Three Common Misconceptions that are Costing You Money
by Chris Giusto on Apr 23, 2020 10:30:00 AM
If you set out to build a new industrial facility costing hundreds of millions of dollars, you would certainly have an engineering firm as part of your project team. Right? But for smaller projects at existing facilities, project managers often ask themselves if it is necessary to have an engineer involved.
The question I would encourage you to ask yourself is not, “Do I have to have an engineer to do this project?” but instead, “Can I get any value out of having an engineer involved in my project?” In this and future blogs, I explore three common misconceptions that cause project managers to lose out on the value of working with an engineer:Misconception #1: My project is too small/simple to get engineering involved.
Engineering is often viewed as an unnecessary expense on projects that are perceived as “too small” or “not complex enough” to involve an engineering firm. “Small” and/or “simple” projects often have tight budgets and the fear is getting a high paid consultant involved will just make things more complicated and expensive.
The first problem with this misconception is that it’s talking in absolute terms about something that is relative. “Too small,” “too simple,” or “too expensive” imply that there are some thresholds above or below which a decision should be obvious. But these terms – size, complexity, expensive – are all relative terms. A good engineer will discuss your project with you to understand what you need and scale their proposed scope of work accordingly, thus ensuring you receive maximum value.
Something else to consider when talking about “expensive” is the 1-10-100 rule for quality. If you are not familiar with this concept, the rule basically says if an issue costs $1 to prevent, it costs $10 to correct, and it costs $100 if the issue is not corrected and a failure results. Some descriptions go on to add that it costs $1000 in lost business due to a damaged reputation.
The 1-10-100-1000 Rule
For years I’ve shared this same concept with my clients. It costs $1 to fix an issue on paper (in design), $10 to fix it in the shop (prior to shipment), $100 to fix it in the field (during construction), and $1000 if not corrected and you have to live with that operational deficiency for an extended period of time. Having a trusted engineer involved helps make sure as many issues as possible are identified and resolved as early as possible (at the lowest cost), no matter the size or complexity of the project.
SIDE NOTE: Generally speaking, $5000 will get you about a week’s worth of an engineer’s time. For a small project, 40 engineering hours can go a long way to help identify issues and work out details, resulting in a quicker installation with minimal rework and less down time. How much does one hour of down time cost your facility?
Sometimes a few drawings, simple letter specifications, or a brief scope of work document is all it takes to prevent a compromised installation or a delayed start up. Not all engineers believe they get paid by the pound for their deliverables!
A few words about price and value:
Consulting engineers are often perceived as being expensive, commonly charging $100-$150 per hour, and even more for those with specialized skills or experience. That may seem like it would add up very quickly. However, engineering frequently accounts for only around 5% of total project costs, while equipment/materials and construction account for the rest. If you consider the full life cycle, including operation and maintenance, engineering costs drop to less than 2%. Consider that 2% of your investment will directly impact how much value you can get out of the remaining 98%, and engineering looks like a tremendous bargain!
About the Author
Chris Giusto is Regional Manager for the South Atlantic and Director of Combustible Dust Safety at Hallam-ICS. He works with clients to improve processes & safety, reduce waste & energy consumption, increase flexibility & capacity, and build new facilities. He has over 20 years of engineering experience and leads Hallam’s Combustible Dust Safety Service offerings. He’s spent nearly his entire career working with combustible dust hazards and designing NFPA-compliant equipment and systems. With additional expertise in material handling and dust collection system design, he and his team bring a comprehensive approach to practical solutions for improving safety and meeting NFPA requirements.
Read My Hallam Story
About Hallam-ICS
Hallam-ICS is an engineering and automation company that designs MEP systems for facilities and plants, engineers control and automation solutions, and ensures safety and regulatory compliance through arc flash studies, commissioning, and validation. Our offices are located in Massachusetts, Connecticut, New York, Vermont and North Carolina and our projects take us world-wide.
You May Also Like
These Related Stories
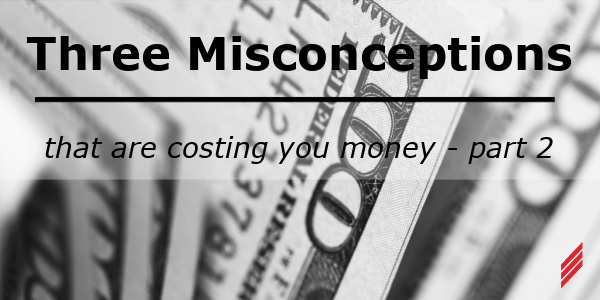
Three Common Misconceptions that are Costing You Money-Part 2
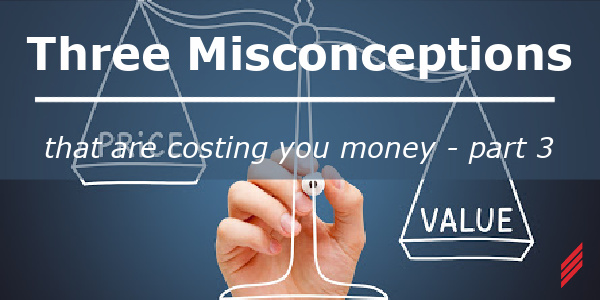
Three Misconceptions that are Costing You Money- Part 3
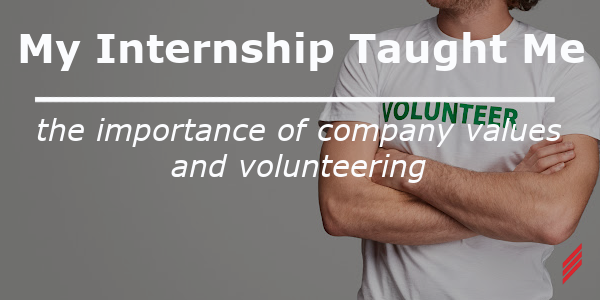
No Comments Yet
Let us know what you think