2017 Arc Flash Game Changers
by Brian Crosby on Jan 17, 2017 3:49:06 PM
2017 Trends is a 5-part blog series that takes a look at how the latest technology, economic developments, evolving user expectations and changing industry standards might affect the way we all do business.
- 2017 Trends – 2017 Arc Flash Game Changers
- 2017 Trends – The Latest in Gas Detection: New Technology for 2017
- 2017 Trends – LEED v4, ASHRAE Guideline 36 and Other MEP Engineering Trends for 2017
- 2017 Trends – 4 Trends to Watch in Industrial Automation in 2017
- 2017 Trends – 3 Things That Will Impact Your Business in 2017
Introduction
At Hallam-ICS, 2016 was a year of electrical safety and arc flash changes. We learned so much by keeping up with changing industries and simply listening to our customer’s concerns and needs. During the year, there were four areas that generated the most interest from our clients:
- Arc Flash and Incident Energy
- Equipment Maintenance
- Electrical Safety Training
- Cost
These subjects will stay on top of our concern list throughout 2017.
Arc Flash and Incident Energy
After speaking with our clients, we have found most are concerned about equipment in their facility that have high-incident energy and the dangers of their staff working on energized equipment. Although the best practice is to de-energize, this isn’t always an option. There are many ways to mitigate high incident energy using fiber optic relays, zone selective interlocking and maintenance bypass switches. A growing concern from 2016 was the front service entrance where the utility enters the facility. This is where you can see the largest amount of fault current. Even if you mitigate incident energy within the main switchgear, there is always the danger of incident energy on the primary side of the main breaker.
Solutions:
- Virtual mains
- Medium voltage relays
- Reclosers
These methods have eliminated dangerous incident energy in the facility by disconnecting the power on the higher voltage side. This allows regular maintenance to be performed on the lower voltage side with reduced incident energy. As safety is always our priority, we are keen on providing solutions that make our clients more aware of best practices.
Equipment Maintenance
Equipment maintenance is very important for the safety of employees within a facility. On average, 90% of the equipment we surveyed in 2016 was 40+ years old. As equipment deteriorates over time, regular maintenance and testing is vital for smooth operations.
Most people think that a breaker is an electronic device. The truth is, a breaker is a mechanical device when it operates. ANSI defines a circuit breaker as a mechanical switching device. Some breakers use springs for the switching. For instance, think about a spring that is under tension waiting for a fault or something to release that tension. Now, think about that same spring stretched in the same position for 40 or more years. This is why calibration and maintenance is so important.
A common maintenance standard (NFPA 70B) requires power circuit breakers to be calibrated by the manufacturers’ guidelines every three years. How long has it been since the breaker in your facility was turned off and back on to distribute lubrication within the casing?
Solutions:
- Maintain equipment frequently in an accurate and safe manner.
NFPA-70B highly stresses the importance of equipment maintenance for facilities and will again for NFPA 70E-2018.
Electrical Safety Training
Whichever industry you work in, staff safety training is extremely important. As a company, we offer Qualified Low Voltage Electrical Safety Training. It is amazing how many employers are unaware that this is a requirement of NFPA-70E and needs to be done every three years.
“It is amazing how many employers are unaware that [Electrical Safety Training] is a requirement of NFPA-70E and needs to be done every three years.”
The key to this training is one word: Qualified. Qualified shows that someone is properly trained and has the skills and knowledge to work on energized equipment. Many electricians –and even managers-- that sat in on the classes I taught in 2016, walked into the class thinking “I don’t need it” or “It’s nothing.” However, by the end of it, they were stunned and said it was an “eye opener” for them. They did not realize just how dangerous electricity could be and why it was so important to have Electrical Safety Training. This training is not to scare someone into a new profession, but to help them realize how important safety is for themselves and their fellow co-workers.
Solutions:
- Make safety awareness more prominent by training your staff
I started to see a sharp increase of employers wanting to get their electricians and maintenance staff trained and I’m certain that number will rise in 2017.
Cost
Businesses want to create a safe working environment for their employees and stay on OSHA’s good side. However, one of the biggest concerns from our clients in 2016 was fearing a high expense.
