Control System Project Implementation One Size Does Not Fit All
by Ray Racine on Nov 17, 2022 10:30:00 AM
In a world where we are increasingly trying to standardize and document our project approach, we need to be ever more careful that we do not try to deliver the same bill of goods to every client. Each client has unique needs as regards their Control Systems.
In the process industries, we encounter highly sophisticated Semi-Conductor and Pharmaceutical clients. We work with Food Producers, and Water Treatment Facilities. We work with manufacturers working on small margins and those with much larger automation budgets.
In process controls, ever increasing integration between PLCs, HMIs or SCADAs, VFDs, Smart Valves, Networked Valve Manifolds, is possible. Every year, the vendors are offering new and better ways to tie these pieces of hardware into elegant systems. But, they are not for all of our clients.
In one facility, we worked with the client to integrate their Variable Frequency Drives to their PLCs (same manufacturer). The Ethernet interface between the drives and the controllers was fantastic. A single CAT6 cable replaced hard-wired, Start / Stop / Fault / Reset / Speed Command & Speed Feedback. That’s a lot of wire and a lot of terminations. It also saved a lot of I/O modules in the PLC.
This site has a lot of great technicians on staff. They fix electrical, pneumatic, mechanical systems, and do it quickly to keep production up and running. Unfortunately, when the first of the networked drives failed at 2 AM, they did what they always do. They went to the shelf; they found the same model and horsepower drive. They removed the old drive, installed the new drive, changed a dozen or so drive parameters (IP address / FLA etc.). They reconnected the CAT6 and??? Nothing! Why?
As it turned out, the replacement drive was a different firmware revision. It took a controls guy going into the PLC program to reconcile this issue. By removing the hard-wired signals, we had moved this job from one that an off-shift technician could handle, to one that also required calling in a controls guy. The line was not up as quickly. So, did we really make the system better?
Are drives really better than motor starters? We all know the energy spikes that we can remove with drives. But when a small manufacturer has a simple system, might we better serve them by making their control systems as simple and self-maintainable as possible? Motor Starters are pretty bullet proof. The average small town Waste-Water Treatment Facility probably has one operator that often runs a couple of these small facilities. He or she has had to get pretty flexible in keeping systems running; but they probably aren’t up to trouble-shooting the programming & drive parameter settings of their systems. Add to that, a lot of them are tech adverse.
It is up to a good Control System Contractor to know their client. If you have a big Pharma client with a full time control staff, then install all the really cool networking and drives and valve manifolds you want; but define with their control group – up front – which networks and systems they want to support. These tightly integrated systems will serve them very well and will provide great visibility on their Operation Technology network. Their 20-something new engineers can look at a VFD on their phone and see why it failed. The information available from these systems in nothing less than the stuff of Science Fiction from 30 years ago.
Deploying that same system on a small manufacturer with no technical staff, is an awful idea. That client budget cannot support $8000 processors, and they do not have a maintenance budget that can support costly call-ins that only the Controls vendor can support. They want systems that can, mostly, be supported by their local electrician. Some of these Tech./Electrical guys do carry a laptop; so if you select a platform with free software, they might be able to debug it or at least provide good local eyes on a system to turn a service call with travel into a service call while sitting at your desk.
As we Control System Integration firms grow more young engineers into our ranks, we need to remember that they have always had lots of tech. My guess is that they will be tempted to introduce as much tech as possible into their systems if left unchecked. It is up to our “more seasoned” staff, to make sure that we teach these young engineers which clients benefit from the high-end, elegant solutions, and which will benefit from seemingly clunkier, but more supportable systems. Sometimes KISS (Keep It Simple Sam) is much better.
Daniel Craig and Tom Cruise do not wear off-the-shelf suits. Part of the reason they look so good in their roles is that each of those fantastic suits is tailored specifically to fit them. (That and they’re just good looking guys). As Control System providers, we need to tailor our systems to the actual client – not just treat all of our clients as if they all have the same set of needs.
It is important that we keep focus on our Quality Management Systems, to assure a consistent approach to and documentation of our projects. These systems are a framework, and do not dictate that the project deliverables need to look the same. When it comes to your final design & implementation - know your clients. Make sure the system you tailor for them, is the one they need and can support. These “tailored” systems will fit each client. When it comes to Control Systems – One Size Fits Only One Client.
About the Author
Ray has retired from Hallam-ICS, but his contributions to the company continue to be valued.
Read My Hallam Story
About Hallam-ICS
Hallam-ICS is an engineering and automation company that designs MEP systems for facilities and plants, engineers control and automation solutions, and ensures safety and regulatory compliance through arc flash studies, commissioning, and validation. Our offices are located in Massachusetts, Connecticut, New York, Vermont and North Carolina and our projects take us world-wide.
You May Also Like
These Related Stories
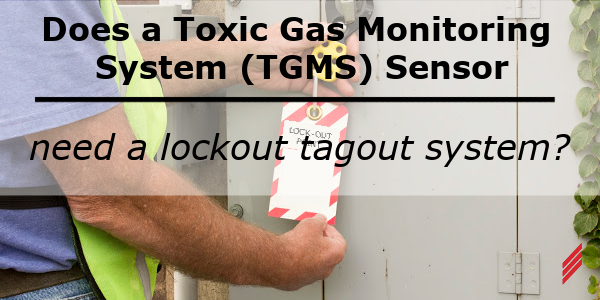
Does a Toxic Gas Monitoring System (TGMS) Sensor Need a Lockout Tagout System?
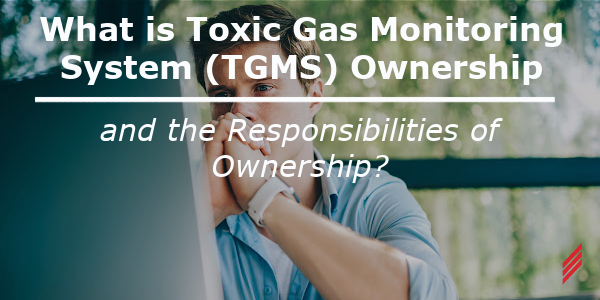
What is Toxic Gas Monitoring System (TGMS) Ownership and the Responsibilities of Ownership?
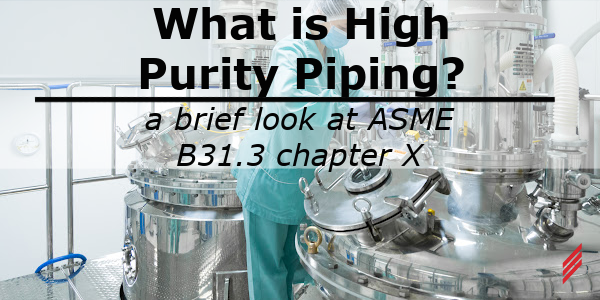
No Comments Yet
Let us know what you think