Key Elements of a Safety Requirements Specification for Toxic Gas Monitoring Systems (TGMS)
by John Kurowski on Jun 13, 2024 10:00:00 AM
From the Author
My friend and colleague, Jim Blais, originally wrote the contents of this blog as part of a White Paper. I have decided to break up the original White Paper into four separate blogs that are detailed below. Hallam-ICS will publish one blog per month, for four months. I wanted to get this valuable information back to the forefront of our clients and potential clients.
As Jim Blais originally wrote: Hallam’s controls experience has evolved into a more dedicated passion and focus – for the integrity of safety control system platforms, as they apply to hazardous gas and chemical monitoring; to ensure the safe storage, handling and use of hazardous materials used in research laboratories and semiconductor manufacturing facilities. A small client sample includes Applied Materials, Akoustis, ASML, Boston University, Cornell University, Global Foundries, IBM, MIT, MIT -Lincoln Laboratories, and many others.
Introduction
Jim Blais originally developed this section of his white paper to provide best practices through years of studying codes, attending (SESHA) seminars and meeting with other safety professionals. All of us at Hallam-ICS hope that this will serve to answer questions you may have or stir thought that will lead to creative approaches to TGMS’ in the future. This blog will cover only the second topic below. (The first topic was published last month and can be accessed below.) Hallam-ICS will publish the remaining two topics in subsequent months.
- Harmonizing Code and Best Practices for a TGMS
- Key Elements of a Safety Requirement Specification (SRS)
- Selection of Toxic Gas Monitoring Detection Technologies
- How to Properly Select Toxic Gas Monitoring Locations
Key Elements of a Safety Requirement Specification (SRS)
Developing a Safety Requirement Specification (SRS) or functional “cause & effect” matrix for a TGMS is absolutely critical to identify and then eliminate potential gas related hazards. The purpose of the approved SRS is to provide people, equipment and the facility with safety and freedom from unacceptable risks.
Development of an SRS requires participation of cross-functional disciplines (EH&S, Facilities and FAB Engineers and Management). The approved SRS becomes the basis of design for the TGMS. Depending upon the acceptable risk, the required reliability of the TGMS can be further ensured by understanding and providing effective measures of:
- failure avoidance
- failure detection
- failure tolerance
This reliability applies to all of the toxic gas monitoring safety sensors, the logic controller and the required final control elements (gas shutdown /alarm/fault notifications).
The required reliability is to keep the “probability of failure” as low as possible (failure avoidance), or to detect failures by diagnostic functions (failure detection) and – in the case of a detected failure – to force the safety system to go into a safe state (failure tolerance).
Therefore the SRS should identify…
- Each potential hazard and its consequences
- Definition of the process safe state
- Description of all safety functions
- Description of each alarm level trip point and associated measurement values
- Maximum response time requirements
- Manual safety activation of the safety functions
- Safety function responses to diagnostic faults (shutdown/interlocks, alarm only, or other)
- Local alarm / trouble – notifications (visual and audible)
- Local alarm / trouble – HMI visualization (access and content)
- Remote “Emergency Responder” alarm / trouble – notifications (paging, texting, email)
- Remote “Emergency Control Station” alarm / trouble – HMI visualization (access and content)
- Include maintenance override capability requirements
- Provide system alarming bypass capability requirements
- Requirements for reset or alarm recovery
Common Issues with an SRS
A poor SRS is the root cause of 44% of safety system problems. The largest single cause being that the needed functionality is missing or incorrect. EPA and OSHA findings of recent accidents find that common themes include:
- Inadequate hazard review or process hazard analysis
- Use of inappropriate or poorly designed equipment – better performance was required.
How best to proceed with determining a TGMS’ requirements and the needed safety functions?
- The “process industry” has adopted an approach that begins with a “hazard analysis” and “risk assessment”.
- This is a step by step approach based upon the “IEC 61508” (an umbrella Safety Standard) along with IEC 61511 being specific to safety in the process industry. This has been adopted as a fully compatible ANSI/ISA-84.00.01-2004 standard, which is the USA version of IEC 61511 (with one reference used from OSHA 29CFR1910.119).
It is important to remember that there may be gas detection challenges that are not always safely addressed by minimum code compliance.
- There are potential hazardous gas target “cross sensitivities” and “interferences”, that interfere with certain selected gas target sensors and gas detection technologies.
- These hazardous gas materials may “suppress sensor response or cancel sensor response” by driving the sensor response negative.
- Depending upon the specific gas leak type and the applied detection technology; poisoning a sensor element may occur; making it unresponsive – and – “unavailable” for detection and protection!
Establishing Gas Alarm Levels
As described in the previous section, setting SRS gas alarm levels for individual gas targets should not focus solely upon applying the mandatory (minimum) code requirements (e.g., OSHA PELs), but it should always consider authoritative requirements and best practices (e.g., NIOSH RELs, and ACGIH® TLVs).
