8 Things to Consider for Your PLC5 Upgrade- Part 1
by Ray Racine on Jan 20, 2022 10:30:00 AM
You know you need to upgrade; Where do you start?
Rather than risk an unplanned shut down of your line, you need a planned conversion and cutover strategy. In this two-part blog series we will discuss the following 8 things to consider when upgrading your PLC5.
- Re-envision your system
- Follow the Money
- What do you have to convert?
- What could go wrong?
- Your PLC5 code
- Your SCADA/HMI
- Your Panelboards
- How are you going to cut this system over?
Re-envision your system
Dream but don’t blow the budget. A lot has changed since your PLC5 went into service. This system may not see another major upgrade for 25-30 years; so how can you capture the possible as regards improvements?
- KISS – Controls can be hard. Keep it as simple as possible. Fancier is not always better. Ask yourself if there are things in your current system that might be weeded out?
- Networks – What is the current system using? What do you see yourself using after the conversion? I strongly recommend two ethernet cards in your main PLC rack, one for SCADA communication, and one for I/O support to keep IT out of your control system networks as much as possible.
- Safety – Barely a thought 30 years ago. Are there safety features you should build into this upgrade? Should you use a safety processor, or bolt on safety relays?
- Motion – Did the old PLC5 system support motion control? New processors have native motion support. Should you be looking to move the motion control into the new PLC?
- Solenoids – If you have a bunch of them on your current installation, you may wish to consider modern solutions. At least two vendors sell multi-station manifolds that can be dropped into the I/O tree of your new Logix / Studio 5000 PLC code. This could clean up a lot of wiring and a lot of Output points.
- VFDs – If you have them on your PLC5 control system, they probably need to come up to the current century as well. Like the PLC5, your 1305 & 1336 drives are pretty bulletproof but for how much longer? While you are thinking about your drive upgrades, do you want to hardwire them, or network them? Your answer should be based on the level of your maintenance staff’s software skills, as networked drive replacement is often not as simple as you would think.
- Oversized motors – Everybody has them and most of them run across the line. Do you have motors that should be on drives instead of starters? Drives are much cheaper and more reliable now than they were when your PLC5 system went into service. While you are thinking about drives, are there control valves on lines that should be replaced with motors and VFDs?
Follow the money
So, did your boss give you a magical number for budget, or do you have to build a case and fight for your own budget? Can you do this project in one budget cycle, or will you have to do it in stages over several cycles? Your project approach, and the order in which you do things, can be greatly impacted by the answer to these questions. Having to convert your system over several years may be a blessing. You might be able to get more done for your system if you can get more money out of multiple budget cycles, rather than squeezing it into a single year.
What do you have to convert?
This is where a detailed system survey comes in. Get the part number of every card in every chassis.
Network Diagrams – when your PLC5 system went in, odds are decent ethernet as a control network was not around. You probably have remote I/O, or ControlNet, or DH+. Maybe DeviceNet. Well, of those networks, RIO is gone. ControlNet and DH+ are on the way out. Whatever you have, you need to get to Ethernet; so, include that in your to do list.
Converting the I/O is fairly straight forward; but considering your networks may not be as easy. If you have drives or other I/O drops with communication cards, you should really try to get to Ethernet if it makes sense. If the drives need to be replaced but not on this project, consider hard wiring I/O until drive upgrades happen.
Take good pictures of each enclosure. If the person building up the estimates is working remotely, it can be a great time saver. Pulling the wire way cover off, before taking those pictures can help as well.
What could go wrong?
1771 Output modules carried a lot more current than new ControlLogix equivalents. If you have a lot of devices with significant amp draw, you may need to buy a bunch of relays and put them somewhere – OR – consider using relay output modules if switching frequency allows.
Some 1771 I/O modules will require 1:2 or 2:1 1756 modules for conversion – point counts won’t always match neatly. Old installations had a lot of 8 point Discrete cards, since that is what they made way back – consolidation to 16-point modules can save significant money in hardware.
Make sure you know if your analog inputs are differential or single ended – you could come up way short on analog cards if you miss this one, as differential inputs support ½ the point count.
The hardware conversion manual does a good job of helping you; but think before building your Bill of Materials. Some of the recommended modules are much more expensive than another that might serve as well. You can save a lot of $$$ by not following the conversion manual blindly. Thinking outside the box here is key. Sometimes custom is better
On the conversion described above, we were able to save our client over $100,000 in materials, by using lower cost modules and custom wiring harnesses.
What about the stuff connected to the PLC5? RIO and ControlNet drops definitely need to be changed. There is no sense in upgrading legacy networks unless absolutely needed.
In the next blog I will cover the last 4 items to help you successfully plan your PLC5 to ControlLogix conversion.
If you have any questions, please email me at rracine@hallam-ics.com or contact us here:
About the author
Ray has retired from Hallam-ICS, but his contributions to the company continue to be valued.
Read My Hallam Story
About Hallam-ICS
Hallam-ICS is an engineering and automation company that designs MEP systems for facilities and plants, engineers control and automation solutions, and ensures safety and regulatory compliance through arc flash studies, commissioning, and validation. Our offices are located in Massachusetts, Connecticut, New York, Vermont and North Carolina and our projects take us world-wide.
You May Also Like
These Related Stories
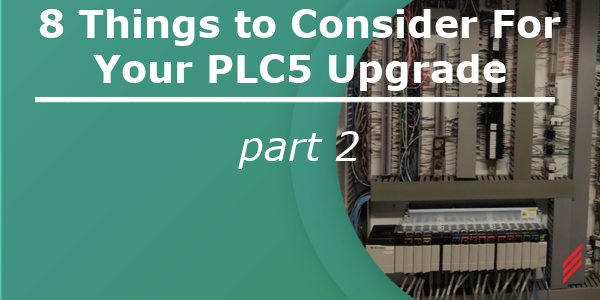
8 Things to Consider for Your PLC5 Upgrade- Part 2
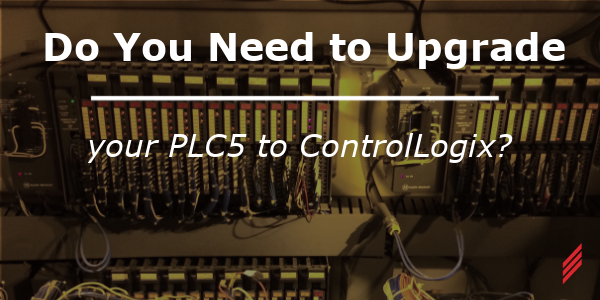
Do You Need to Upgrade Your PLC5 to ControlLogix?
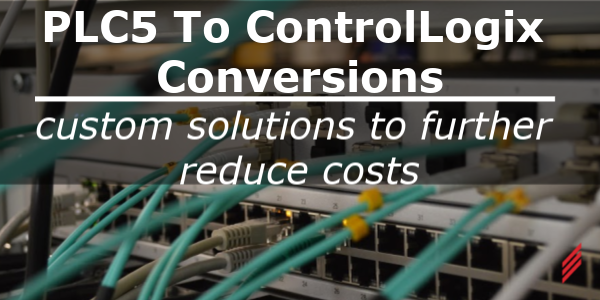
Comments (1)