Demystify VFD Cable Requirements: Standards, Benefits, and Drawbacks
by Jeff Babineaux, PE on May 2, 2024 10:30:00 AM
It’s hard to tell someone that they need a VFD cable when there isn’t a code or standard to tell us what that is. Telling someone only that they need a VFD cable then leaves it up to a vendor or cable manufacturer, and not all of these are created the same. This article will focus on the science behind what makes these cables necessary, when they become necessary, and how to make sure that the cable that you get addresses the concerns you have in your particular application.
Key Concepts
Before we start, there are three key concepts that drive the conversation on VFD issues. The first is electro-magnetic interference, or EMI. The two types that we primarily concern ourselves with are magnetically-coupled (or inducted), and capacitively-coupled. For the former, the cable can end up acting like an antenna, broadcasting or receiving noise that interferes with alarms and other sensitive electronics. For the latter, long parallel runs can induce a voltage in the adjacent cable, leading to dangerous voltage in a cable that might assumed to be locked out and deenergized. Akribis Systems gives a great, short discussion on EMI in drives on YouTube (and links to a longer thesis from MIT on the subject), however they do refer to proper grounding as only a single point. While this makes sense for controls, we will see later why grounding at both ends for VFD supply cables is preferred.
The second is reflected, or standing wave voltage. This is caused by the action of a square wave being sent down a conductor and made worse by improper connections. BTC Instrumentation gives a great demonstration of this on YouTube. Southwire’s presentation on YouTube also provides a reference to an IEEE paper that shows peak voltages in excess of typical THHN insulation characteristics (Southwire 1).
The third and final key concept is common-mode currents, or currents realized in motors due to the common-mode voltage of each phase being controlled by overlapping switching frequencies. VFDs.org provides a great overview showing how this current leaks through bearings instead of going back down the conductors, damaging the motor.
Defining VFD Cables
With that out of the way, what exactly is a VFD cable, and who says we need one? While there is no standard, we do have some typical elements of construction. VFD cables will typically be comprised of a jacket, an overall shield, insulated conductors, and a symmetrical or 3+3 design using three equipment grounding conductors (EGCs) instead of the single EGC in typical multi-conductor cables (Southwire 1). The 2018 edition of NFPA 79, Electrical Standard for Industrial Machinery, had a list of cables in 4.4.2.8 that were allowed for circuits provided from power conversion equipment that were separate from the requirements in chapter 12 for conductors, cables, and flexible cords. Helukabel mentioned in their technical article that this might mean that future revisions would provide better definitions for what is needed in a VFD cable, however 4.4.2.8 has since removed this in more recent editions. Protecting our motors from VFD noise, then, is up to us, and is not as simple as making sure that an installation is up to code.
Fixing the Problems that VFDs Create
So what types of problems are VFD cables are trying to solve? There are several, but they all start with the VFD’s output signal. High-frequency pulse-width modulated (PWM) signals generate noise. This noise takes the form of magnetically or capacitively coupled EMI which is a problem of higher frequency output in the former, and from long parallel runs in the latter. The fast switching of these square-wave PWMs generate a reflected wave or standing wave voltage that is a problem of cable length. The fast-switching frequencies across several phases results in a common-mode current that threatens motor bearings. These are briefly discussed above in the key concepts, and more information is found at the end of the article for further reading. These problems can show up as drive tripping, nuisance tripping in nearby devices, motor insulation failure, motor bearing failure, noise in adjacent equipment, false alarms, shock hazards, and cable failure.
Combatting the EMI generated from VFDs leads to a discussion on shielding that often gets confused with shielding discussions for controls. Control cables typically recommend grounding at one end only. This reduces issues from having different ground potentials at each end that could result in current flowing on the ground. Unlike control wiring, a VFD cable’s shield is intended to carry common mode current noise in addition to noise from magnetically-induced EMI (Southwire 2). To ensure that common-mode current noise has a continuous current back to the source and that magnetically-coupled noise is effectively reduced, the shield can be either a copper ribbon-type for cables that don’t move much, or a copper braided shield should be used for cables requiring regular flexing. In addition to terminating at both ends, special considerations need to be made for VFD cables that extend through an intermediate point to the motor, as is the case with local disconnect switches at the motor, out of sight of the VFD itself. Not properly carrying this common-mode noise current back to the source is one cause of motor bearing and insulation failure (Southwire 1).
