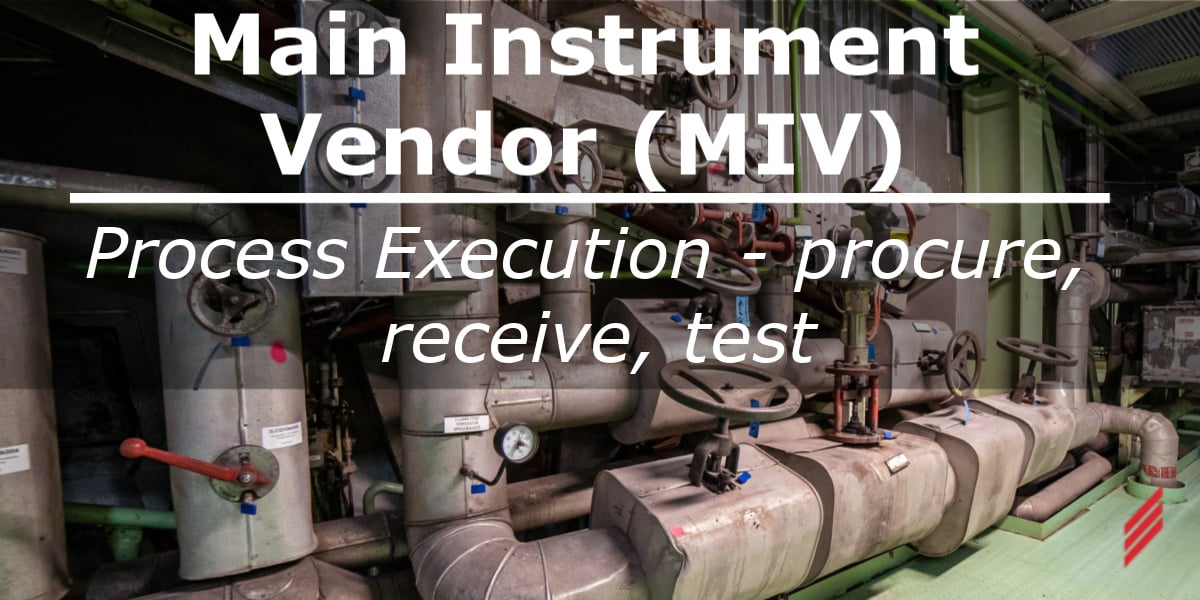
Main Instrument Vendor (MIV) Process Execution - Procure, Receive, Test
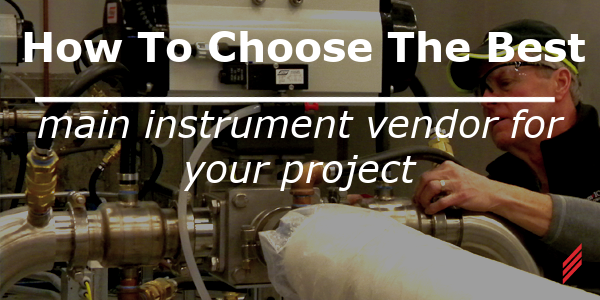
How To Choose The Best Main Instrument Vendor For Your Project
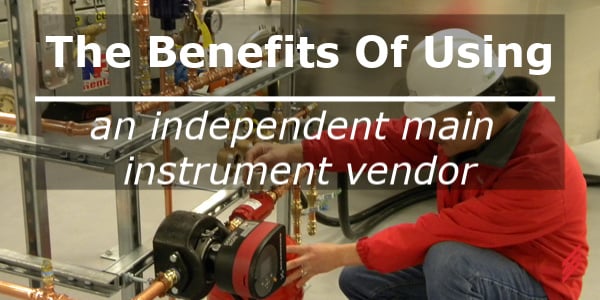
Comments (4)