Threshold Limit Values (TLVs®) refer to airborne concentrations of chemical substances and represent conditions under which, it is believed that nearly all workers may be repeatedly exposed, day after day, over a working lifetime, without adverse effects. The ACGIH® TLVs® are widely recognized as authoritative, and are required to be included on safety data sheets by the OSHA Hazard Communication Standard.
NOTE
OSHA recognizes that many of its permissible exposure limits (PELs) are outdated and may be inadequate for ensuring protection of worker health. Industrial experience, new developments in technology and scientific data clearly indicate that in many instances these adopted limits are not sufficiently protective of worker health.
This has been demonstrated by the reduction in allowable exposure limits recommended by many technical, professional, industrial, and government organizations, both inside and outside the United States. To provide employers, workers, and other interested parties with a list of alternate occupational exposure limits that may serve to better protect workers, OSHA has annotated the existing Z-Tables with other selected occupational exposure limits. OSHA has chosen to present a side-by-side table with the NIOSH Recommended Exposure Limits (RELs) and the ACGIH® TLVs®s.
OSHA’s mandatory PELs in the Z-Tables remain in effect.
However, OSHA recommends that employers consider using the alternative occupational exposure limits because the Agency believes that exposures above some of these alternative occupational exposure limits may be hazardous to workers, even when the exposure levels are in compliance with the relevant PELs.
Benefits of a Safety Requirement Specification and Periodic Testing
The SRS provides the Owner with a functional specification that records all monitored hazards, their locations, alarm set-points and the actions taken when predetermined limits are exceeded. The SRS can be provided to and reviewed with the local AHJ to address any concerns during the design phase.
Used as a validation/commissioning test document to record system performance during startup, it also becomes a “living record document” that can be used as an auditable record of periodic testing records, required throughout the life of the safety system.
Note - “periodic functional testing” of each gas sensor (recorded with the SRS) is highly recommended and required given that many gas sensors utilize “consumable sensors” and the probability of sensor failure therefore continuously rises with operational time.
- Periodic testing effectively “resets” the probability of the sensor and control platform to “not” perform the required safety functions back to zero.
- Successful “on demand” detection and performance of the TGMS functions are both demonstrated and reassured by periodic validation testing.
Once the SRS has been developed and the gases to be monitored have been clearly identified, the design team can then proceed with selecting the most appropriated gas detection technology to utilize along with the best locations for the gas sensors.
About the Author
John has a B.S. in Chemical Engineering from Penn State and a M.S. in Manufacturing Engineering from RPI. Prior to coming to Hallam-ICS, John had 30 years of experience working in Manufacturing/Process/Facilities Engineering for printed circuit board and semiconductor manufacturing. As a Senior Engineer at Hallam-ICS, John is responsible for the design and specification of Toxic Gas Monitoring Systems. He participates in all project design phases from concept through construction documents.
Read My Hallam Story
About Hallam-ICS
Hallam-ICS is an engineering and automation company that designs MEP systems for facilities and plants, engineers control and automation solutions, and ensures safety and regulatory compliance through arc flash studies, commissioning, and validation. Our offices are located in Massachusetts, Connecticut, New York, Vermont and North Carolina and our projects take us world-wide.
You May Also Like
These Related Stories
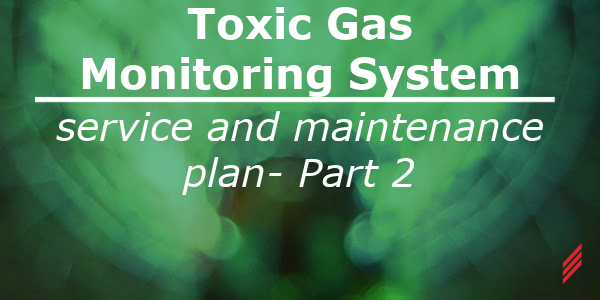
Toxic Gas Monitoring System Service and Maintenance Plan- Part 2
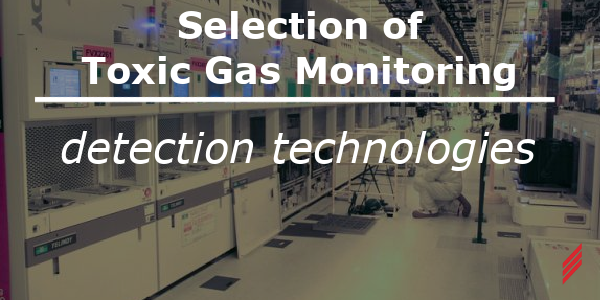
Selection of Toxic Gas Monitoring Detection Technologies
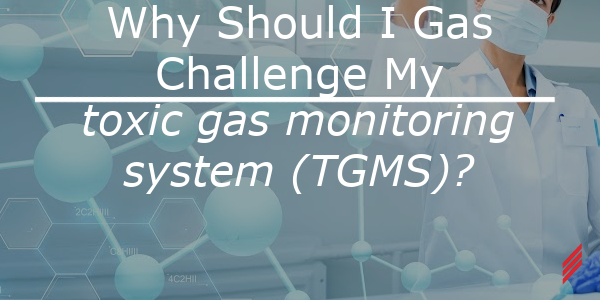
No Comments Yet
Let us know what you think