8 Things to Consider for Your PLC5 Upgrade- Part 2
by Ray Racine on Feb 3, 2022 10:30:00 AM
Rather than risk an unplanned shut down of your line, you need a planned conversion and cutover strategy. In part 1 of this blog series we discussed:
- Re-envision your system
- Follow the Money
- What do you have to convert?
- What could go wrong?
In part 2 we will cover:
5. Your PLC5 code
6. Your SCADA/HMI
7. Your Panelboards8. How are you going to cut this system over?
What About Your PLC Code? Do You Do a Canned Conversion, Or a Total Rewrite?
The Allen-Bradley PLC5 to ControlLogix Translation Tool does a great job of grinding through the code and gives great results. It flags everything it has doubts about. Check every timer because your time base is now milliseconds.
Rebuild your messaging because it does not translate. If this PLC5 is being messaged by other PLC5s, you will need to move the messaging into the converted Logix PLC, because PLC5s can’t poll tags. You need to map new I/O addresses into old register locations. With those tweaks, and a few others you have a solid promise of a clean start-up. I have never had a logic error from the translated code. I have had a couple where I missed a fix on one of the flagged items. Good News, it will now run just as it always did. Bad news, you have old pseudo- register code running in a state-of-the-art PLC. You haven’t taken advantage of add-on profiles or tag-based logic or any of the other cool features of the Studio 5000 software.
Your second option is a total rewrite of PLC5 code. If there is no sequence of operations, you need to come up with one; and program to match. It will take significant time, just like it did 30 years ago. Good news, you have consistent code and have well-written add-ons for your repeated devices. It runs great and looks like it should. Bad news, you have spent a lot of Money and time on it. It will add to your start-up and debug time. And you will need to re-do your entire data map from registers to tags in your SCADA or HMIs. It is great if you have the time and /or budget but it will cost you.
What About Your SCADA/HMI?
Is your SCADA up to date, or does it need HELP? If it is out of date, do you upgrade your system with the current version of your current SCADA, or do you replace it with a new SCADA to match plant standards? Of course, you should consider FactoryTalk for its integration with the Logix PLC products.
If you are going to do this in conjunction with the PLC upgrade, you will have debug time for the PLC and additional debug time for the SCADA during your start-up. If you do your front-end work before the PLC conversion, you will have a proven front end when the PLC conversion goes in. Your rework on the SCADA will then be a remap of the tags which should go easily.
If you are replacing the SCADA computer, add a second network card to segregate SCADA to PLC, and SCADA to office communication. Again, this helps to keep IT off of the control network. The current term for our control networks is OT or Operational Technology. IT and OT don’t always think about things the same way.
New SCADA products have a lot of hooks and better data options than older ones. Should you consider the advantages of better reports or dashboard metrics for managers?
What About Your Panel Boards?
We love our lights, pushbuttons, and switches but they eat a lot of I/O. If you have significant panelboard real estate, you really need to consider upgrading to either SCADA clients or HMIs.
How Are You Going to Cut This System Over?
Will you buy the conversion hardware for your system, or have your electricians re-wire every point?
- If you decide to hardwire the new modules, your techs will not be able to fit the original 12 & 14 gage wires under new ControlLogix or CompactLogix terminals. Do you have room and time for adding terminal blocks or pulling wires back to the original locations?
- Consider seriously using the conversion hardware. Replacing your PLC5 Rack with a conversion rack takes less than an hour, start to finish. Hard wiring each card will take a lot longer and will introduce wiring errors.
- You will have near-zero errors with the conversion hardware.
- You will need a minimum of 10” depth – measure to be sure.
- It is costly, normal I/O for most cards is on the order of $300 to $500 per card.
- If you go with conversion hardware, the original swing arms provide the termination points.
- Have your techs go around before the cutover and tighten every screw on every swing arm. They loosen up over 25 years and you are going to bury them under the mounting plate, so you won’t have easy access to them.
- If you use the conversion hardware, you may want to have the techs that will be doing your conversion, build up the conversion racks to familiarize themselves with the hardware.
Cutovers always take time. You will have to allow for however long it takes, but you do have some actions you can take to shorten the time:
- Have your techs pre-survey each enclosure that they will be working in. They need to have a plan.
- If they are hard wiring, where will they put the terminal blocks
- Can they do any pre-work, or rip out of abandoned stuff?
- If you are adding relays due to output point power issues, can they be mounted before the conversion?
- Plan your labor. If you have several racks, plan for parallel tech teams to do the work.
- For start-up & debug, plan enough techs to support debug and enough operators to put the system through its paces. You will want at least two of each so one team can move forward while the other team debugs the last issue. Oh, and you may want your programmer on that team as well.
- Due to both budgetary and time constraints you will probably be reworking your existing enclosures, as opposed to building new enclosures and pulling the wires back.
- If the techs are hard wiring the new modules, you need to have new and old cutsheets to show screw-to-screw mapping for each point.
Now that you have gone through the process once, you are ready to loop back to the beginning and start again. Taking the time for a second pass, will guarantee a much better approach and implementation. Good Luck with your upgrade. Please, let me know if Hallam-ICS can help you.
If you have any questions, please email me at rracine@hallam-ics.com or contact us here:
About the author
Ray has retired from Hallam-ICS, but his contributions to the company continue to be valued.
Read My Hallam Story
About Hallam-ICS
Hallam-ICS is an engineering and automation company that designs MEP systems for facilities and plants, engineers control and automation solutions, and ensures safety and regulatory compliance through arc flash studies, commissioning, and validation. Our offices are located in Massachusetts, Connecticut, New York, Vermont and North Carolina and our projects take us world-wide.
You May Also Like
These Related Stories
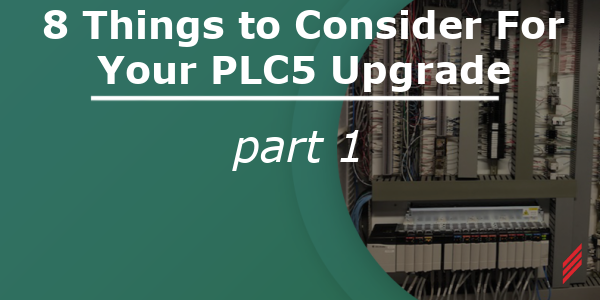
8 Things to Consider for Your PLC5 Upgrade- Part 1
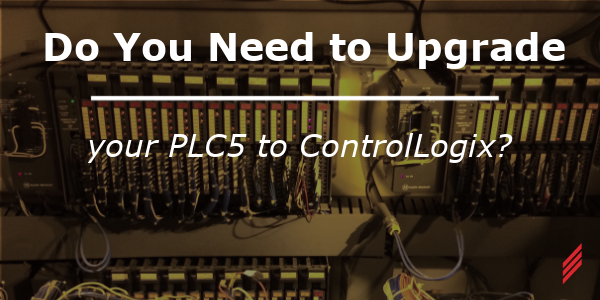
Do You Need to Upgrade Your PLC5 to ControlLogix?
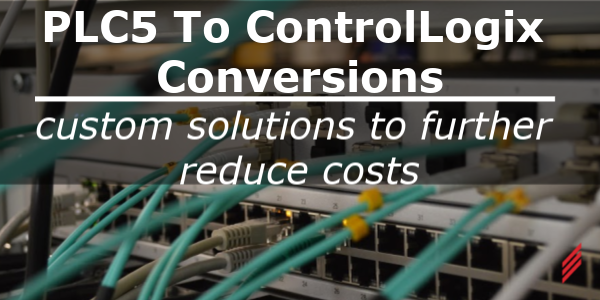
No Comments Yet
Let us know what you think