Toxic Gas Monitoring System Service and Maintenance Plan- Part 2
by Vin Calio on Feb 24, 2022 10:30:00 AM
In my last blog I outlined what a TGMS is and items that need to be considered when planning your TGMS service and maintenance plan. In this blog I will help you develop the procedures and maintenance program components required for a complete and comprehensive service and maintenance plan.
Documentation
The next component of a TGMS maintenance plan is Document Control. The standard associated with this requirement is NFPA 72- 14.2.5.
Maintaining comprehensive, and updated documentation of both the system design as well as all modifications, scheduled maintenance, sensor replacements, tape changes and system testing will allow you to demonstrate compliance should an issue arise with a regulatory agency.
Keeping these documents in a central, secure location will ensure that they cannot be modified by unauthorized personnel. It will also provide the necessary access should it be needed for repairs or modifications in the future.
Some examples of documents that should be maintained include:
- I/O List
- This shows all the sensors and beacons connected to the system as well as any external connections to other systems such as a fire alarm system or gas delivery system.
- Plan View Drawings
- These outline the physical location of the central control panel as well as all sensors and beacons connected to the system making them easier to locate in the field.
- Panel Wiring Schematics
- Maintaining an updated wiring diagram of the central control panel will make repairing or modifying the system easier in the future.
- SOPs
- Keeping all of your operational and maintenance SOP’s in a central, secure location simplifies access for operations and maintenance personnel.
- Integration change log
- This is a log of any programming changes made to the system after it was installed to accommodate new external device connections or added functionality. Keeping a record of any programming changes, as well as an offline copy of the associated programs will make any future repairs or modifications easier.
- Contact list for TGMS paging/notifications
- For systems that are designed to automatically notify certain personnel of any alarm conditions, it is critical to keep that notification list updated. This ensures that the proper people are notified of an event depending on the time of day or day of the week that the event occurs. It also accounts for any personnel changes that occur throughout the life of the system such as work schedule changes, new employees or employees that are no longer with the organization.
- Not all TGMS systems have this functionality as sometimes it is handled through other building systems. If your system does, it is critical that you keep this information current to ensure that the right people are notified of a hazardous condition so that they can take the appropriate action.
- Sensor replacement log
- For systems that utilize electrochemical sensors, those sensors have a limited operational life and must be replaced periodically. It is important to maintain records of this work to be able to demonstrate that your system has been properly maintained and can perform its intended function reliably.
- Annual Maintenance and Testing Documentation
- Maintaining detailed records of all maintenance and testing activities is important to be able to demonstrate compliance and proper system operation to a regulatory agency. This could be because of a routine audit or in response to an incident. Either way, you will want to be able to quickly produce your maintenance records should they be requested. Demonstrating a well-organized and comprehensive maintenance program can help reduce your exposure in situations such as these.
- Maintaining detailed records of all maintenance and testing activities is important to be able to demonstrate compliance and proper system operation to a regulatory agency. This could be because of a routine audit or in response to an incident. Either way, you will want to be able to quickly produce your maintenance records should they be requested. Demonstrating a well-organized and comprehensive maintenance program can help reduce your exposure in situations such as these.
Visual Inspections
This generally starts with a simple visual inspection which is exactly what it sounds like. Using the Plan View drawings and other system information, each device on the system should be inspected visually to ensure that there are no obvious issues.
Depending on the type of device, this may include:
- Error messages
- Fault indicators
- Physical damage
- Disconnected wiring, etc.
Recommissioning
The standard associated with this requirement is NFPA 72-table 14.4.3.2
This involves a functional check of each device and its connection to the central control system whether that is a PLC or SCADA system. Testing outputs like the Gas Alarms Notification devices (horns and strobes) or gas shutdown devices as well as inputs such as from a fire alarm system.
Filter Replacement
Filters require replacement after about 3-6 months depending on the environment. A cleanroom environment may allow for longer intervals between replacements.
Chemical Tape Changes
Chemical tapes are constantly moving. They are considered a consumable item and need to be replaced periodically. Chemical tapes need to be stored properly and because of this, generally ordered on a “just in time” basis.
