PLC5 to ControlLogix Conversions – Custom Solutions to Further Reduce Costs
by Ray Racine on Nov 14, 2019 12:09:00 PM
PLC5 Conversions 3-Part Series detail considerations when performing a PLC5 to ControlLogix conversion.
PLC5 to ControlLogix Conversions - Part 1: Custom Solutions to Further Reduce Costs
PLC5 to ControlLogix Conversions - Part 2: 3 Ways to Meet Your Budget
PLC5 to ControlLogix Conversions - Part 3: A multi-year Conversion Case Study
In my previous blog: PLC5 to ControlLogix Conversions – 3 Ways to Meet your Budget, I discussed the basics of evaluating your obsolete control system conversion and budget. In this blog, I would like to highlight some of our “lessons learned” from the many systems we have already converted.
While the Rockwell Conversion manual is great for most applications: there are some holes in the offering(s). So, what pitfalls has Hallam-ICS encountered that you can learn from?
1. Power Ratings On Output Modules
Some of your old contactors, solenoids, and other powered devices are – how do I put it nicely – HOGS. They eat a lot more juice than some of their modern counterparts. In some cases the old I/O modules support four times (or even greater) the power of the modern equivalent. My guess is that you don’t have enough budget allocation to replace your old field hardware. I am also betting that you don’t want to fire every output in your system to measure the current draw and calculate the total draw on every point in every card of your control system. In some cases, the Rockwell recommended modules for the higher current cards are very expensive electronically fused cards. On one project for converting dozens of racks, Hallam-ICS was able to save a client over $100,000 in hardware costs by developing custom Conversion Cables for lower-cost modules.
Hallam-ICS has developed custom cable options to work with the Allen-Bradley Conversion modules, which allow the new Relay Output cards to replace the older, higher-current-rated modules. While some people argue with the usage of Relay Cards over Solid State outputs, it takes a long time to get to 300,000 cycles on most processing equipment. And the relay cards are fairly inexpensive so you can stock a few spares. We have custom solutions for the 1771-OA modules and the 1771-OD modules on the shelf ready to help with your conversion.
For cases, where you have high cycle rates and high output amperage, we can work with you on other solid state solutions that will meet your needs.
2. Buried Spares
If you have watched the conversion video, you can see that once you bury the conversion modules, they are fairly inaccessible. Despite Rockwell’s best effort with the top-swing pivot point, you pretty much have to pull all of your RTBs off the I/O modules to adequately access the old points on the original swing-arms. For discrete points, which are fairly inexpensive on a per-point basis, this is probably OK. For Analog Points, you may want to maintain better access to your unused I/O, particularly if you have upcoming process improvements, or a dynamic line.
Hallam-ICS frequently uses the conversion hardware for most I/O in a system, while allowing for direct wiring of certain Analog modules if the client prefers. In some cases, we have used the conversion hardware for half of a card, and direct wired the second half. It isn’t that hard if you plan for it.
3. The old I/O rack in an MCC Bucket
Hallam-ICS has encountered dozens of these in legacy systems. Allen-Bradley had some bucket inserts for the Centerline series that accepted 8-Slot I/O racks; so that you could wire the Start/Stop/Aux for each bucket in that section without long I/O runs. Remote I/O cards communicated back to your processor and life was good.
Unfortunately the bucket depth will not support the standard conversion hardware. One of our clients had 14 such racks in their installation. Their shutdown windows did not allow the time for rewiring of the I/O and only one technician could work on a single rack at one time. We needed to adapt the Rockwell Automation standard offering to a form that would fit in these buckets and offer the quick turn-around and zero wiring errors of the Rockwell system. Hallam-ICS has developed an innovative solution that does exactly that.
No two legacy systems are identical. We look forward to seeing if you can stump us with your special requirements. Maybe you can push us to develop another custom solution or two.
To date, Hallam-ICS has upgraded more than 100 PLC5 I/O racks on over dozens of processors. We have another 25 conversions slated over the next 3 quarters. We are able to execute the physical conversions and the PLC code conversions in a very effective manner. We are also very well versed in converting existing networks to Ethernet for communications. If you have any questions on PLC5 to ControlLogix conversion strategies and potential cost savings, please contact me. We are also well versed on several other vendors’ legacy conversions; so don’t hesitate to ask about other platforms. We look forward to working with you on your legacy PLC conversion.
About the author
Ray has retired from Hallam-ICS, but his contributions to the company continue to be valued.
Read My Hallam Story
About Hallam-ICS
Hallam-ICS is an engineering and automation company that designs MEP systems for facilities and plants, engineers control and automation solutions, and ensures safety and regulatory compliance through arc flash studies, commissioning, and validation. Our offices are located in Massachusetts, Connecticut, New York, Vermont and North Carolina and our projects take us world-wide.
You May Also Like
These Related Stories
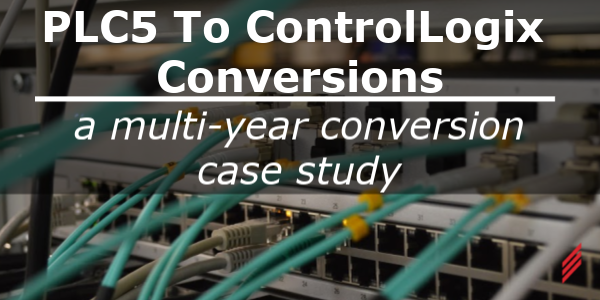
PLC5 to ControlLogix Conversions – A Multi-Year Conversion Case Study
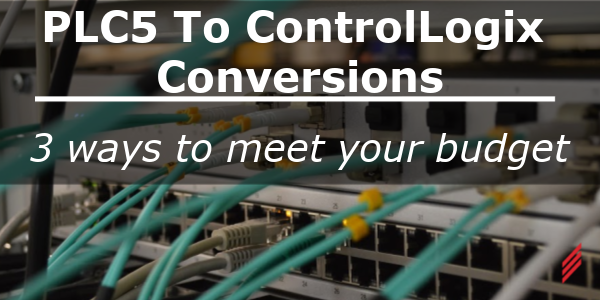
PLC5 to ControlLogix Conversions – 3 Ways to Meet your Budget
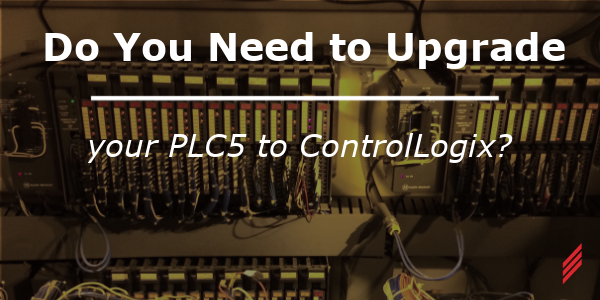
No Comments Yet
Let us know what you think