Standing wave voltages can be combatted in many ways, but one consideration is making sure that the cable is made to withstand the application. 2021 edition of NFPA 79, section 4.4.2.8 requires that cables are suitable for the electrical power characteristics of the power conversion equipment. VFD cable manufacturers have been able to prove that the standing wave voltages seen on these drives can be 2 to 2.4 times the input voltage, leading to a breakdown in thermoplastic insulations where thermoset insulations can withstand (Southwire 1*, TPC Wire, Helakubel).
*Actual study referenced in Southwire 1 refers to Riding the Reflected Wave – IGBT Drive Technology Demands New Motor and Cable Considerations (IEEE).
Speaking of the common mode, the use of symmetrical grounds addresses a similar problem to the common-mode voltage. Just as common-mode current means that the sum of phase currents does not equal zero, the sum of the ground currents will also not cancel. When these travel down the same EGC, this increase in ground current means that normal sizing rules for EGCs can be inadequate (Southwire 1). Using symmetrical grounds prevents the additive ground current issue and is a more practical construction than oversizing the EGC and making the cable less flexible.
Drawbacks and Limitations of VFD Cable, Partial Solutions
Are they necessary, though? Common complaints are that VFD cables are expensive, inflexible, and take more time to install over single-conductor or unshielded multiconductor cables. This is probably why Peter Cox estimates in a Belden article that of the applications that should be using VFD cable, fewer than 20% are’ (Belden)
As mentioned in the discussion on symmetrical grounds, VFD cables need all the help they can get to increase their flexibility and ease of installation. A braided shield goes a long way, but careful consideration needs to be made when looking at the bend radius of VFD cables compared to junction box sizing, condulets, and wire installation in narrow gutters. Moreover, the shielding and insulation in VFD cables don’t actually reduce the reflected wave magnitude or the harmonics produced by the VFDs (Southwire 1). What do you actually get for your money when you buy these? It’s possible you haven’t seen any issues with noise, and won’t until something is installed close enough to be affected. Actual wear on the motor from common-mode current might not show up for months. For these reasons, the benefits of properly installing VFD cables might not be apparent, and other partial and cheaper solutions might be more attractive.
One partial solution is the installation of wires in metallic conduit. This mechanical solution might be good enough to address EMI shielding, the inspection and maintenance of this doesn’t get the attention of electrical shielding, and improper conduit installations can often be missed. Motor termination kits can help to reduce the reflected wave voltages, and a filter is a more expensive solution that reduces noise but does not eliminate EMI the way proper shielding does.
NEC, NFPA 79, and the Manufacturer
The final consideration to the question of whether a VFD cable is actually required goes back to NEC 110.3(B): “Listed or labeled equipment shall be installed and used in accordance with any instructions included in the listing or labeling.” VFD manufacturers recognize the harmful effects of power conversion equipment, and have written instructions into their installation manuals and guidelines for using VFD cables to reduce these effects on the motors they control. NFPA 79 4.4.2.8 restates this when talking about conductors supplying power to industrial machinery, and it bears repeating here.
Conclusion
VFD cables make a difference, fixing problems where the root cause is not always obvious. In Southwire’s webinar, the installation of VFD cables solved problems with drive trips, motor failures, controls and communications issues that chokes couldn’t fix. (Southwire 1) VFD.com presented a situation where servo motors not properly grounded back to the VFD would not autotune. Belden mentioned in an article that parallel unshielded feeders caused controls issues with batch weights to a mixer.
Cable manufacturers are attempting to create products that address the issues that VFD output signals create. There are guidelines from the VFD manufacturers on how these should be implemented. In the absence of input from the VFD manufacturers, cables should be selected that mitigate EMI, withstand reflected-wave voltages, and safely carry common-mode current back to the source.
Are you looking for more information on the value and requirement of VFD cables? Have you had a similar experience? Let us know!
