The Importance of Metallic Piping Welding Qualification Submittals Part 1-Definitions
by William Neuburger on May 6, 2021 10:30:00 AM
As mechanical engineers in the built environment, our work often covers metallic piping with welded joints. We deploy metallic pipe welding for chilled and hot water for space conditioning, chemical solutions for industrial processing, and steam for any purpose. Piping and joining system specifications often include requirements for quality assurance and submittals, similar to many other aspects of a project. This blog describes a typical building services piping weld submittal process and scope of a welding submittal and shares some recent experiences.
It would be mendacious to say I have always been vigilant in reviewing weld submittals. However, I became more vigilant and diligent after a project with a specialty piping consultant on the team. The sub-consultant working with us provided a clear weld submittal process in the contract documents and held the installer to the contract documents. This firm’s commitment to quality inspired me to do better.
A few definitions and explanations:
- Procedure: This is the method by which the welder (a person, not the welding machine) performs a weld. The American Welding Society provides a template for describing the process in a Standard Welding Procedure Specification (WPS and SWPS are common acronyms). The Procedure allows the user to describe the materials, size, thickness, welding position, filler material, pre-heating, grinding and other information. One can consider the Procedure as the recipe for the welding process.
Many installers use a template from the American Welding Society for their Procedure submittal. Some installers submit pipe welding procedures from the United Association, the trade union which represents pipe fitters and plumbers. The engineer’s specification should define the contents and format for the submittal, clarity helps the installer develop their submittal accurately and allows the engineer to review it quickly.
- Qualification: This form documents a testing and inspection plan which ultimately can qualify a Procedure. The American Welding Society provides a template for documenting the qualification in their Procedure Qualification Record (PQR) Form. A welder performs the Procedure under the watch of a certified weld inspector who visually inspects the weld, performs various tests (tensile strength, radiographic) and certifies the Procedure is adequate for the identified service. This form also confers an individual welder a certification to perform the welding procedure. The Qualification (sometimes called a certification) for the individual has an expiration date, after this date the welder must re-qualify on the procedure.
For an overview of SWPS: American Welding Society
In Part 2 we will discuss the submittal and review process and potential improvements.
About the Author
Bill has been a mechanical engineer since 1995 and with Hallam-ICS since 2010. His career has brought him to the top of the Transamerica Pyramid Center, chemical plants, underground mines, paper mills, and semiconductor fabrication facilities. He has experience designing, specifying and installing mechanical and electrical systems in the built environment covering industrial, institutional and commercial facilities.
Read My Hallam Story
About Hallam-ICS
Hallam-ICS is an engineering and automation company that designs MEP systems for facilities and plants, engineers control and automation solutions, and ensures safety and regulatory compliance through arc flash studies, commissioning, and validation. Our offices are located in Massachusetts, Connecticut, New York, Vermont and North Carolina and our projects take us world-wide.
You May Also Like
These Related Stories
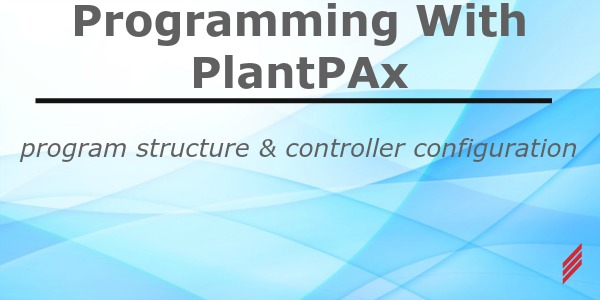
Programming with PlantPAx - Program Structure & Controller Configuration
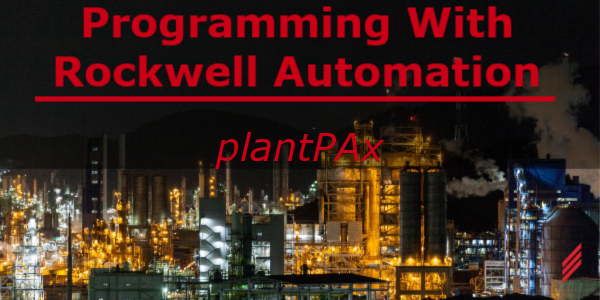
Programming with Rockwell Automation's PlantPAx
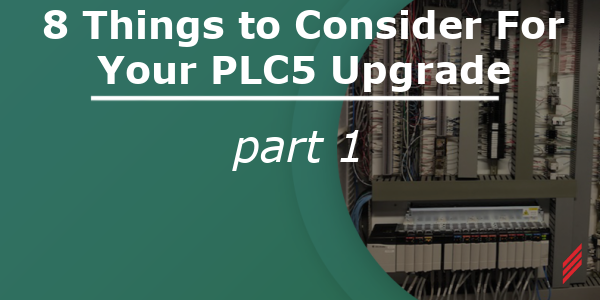
Comments (1)