How to Organize Your Safety Requirement Specification (SRS)
by Dan Maxwell on Jun 15, 2023 10:30:00 AM
In our last discussion, we established a framework for the Safety Requirement Specification (SRS) by identifying the first 2 steps as defining the Inputs and Outputs. The next step in the process of completing an SRS is to organize the document in a way that is most useful for the stakeholders. The document must be easy to digest and navigate. This blog will present the top choices that will make your SRS the best possible representation of your TGMS functionality.
At this point in your thought process, you should have a good idea how big/complicated an SRS you are wrestling with for your particular TGMS. Here is a list of some commonly seen conditions that may have an impact on the organization of your SRS:
- Distinct Stakeholder Groups
- Multiple Buildings
- Multiple Levels in a Building
- Multiple Zones (typically defined as having separate air systems) in a Building
- Ambient vs. Exhaust monitoring points
Before we begin to discuss the impacts of the above conditions, it is important to note that Safety Requirement Specifications should be consistent throughout. By breaking an SRS into sections to make it better organized, and then proceeding to the details, the resulting SRS may not be uniform. This can be avoided by working on the details first and then reorganizing the SRS. Alternately, vigilance during the detail development can assure the consistency.
Distinct Stakeholder Groups – Each stakeholder group is going to have input into how the TGMS should operate. By separating an SRS into pages or sections focused on the needs of a specific stakeholder group, you can maintain the focus of the group through the development and review process. Various stakeholder processes or equipment may have unique needs that need to be addressed in an SRS.
Multiple Buildings – It is difficult to interpret a document if it is so general that users can say, “Well we don’t have that in our building. Why do we need to be concerned with issue X?” Different buildings often represent different stakeholder groups but they may also represent different logic solvers for the TGMS itself. Often a TGMS will be built on a single PLC platform for each building.
Multiple Levels in a Building – A common example of a TGMS in a building with multiple levels is a research facility with a first floor Clean Room and upper stories with traditional wet/dry labs. Clean Spaces and lab spaces may have very different gas detection applications and annunciation needs. Grouping an SRS by level may be a good starting point.
Multiple Zones - This topic is very similar to multiple stakeholders. Zones for Utility Support Equipment, Gas Storage Areas, and Clean Spaces all have unique needs. By organizing the SRS with this in mind, it may be more logical for the stakeholders to interpret.
Ambient vs. Exhaust monitoring points – The location type for gas detection points is a very granular level for organizing an SRS and it would typically fall within some set of the preceding topics. The actions identified within the SRS are often different for ambient points vs. exhausted points. The common train of thought is that exhausted detections are still contained.
It is an extensive list of organizational topics to consider. It is also not all-inclusive. Your project is unique and will need to be considered in its entirety to develop the best organizational strategy. It is likely you will reorganize more than once before you are satisfied. Just keep in mind that a consistent document is important to the final implementation of the TGMS.
About the Author
Dan Maxwell is a Senior Project Manager with Hallam-ICS’s Toxic Gas Monitoring team. Dan trained in Mechanical Engineering and has worked in Project Management in the construction and manufacturing sectors before coming to Hallam-ICS in 1999.
Read My Hallam Story
About Hallam-ICS
Hallam-ICS is an engineering and automation company that designs MEP systems for facilities and plants, engineers control and automation solutions, and ensures safety and regulatory compliance through arc flash studies, commissioning, and validation. Our offices are located in Massachusetts, Connecticut, New York, Vermont, North Carolina, Texas and Florida and our projects take us world-wide.
You May Also Like
These Related Stories
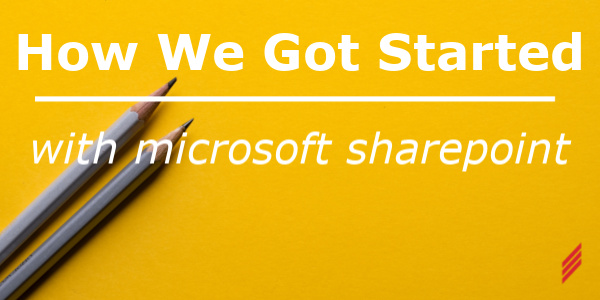
How We Got Started with Microsoft SharePoint
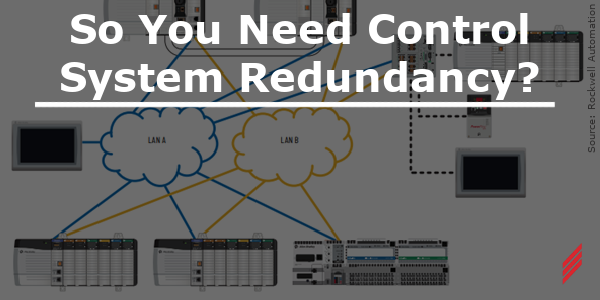
So You Need Control System Redundancy?
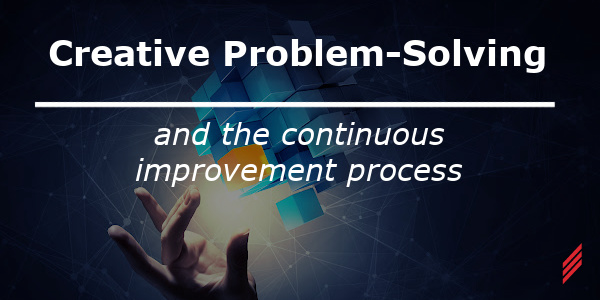
Comments (1)