Further Reading
Akribis. Electromagnetic Interference & How to Reduce It, Akribis Systems (YouTube) https://youtu.be/eLOutoWoDNg
Belden. When Should You Use VFD Cable? https://www.belden.com/Blogs/Industrial-Automation/2020/05/06/when-to-use-vfd-cable
BTC Instrumentation. Reflected Waves on a Cable, BTC Instrumentation (YouTube), https://youtu.be/zrDxSM91Jcg
Helukabel. Benefits of VFD Cables Over THHN: Extending the Life of Your Automated Equipment, https://www.helukabel.com/publication/us/technical_articles/vfd-or-thhn_final_v2.pdf
Mike Holt. VFD Cable - Worth It? https://forums.mikeholt.com/threads/vfd-cable-worth-it.135835/
PLCtalk. When to Use VFD Cables, https://www.plctalk.net/qanda/showthread.php?t=120797
Reddit. VFD cable experiences with effectiveness/benefits. https://www.reddit.com/r/PLC/comments/124nm35/vfd_cable_experiences_with_effectivenessbenefits/
Southwire 1. VFD Cable: Essential or Overkill? with Southwire, https://youtu.be/N_kfi61hC6o?si=NhLAOngfs0Cf8Scg
Southwire 2. Begin with the End in Mind – Proper VFD Cable Termination, https://www.southwire.com/medias/sys_master/related-pdfs/related-pdfs/he5/h8e/8868033429534/Begin-with-the-End-in-Mind-Proper-VFD-Cable-Termination.pdf
TPC Wire. What is VFD Cable and Why Does It Matter? https://www.tpcwire.com/blog/vfd-what-it-is-and-why-using-vfd-cable-matters
VFD.com. When to Use VFD Cable On Variable Frequency Drives, https://variablefrequencydrive.com/when-to-use-vfd-cable/
VFDs.org. Influence of VFD on motor shaft voltage and bearing currents, http://www.vfds.org/influence-of-vfd-on-motor-shaft-voltage-and-bearing-currents-984683.html
About the Author
Jeff has a B.S. in Electrical Engineering from Louisiana Tech University. Prior to coming to Hallam-ICS, Jeff had 7 years of experience working in prefab construction for mechanical and electrical buildings and skids. He holds a professional engineering license in multiple states, participates in all phases of the project design from concept through construction, and cooks a mean gumbo.
Read My Hallam Story
About Hallam-ICS
Hallam-ICS is an engineering and automation company that designs MEP systems for facilities and plants, engineers control and automation solutions, and ensures safety and regulatory compliance through arc flash studies, commissioning, and validation. Our offices are located in Massachusetts, Connecticut, New York, Vermont and North Carolina and our projects take us world-wide.
You May Also Like
These Related Stories
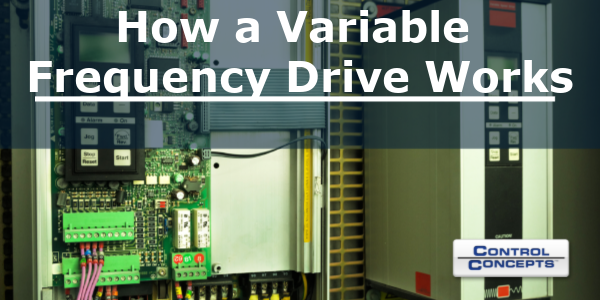
How a Variable Frequency Drive Works
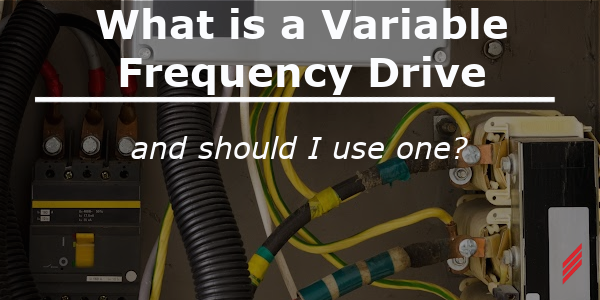
What is a Variable Frequency Drive, and Should I Use One?
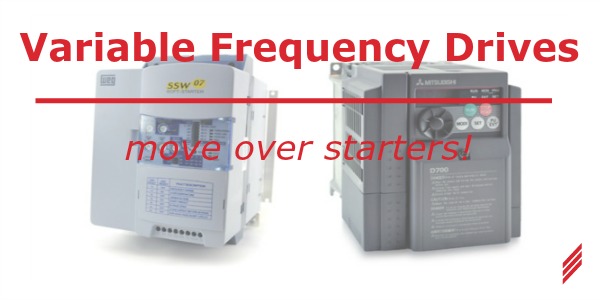
No Comments Yet
Let us know what you think