Solutions:
- The same team of engineers completes the arc flash work from start to finish
- Use infrared and testing maintenance companies to reduce labor costs
- Easy access to information reduces the cost of running an Arc Flash Study every five years
To address the cost concern, Hallam-ICS developed ways to improve our efficiency to help drive down costs.
First, we have the same team of engineers work on arc flash from start to finish. We don’t use outside firms to do survey field work. There is no break in the process that can lead to an inaccurate Arc Flash survey and potentially dangerous mislabeling. The person that surveys the site is the same person that writes the report and returns to label the equipment.
Second, we try to perform the arc flash survey at the right time. Teaming with Infrared and testing maintenance companies decreases survey time, which then reduces labor costs. When a company is getting its annual IR (infrared) completed, this is the perfect time to survey the equipment while the covers are off. This helps to get two things done at once for the client with reduced labor cost.
Third, readily available information can be easily updated, thus reducing cost. We keep copies of every report we produce. Since it is required to update an Arc Flash Study every five years we remind our clients when it is time for an Arc Flash update. Utility companies constantly make changes to their system, which means the available fault current contribution will likely affect results of the study. If no changes were made within the facility, we just have to plug in updated utility contribution information and rerun the study. If the facility underwent changes, Hallam-ICS helps clients stay on track of maintaining equipment/safety and we’ll have access to all information for a quick and easy update. This saves money for our customers.
2016 was a year of awareness; more and more companies are finding out the importance of worker safety. I feel that 2017 will be a landmark year for electrical safety in the workplace. To learn more about Hallam-ICS Arc Flash and electrical safety services click here.
About the author
Brian Crosby is the Arc Flash Safety Supervisor for all Hallam-ICS and runs our arc flash business out of our Raleigh, NC office. Brian has been with the company for over 15 years.
Read My Hallam Story
About Hallam-ICS
Hallam-ICS is an engineering and automation company that designs MEP systems for facilities and plants, engineers control and automation solutions, and ensures safety and regulatory compliance through arc flash studies, commissioning, and validation. Our offices are located in Massachusetts, Connecticut, New York, Vermont and North Carolina and our projects take us world-wide.
You May Also Like
These Related Stories
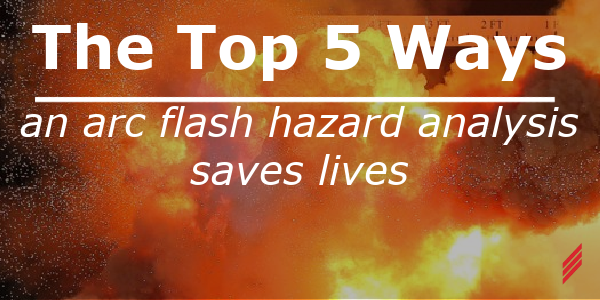
Top 5 Ways an Arc Flash Hazard Analysis Saves Lives
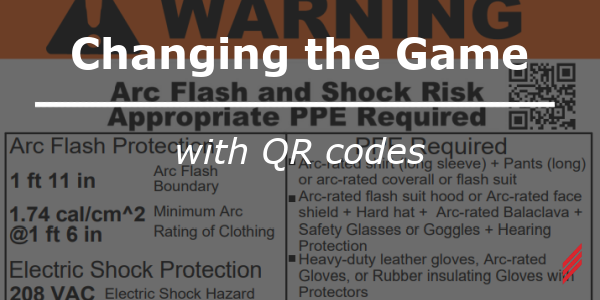
Changing the Game with QR Codes
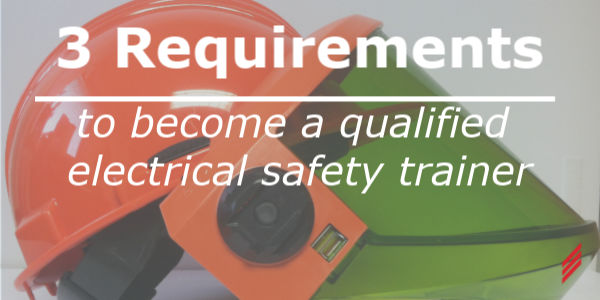
No Comments Yet
Let us know what you think