Sensor Replacement
For systems that utilize electrochemical sensor technology, these sensors typically have an operational life of 2-3 years after which they become ineffective and require replacement.
Replacement sensors are ordered on a “just-in-time” basis due to their limited shelf life. Proper planning is necessary to ensure that the needed replacement parts are on hand when scheduling the shutdowns necessary for replacement to minimize downtime.
Replacement sensors typically come with a factory calibration, but a bump-test is typically performed to test operation before putting the TGMS back into operation.
Integration Support
Occasionally changes to the functionality of the system may be necessary. It is important to allow enough time for modifications to be made and for the necessary commissioning and validation. Some of these changes might include:
- Addition, removal, or relocation of equipment with the facility
- Addition or removal of GAN’s
- Addition or removal of gas detection devices
- Changes in connections to FAS, gas delivery or other external systems
Gas Challenging and Calibration
All electrochemical sensors need to be gas challenged upon initial installation and periodically thereafter. Sensors are challenged, or “bump tested” every 6 months to ensure they are operating properly.
Testing involves specialized knowledge and equipment, and calibrated cylinders of the target gases. This work is typically performed by an outside contractor.
A comprehensive TGMS maintenance plan ensures that the life safety system is functioning properly and protecting the people working in your facility. Given the nature and the limited operational life of critical components, it is crucial to have a plan and to execute it reliably and timely.
Please don't hesitate to contact my via email, vcalio@hallam-ics.com with any questions you might have or contact our Help Desk by clicking the button below.
About the author
Vin Calio is the Regional Manager, South New England. He is an Electrical Engineer with over 15 years of experience in automation and control systems.
Read My Hallam Story
About Hallam-ICS
Hallam-ICS is an engineering and automation company that designs MEP systems for facilities and plants, engineers control and automation solutions, and ensures safety and regulatory compliance through arc flash studies, commissioning, and validation. Our offices are located in Massachusetts, Connecticut, New York, Vermont and North Carolina and our projects take us world-wide.
You May Also Like
These Related Stories
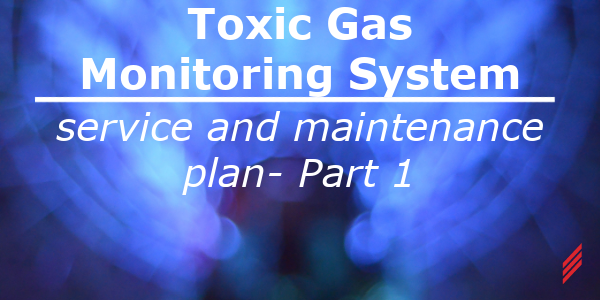
Toxic Gas Monitoring System Service and Maintenance Plan- Part 1
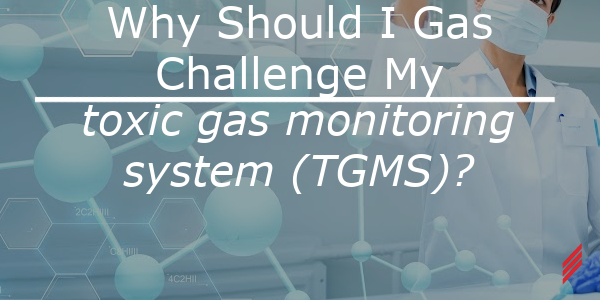
Why Should I Gas Challenge My Toxic Gas Monitoring System (TGMS)?
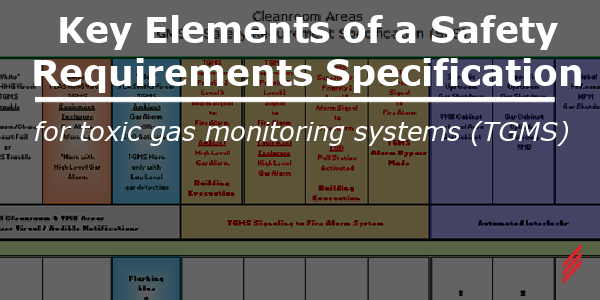
No Comments Yet
Let us know what you think